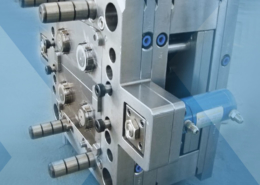
Exploring the World of Plastic Casting Molds
Author:gly Date: 2024-06-08
Plastic casting molds, often overshadowed by the final products they help create, play a pivotal role in numerous industries, silently shaping our everyday lives. From the meticulous design phase to the precision manufacturing process, these molds are the unsung heroes behind the scenes, ensuring the replication of intricate details with unmatched accuracy. This article delves into the multifaceted realm of plastic casting molds, unveiling their significance, intricacies, and potential future developments.
Understanding Plastic Casting Molds
Plastic casting molds constitute a fundamental component of the manufacturing process, enabling the mass production of intricate plastic parts with consistent quality. These molds, typically made from metals such as aluminum or steel, serve as negative impressions of the desired product, into which molten plastic is injected and cooled, resulting in the formation of the final component.
Design and Fabrication
The design and fabrication of plastic casting molds demand a meticulous approach, integrating cutting-edge CAD (Computer-Aided Design) software with precision machining techniques. Engineers meticulously craft each mold to accommodate the specific geometry and functional requirements of the intended product, ensuring optimal performance and longevity.
Material Selection
The choice of material for casting molds is a critical consideration, influencing factors such as durability, thermal conductivity, and cost-effectiveness. While steel molds offer superior durability and heat resistance, aluminum molds are preferred for their lightweight nature and faster cooling times, especially in high-volume production settings.
Surface Finishing
Surface finishing techniques play a crucial role in enhancing the quality and aesthetics of plastic components. Molds are meticulously polished to achieve smooth surface finishes, minimizing defects such as sink marks and flow lines. Advanced surface treatments, including chemical etching and electroplating, further enhance the durability and wear resistance of molds, prolonging their service life.
Applications Across Industries
Plastic casting molds find widespread applications across diverse industries, ranging from automotive and aerospace to consumer electronics and medical devices. Their versatility and adaptability make them indispensable in the production of a myriad of components, including intricate housings, intricate enclosures, and precision components.
Automotive Industry
In the automotive sector, plastic casting molds are instrumental in the production of lightweight yet durable components, such as bumpers, dashboards, and interior trim panels. The ability to replicate complex geometries with precision ensures the seamless integration of these components into modern vehicle designs, enhancing both aesthetics and functionality.
Consumer Electronics
In the realm of consumer electronics, plastic casting molds facilitate the production of sleek and ergonomic enclosures for smartphones, tablets, and wearable devices. The demand for miniaturization and intricate designs necessitates the use of high-precision molds capable of capturing fine details and maintaining tight tolerances.
Medical Devices
Plastic casting molds play a pivotal role in the medical device industry, where precision and reliability are paramount. From intricate surgical instruments to complex diagnostic equipment, these molds enable the production of sterile and biocompatible components essential for medical applications, contributing to advancements in healthcare technology.
Challenges and Innovations
Despite their critical role, plastic casting molds face various challenges, ranging from mold degradation and wear to the optimization of production processes. However, ongoing advancements in materials science, additive manufacturing, and process optimization are paving the way for innovative solutions to address these challenges and enhance the efficiency and sustainability of mold manufacturing.
Advanced Materials
The development of novel materials, such as high-performance thermoplastics and hybrid composites, presents new opportunities for enhancing the performance and longevity of plastic casting molds. These materials offer superior mechanical properties, chemical resistance, and thermal stability, allowing for the production of molds capable of withstanding harsh operating conditions and prolonged use.
Additive Manufacturing
Additive manufacturing, commonly known as 3D printing, is revolutionizing the design and production of plastic casting molds. By harnessing the capabilities of additive manufacturing technologies, engineers can rapidly prototype complex mold designs, optimize cooling channels for enhanced efficiency, and incorporate conformal cooling features to reduce cycle times and minimize part defects.
Process Optimization
Process optimization plays a pivotal role in maximizing the efficiency and cost-effectiveness of plastic casting mold manufacturing. Advanced simulation tools enable engineers to analyze and optimize mold designs, predict manufacturing defects, and fine-tune process parameters to achieve optimal performance and quality. Additionally, the integration of automation and robotics streamlines the manufacturing process, reducing lead times and enhancing productivity.
Conclusion
In conclusion, plastic casting molds represent a cornerstone of modern manufacturing, enabling the efficient and cost-effective production of a wide range of plastic components. From their intricate design and fabrication to their diverse applications across industries, these molds play a pivotal role in shaping the world around us. While they face various challenges, ongoing innovations in materials science, additive manufacturing, and process optimization promise to further elevate the capabilities and sustainability of plastic casting mold technology, driving continuous advancements in the field. As we look towards the future, it is imperative to recognize the significance of plastic casting molds and invest in research and development efforts to unlock their full potential in shaping tomorrow's world.
GETTING A QUOTE WITH LK-MOULD IS FREE AND SIMPLE.
FIND MORE OF OUR SERVICES:
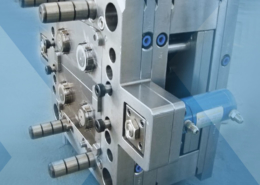
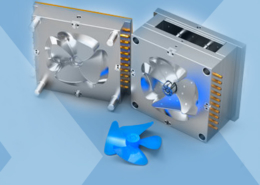
Plastic Molding

Rapid Prototyping
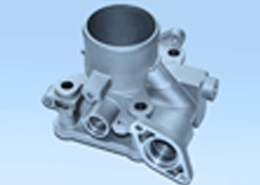
Pressure Die Casting
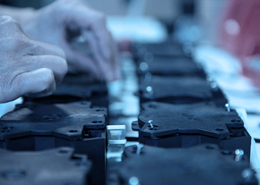
Parts Assembly
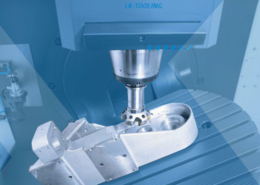