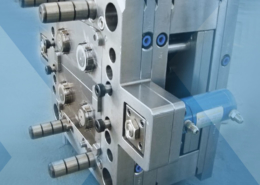
Plastic Process Equipment, Inc. Suppliers Showroom - ppe injection molding
Author:gly Date: 2024-10-15
Contact us via phone or through our contact form. Our team is looking forward to meeting you and addressing your unique requirements!
Our services are designed for established companies with significant buying power, capable of investing in molds and committing to substantial annual injection molding volumes. We aim to partner with enterprises that can leverage our capabilities for large projects and established markets.
In addition to producing complete OEM plastic products, we can optimize existing components by incorporating various additives. These can include fire-retardant additives to enhance safety, anti-static additives to prevent static charging on plastic surfaces, and antimicrobial additives to inhibit the spread of viruses and bacteria. At AKF Plastics, we use the latest and most innovative materials to ensure our products meet the highest standards of quality and functionality.
The Topre Realforce RGB comes with backlit double-shot keycaps. These are one of the product ranges that show a stencil look to the first shot.[4] While sold by Topre, it is not confirmed that Topre manufacture the keycaps themselves.
As your trusted OEM plastics supplier, we offer comprehensive services that cover the entire production process. From initial design and prototyping to full-scale production, assembly and JIT Delivery.
Double-shot moulding is enjoying a slow resurgence in the gamer and enthusiast markets: brands such as Vortex, Tai-Hao and Topre now provide modern backlit double-shot keycaps, and Tai-Hao double-shots are available for sale in a wide variety of colourways in both ABS and PBT plastic. These new product ranges demonstrate a willingness to invest in this technology.
The technicalities of this process vary quite distinctly between manufacturers. In many cases, the process leads to a striped pattern within the keycap formed from the two different coloured plastics. This striped pattern remains even when keycaps are manufactured for engraving or other marking processes, as is clearly visible with Devlin Q series keycaps.
Do you have specific needs for your OEM plastic products? Or would you like to discuss possible solutions with us because you are looking for an experienced and certified injection molding company? AKF Plastics, with its ISO AS9100 and ISO9001 certifications, has many years of experience in the field of injection molding for various industries.
Despite the name, the moulding process is not restricted to two colours: triple and quadruple[2] shot keycaps exist, where two or three different legend colours are present on a single keycap. The use of more than three colours is however quite rare. More commonly, where multiple legend colours are required, the additional colours are provided using pad printing (dye sublimation would be unsuitable with the ABS material used in double-shot moulding). This is especially true where the extra text is printed on the front of the keycap, such as with NeXT keyboards.
AKF Plastics is not only focused on the use of materials that are superior in quality and durability but also on the use of materials that provide the best aesthetic results.
Double-shot moulding, double-shot, dual-injection moulding, two-shot moulding or insert moulding is the process of moulding plastic around a preformed metal or plastic insert. This has been a popular process to create very durable keycaps in the past, used extensively in the 70s and 80s and still found into the 90s. Once a staple of keyboard manufacturing, during the 1990s double-shot moulding faded into obsolescence as keyboards were reduced to a simple commodity.
For over 90 years, AKF Plastics has been at the forefront of the plastics industry, offering innovative, high-quality solutions to our clients. Contact us today to discover how our expertise can benefit your projects
SMK double-shot keycaps have varied in design over time. All their keycap styles have in common a completely solid first shot, without striped bands of colour. Older keycaps (from SMK vintage linear keyboards) had a large first shot (giving thick keycaps), while newer keycaps for SMK second generation switches reduced the size of the first shot. It is not known whether they were produced in-house or outsourced.
Injection moulding is also ideal for the production of complex products consisting of several components or even several materials!
Our mission is to create the best possible injection moulding solutions for plastics for industrial customers, in the most economically, technically and socially responsible manner.
AKF/AGF Injection Moulding Naarden, The Netherlands © ALL RIGHTS RESERVED | BTW: NL807854992B01 | Privacy & Cookies | Webdesign door Brainycloud Marketing ©
Double-shot moulding is suitable for backlighting: the first shot can be made from a translucent plastic. Vortex, Tai-Hao and Topre all offer backlit double-shot keycaps. In Topre's case, the first shot cannot support fully enclosed shapes, giving a stencil-like appearance.[4] Neither Vortex's or Tai-Hao's processes are affected by this limitation.
Vortex are one of the manufacturers of PBT double-shot keycaps. Vortex backlit keycaps use translucent POM for the first shot, and PBT for the second shot.[8] Vortex also offer non-backlit double-shot PBT keycaps.[9]
AKF Plastics can meet the most complex product requirements and is dedicated to collaborating with you to translate your needs into the highest quality OEM injection molding solutions, adhering to international standards across various industries
Our expertise in creating custom OEM plastic parts allows us to deliver solutions that enhance the performance and durability of your products. Whether you need high-precision components or complex assemblies, we have the capabilities to meet your needs.
At AKF Plastics, we specialize in providing comprehensive injection molding solutions exclusively for large-scale national and international enterprises. Our fully automated 24/7 production lines, extensive logistics capabilities, and large storage facilities ensure we can meet the demanding needs of our clients.
ABS is typically chosen because most other plastics shrink too much in the moulding process.[Citation needed] Modern ABS however lacks the desired wear resistance, leading to keycaps that develop shine too readily. However, PBT double-shot keycaps are now produced by both Vortex and Tai-Hao.
The majority of double-shot keycaps are made entirely from ABS plastic. Despite their greater wear resistance, Signature Plastics have confirmed that the majority of Comptec keycaps were nonetheless made from ABS, albeit of different formulations (the plastic formulations have since changed due to regulatory requirements).[3] Older Cherry catalogues show that in 1982, the tall Cherry M7 and Cherry M9 keycaps were made of double-shot Tenite, while their other double-shot keycaps were all ABS.
Cherry produced double-shot keycaps in-house, they discontinued the manufacture of double-shot keycaps in 2011. The tooling was sold to GMK, who resumed manufacture of the parts.
We also serve as an OEM injection molding contractor for other OEM product suppliers. AKF has a broad experience in producing plastic parts for:
As a leading OEM plastics manufacturer, we pride ourselves on our ability to produce a wide range of custom plastic components. Our state-of-the-art facilities and advanced manufacturing techniques enable us to meet the most demanding specifications and quality standards
Until early 2010, Cherry still offered double-shot moulded keycaps as an option for their POS and special-order keyboards. Production ultimately stopped and all keyboards with double-shot moulded keycaps were called off. November 2012, it was announced that German company GMK had acquired the original tooling and moulds[5]. In December 2012, EliteKeyboards offered the first GMK product in the form of a double-shot Cherry Escape key[6].
We provide a complete range of services for original equipment manufacturers (OEM), ensuring that your projects are completed efficiently and cost-effectively. Our services include:
As the name suggests, double-shot moulding is a two-step process. In the first step, the legend or graphics to be placed on the keycap, are moulded in plastic[1]. The plastic insert, resulting from the first step, is then placed into another mould, and plastic is inserted under heat to combine both moulds to a single piece keycap.
Original Equipment ManufacturerAutomotive industryAerospace Building and ConstructionPlastic injection Moulds Machinery PoolAS 9100
As a leading Original Equipment Manufacturer for plastic injection moulded parts, AKF Plastics is dedicated to delivering high-quality, custom plastic solutions tailored to various industries. We focus on precision, innovation, and efficiency to ensure your products meet the highest standards.
Other manufacturers use a wholly or near-wholly solid first shot, that gives keycaps a "nested" or "stacked" appearance when viewed from below. Regardless of the specifics, double-shot keycaps can be identified by observing the underside where both colours are visible.
Tai-Hao are a long-time manufacturer of double-shot keycaps, both Cherry MX mount and Alps mount. Their widely-used TI series is still manufactured to this day, and has been extended to cover PBT keycaps. Tai-Hao keycaps were used by brands including Ortek, Focus Electronic and Northgate Computer Systems.
Comptec were one of the world's leading keycap manufacturers, whose keycaps have been found in a large variety of equipment including the Acorn BBC Microcomputer and Wyse terminal keyboards. Comptec USA became Signature Plastics, who remain a very prominent double-shot manufacturer. Tall Comptec keycaps often feature an inner step that appears to be specific to their manufacturing process.
At AKF Plastics, we have a proven track record in delivering comprehensive solutions for various industries, including aerospace, construction, machinery and equipment manufacturing, the automotive sector, and many others. Our services encompass everything from design and mold development to production and logistics. With decades of experience, we offer speed and efficiency, resulting in competitive pricing and fast turnaround times. Our innovative strategy, Contingency Production™ Planning, ensures uninterrupted production even in uncertain market conditions. Whether you are active in aviation, construction, machinery, automotive, or any other sector, AKF Plastics guarantees reliability, quality, and innovation for all your plastic needs.
While Alps are better known for the dye sublimated keycaps used in Apple keyboards, Alps also produced distinctive double-shot keycaps. Alps are one of the companies whose moulding process did not show stripes of colour within the underside of the keycap. Many double-shot Alps keycaps feature a curious pattern of bars and square holes that aids in their identification.
For example, we have injection moulding machines that can deliver up to 1600 tons of closing force, and a shot weight up to 10,900 grams.
All information about AKF Plastics at a glance. What we do, what we stand for and how we can help you with your injection moulding challenges.
Double-shot keycaps were a standard feature of many vintage keyboards, when keyboards were expected to be expensive. As a result, many manufacturers have produced double-shot keycaps. Only a small number of these product ranges are still known to be in production to this day. However, new product lines have arisen to cater for the gamer and enthusiast markets.
AKF Plastics is your Trusted Partner for High-Volume OEM Plastic Manufacturing. Specializing in large-scale, automated 24/7 production, extensive logistics, and international shipping. Perfect for major enterprises with substantial annual injection molding needs. Do you have a question about materials, injection moulding or a specific OEM product? We are always ready to help you! Contact us via our contact form or call: +31 (0)35 694 5545
GETTING A QUOTE WITH LK-MOULD IS FREE AND SIMPLE.
FIND MORE OF OUR SERVICES:
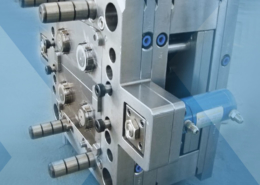
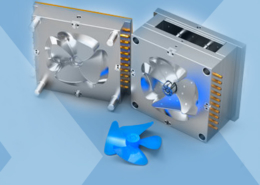
Plastic Molding

Rapid Prototyping
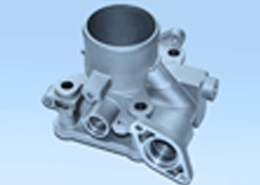
Pressure Die Casting
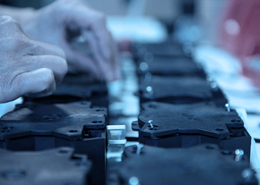
Parts Assembly
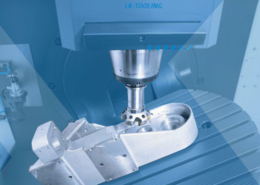