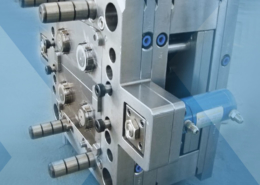
Plastic PET Injection Molding Processing Conditions - Alleycho - petg injection
Author:gly Date: 2024-10-15
Some of the additives used include stabilizers, lubricants, processing aids, pigments, impact modifiers, and fillers. Some features of PVC include low combustibility, toughness (designed to be virtually unbreakable), good weatherability (including good color and impact retention, and no loss in stiffness), and excellent dimensional stability. PVC is highly resistant to oxidizing and reducing agents, and strong acids. However, unplasticised PVC is not recommended for environmental and continuous use above 60 C (140 F). It is not resistant to concentrated oxidizing acids such as sulfuric or nitric acid and is unsuitable for use with aromatic and chlorinated hydrocarbons.
HDPE injection molding is a manufacturing process that involves injecting molten HDPE material into a customized mold cavity. The molten HDPE material is then cooled and solidified,producing precise and high-quality plastic parts. HDPE injection molding process is known for its cost-effectiveness, speed, and ability to produce complex shapes and designs with high precision and consistency.
HDPE is a versatile material that is used in a wide range of applications across various industries. Some common uses of HDPE include:
HDPE molding offers several advantages over other manufacturing processes. It allows for the production of complex designs and intricate shapes with high precision and consistency. It also offers high production rates and is ideal for large volume production runs. Additionally, HDPE molding is a cost-effective process, as it can reduce material waste and labor costs. 1.Versatility: HDPE is a versatile material that can be molded into various shapes and sizes, making it suitable for a wide range of applications. 2.Strength and durability: HDPE has a high strength-to-density ratio, making it strong, durable, and able to withstand harsh environments. 3.Chemical resistance: HDPE is highly resistant to chemicals, making it suitable for use in corrosive environments. 4.Recyclability: HDPE is recyclable and has a low environmental impact, making it a popular choice for sustainable manufacturing practices. 5.Cost-effective: HDPE injection molding is a cost-effective manufacturing process, allowing for the production of high-volume runs of identical parts.
Sungplastic providers that offer custom HDPE plastic parts services. Our company uses HDPE injection molding to produce custom plastic parts according to our customers’ specific requirements.v. Here are some of the steps involved in custom HDPE plastic parts service:
HDPE injection molding has a wide range of applications due to the unique properties of HDPE plastic. Some of the common applications of HDPE injection molding include:
PVC is a relatively stiff flow material and has a narrow processing range. The molecular weight determines the flow characteristics. Higher molecular weight materials are more difficult to process (this could be modified by addition of lubricants). Typically, however, relatively low molecular weight grades are used in molding).
We offer a variety of manufacturing services: Rapid Prototyping, Tool Making, Injection Molding, Product Design and Development, CNC Machining and Metal Stamping. You can choose from a variety of plastics, silicone rubber, or metal for your product. Regardless of mass production or small batch customization, Sungplastic has always been committed to providing assured, efficient and more economical one-stop processing services for your projects.
Rigid (unplasticised) PVC is one of the most widely used plastic materials. It is produced from sodium chloride and natural gas. The repeat chemical structure is vinyl chloride. Additives are mixed with PVC to make it processible. PVC grades produced by suspension or mass polymerization techniques are the major types used for melt processing. PVC is substantially an amorphous material.
There are various types of HDPE plastics that are used for different applications, each with their own unique characteristics. Here are some of the most common types of HDPE plastics and their applications:
It is very important to process the material at the correct melt temperature; otherwise severe problems from decomposition (which produces hydrochloric acid which in turn accelerates decomposition) could result.
HDPE (High-Density Polyethylene) injection molding is a manufacturing process that involves injecting molten HDPE material into a custom-designed mold cavity. The molten HDPE material is then allowed to cool and solidify, creating a finished plastic part.The process is also efficient, cost-effective, and capable of producing complex shapes and designs with high precision and consistency.HDPE molding offers several advantages over other manufacturing processes, including the ability to produce complex and intricate designs, high production rates, and consistent quality of the finished products. It is commonly used in the production of a wide range of plastic products, including bottles, containers, pipes, automotive parts, medical devices, and more.
Injection molded HDPE is a durable and versatile material with excellent chemical and weather resistance, making it suitable for a wide range of applications across industries.
HDPE injection molding is a versatile manufacturing process that can be used to produce a wide range of plastic products with excellent properties and performance.
A: Choosing the right HDPE molding technique depends on several factors, such as the shape, size, and complexity of the product, the required production volume, the material properties, and the cost.
An experienced and knowledgeable partner can help optimize the manufacturing process, reduce costs, improve quality, and accelerate time-to-market, resulting in a better outcome for the client.
Sungplastic is a plastic product manufacturer with rich experience in injection molding. According to the different product development requirements, we flexibly adjust the manufacturing process to achieve high quality, high efficiency and more economical.
HDPE material properties may vary by specific grade and manufacturer. Injection molded HDPE material has some general properties:
Plastic Mold Manufacturing Plastic Injection MoldingRapid PrototypingCNC MachiningSheet Metal StampingPressure Die CastingSilicone & Rubber PartsSurface Finishing
1.Limited temperature resistance: HDPE has a relatively low temperature resistance compared to other materials, making it unsuitable for high-temperature applications. 2.Limited color options: HDPE is typically only available in a limited range of colors, which may not be suitable for all applications. 3.Difficult to bond: HDPE can be difficult to bond with other materials, which may limit its use in certain applications. 4.Limited mechanical properties: HDPE has limited mechanical properties compared to other materials, such as metals, which may limit its use in certain applications where high mechanical strength is required.
A: Challenges of HDPE injection molding include the hygroscopic nature of HDPE, the high melt viscosity of HDPE, and the high crystallization rate of HDPE.
Sungplastic is a reputable manufacturer of high-density polyethylene (HDPE) injection molds and provides comprehensive HDPE injection molding services. Our experienced team of engineers and technicians work closely with our customers to understand their unique needs and provide solutions tailored to meet their specific requirements. We use cutting-edge technology and equipment to design and produce high-quality HDPE injection molds, consistently delivering reliable results. In addition to mold production, we also offer POM injection molding services that include the production of finished POM products such as gears, bearings, and other precision components. Our wide range of injection molded parts caters to various industries. At Sungplastic, we prioritize providing the highest quality products and services. We have strict quality control measures in place to ensure that every product leaving our facility meets the highest industry standards. Furthermore, we offer competitive pricing, guaranteeing our clients the best value for their investment. As your trusted partner for injection molding needs, Sungplastic is committed to excellence and customer satisfaction.
In summary, the various types of HDPE plastics have different characteristics that make them suitable for specific applications. HDPE HMW, Marlex 9006, DOW DMDA-8007 NT 7, and DOW DMDA-8907 NT 7 are all high-density polyethylene (HDPE) resins. They are commonly used in injection molding and blow molding applications due to their excellent processability, impact strength, stiffness, toughness, and environmental stress crack resistance (ESCR).
Water distribution piping, home plumbing, house siding, business machine housings, electronics packaging, medical apparatus, packaging for foodstuffs, etc.
All conventional gate types may be used; pin-point and submarine gates are used for molding small components and fan gates are typically used for thick sections. The minimum diameter of pin-point or submarine gates should be 1 mm and the thickness of fan gates should not be less than 1 mm.
Custom HDPE plastic parts service providers typically work closely with our clients throughout the entire process to ensure the finished part meets their specific requirements. We provide additional services such as material selection, design optimization and prototyping to help customers achieve the best results.
By following these best practices, you can achieve high-quality HDPE injection molded parts with consistent properties and performance.
High-density polyethylene (HDPE) is a type of thermoplastic polymer made from the monomer ethylene.It is a versatile material commonly used in the manufacture of a variety of products. HDPE is known for its high strength-to-density ratio, making it lightweight, strong, and durable.HDPE also has excellent chemical and weather resistance, making it suitable for use in severe environments. HDPE is a recyclable material with low environmental impact, making it a popular choice for sustainable manufacturing practices.
Viewmold company provides injection molding services for your part with PVC plastic material. PVC injection molding processing condition Generic Class PVC (Polyvinyl Chloride) Typical Applications Water distribution piping, home plumbing, house siding, business machine housings, electronics packaging, medical apparatus, packaging for foodstuffs, etc. Injection Molding Processing Conditions Drying Not usually necessary as PVC absorbs very little water. Melt Temperature 160 - 220 C (320 - 428 F) Mold Temperature 20 - 70 C (68 - 158 F) Material Injection Pressure Up to 150 MPa Packing Pressure Up to 100 MPa Injection Speed Relatively slow, to avoid material degradation Runners and Gates All conventional gate types may be used; pin-point and submarine gates are used for molding small components and fan gates are typically used for thick sections. The minimum diameter of pin-point or submarine gates should be 1 mm and the thickness of fan gates should not be less than 1 mm. Sprues should be as short as possible; typical runner sizes are 6 - 10 mm and should have a full round cross-section. Insulated hot runners and certain types of hot sprue bushings may be used with PVC. If you need high quality cutom aluminium casting parts Pls contact us sales@viewmold.com If you need high quality injection mold tooling, Contact us. Chemical and Physical Properties Rigid (unplasticised) PVC is one of the most widely used plastic materials. It is produced from sodium chloride and natural gas. The repeat chemical structure is vinyl chloride. Additives are mixed with PVC to make it processible. PVC grades produced by suspension or mass polymerization techniques are the major types used for melt processing. PVC is substantially an amorphous material. Some of the additives used include stabilizers, lubricants, processing aids, pigments, impact modifiers, and fillers. Some features of PVC include low combustibility, toughness (designed to be virtually unbreakable), good weatherability (including good color and impact retention, and no loss in stiffness), and excellent dimensional stability. PVC is highly resistant to oxidizing and reducing agents, and strong acids. However, unplasticised PVC is not recommended for environmental and continuous use above 60 C (140 F). It is not resistant to concentrated oxidizing acids such as sulfuric or nitric acid and is unsuitable for use with aromatic and chlorinated hydrocarbons. It is very important to process the material at the correct melt temperature; otherwise severe problems from decomposition (which produces hydrochloric acid which in turn accelerates decomposition) could result. PVC is a relatively stiff flow material and has a narrow processing range. The molecular weight determines the flow characteristics. Higher molecular weight materials are more difficult to process (this could be modified by addition of lubricants). Typically, however, relatively low molecular weight grades are used in molding). Shrinkage is fairly low (0.002 - 0.006 mm/mm or 0.2 - 0.6%). If you need to look for more plastic resin injection molding processing condition, could you please click it. If you need high quality plastic extrusion services, Pls contact us sales@viewmold.com If you need high quality sheet metal parts, Pls contact us sales@viewmold.com The following is other plastic processing condition: ABS injection molding processing condition, HDPE injection molding processing condition, LDPE injection molding processing condition, PA12 injection molding processing condition, PA6 injection molding processing condition, PBT injection molding processing condition, PC-ABS injection molding processing condition, PC-PBT injection molding processing condition, PEI injection molding processing condition, PETG injection molding processing condition, PMMA injection molding processing condition, POM injection molding processing condition, PPE injection molding processing condition, HDPE injection molding processing condition, PP injection molding processing condition, PS injection molding processing condition, PVC injection molding processing condition, SAN injection molding processing condition,
A: The most common types of HDPE molding include injection molding, blow molding, and rotational molding. Each process is used to create different types of products with unique shapes, sizes, and properties.
Sprues should be as short as possible; typical runner sizes are 6 - 10 mm and should have a full round cross-section. Insulated hot runners and certain types of hot sprue bushings may be used with PVC.
There is no doubt that HDPE (High-Density Polyethylene) can be injection molded. In fact, injection molding process is one of the most common and widely used methods for manufacturing HDPE products. HDPE is a popular choice for injection molding due to its excellent strength-to-density ratio, chemical resistance, and ability to be molded into complex shapes with high precision and consistency. The process is also cost-effective, efficient, and capable of producing high-volume runs of identical parts. In short, HDPE injection molding is a versatile and efficient manufacturing method that is commonly used to produce a wide range of products, including packaging, automotive parts, medical devices, and more.
GETTING A QUOTE WITH LK-MOULD IS FREE AND SIMPLE.
FIND MORE OF OUR SERVICES:
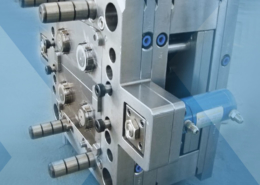
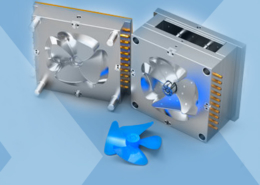
Plastic Molding

Rapid Prototyping
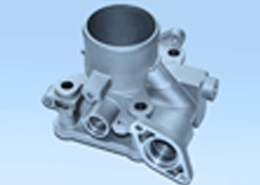
Pressure Die Casting
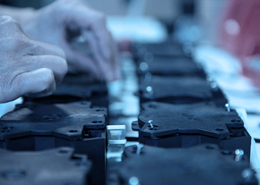
Parts Assembly
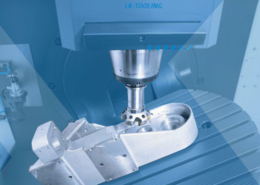