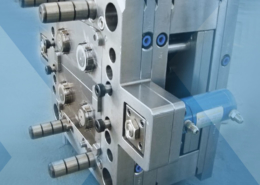
Exploring the World of Plastic Bucket Moulds: Innovation and Application
Author:gly Date: 2024-06-08
Plastic bucket moulds represent a cornerstone in the manufacturing industry, facilitating the production of durable and versatile containers for various purposes. This article aims to delve into the intricacies of plastic bucket moulds, offering insights into their design, manufacturing processes, applications, and future trends.
Introduction to Plastic Bucket Moulds
Plastic bucket moulds play a crucial role in the production of plastic buckets, pails, and containers used in industries ranging from agriculture and construction to food and beverage packaging. These moulds enable manufacturers to produce high-quality, customizable products that meet the diverse needs of consumers and businesses worldwide. Understanding the design and manufacturing processes of plastic bucket moulds is essential for appreciating their significance in modern manufacturing.
Design Considerations and Engineering Principles
Material Selection
The choice of material for plastic bucket moulds depends on factors such as durability, thermal stability, and moulding cycle times. Common materials used for mould construction include steel, aluminum, and composite materials. Each material offers unique advantages in terms of cost, longevity, and machinability, influencing the overall performance and lifespan of the mould.
Mould Design and Optimization
Designing an efficient and effective plastic bucket mould requires careful consideration of factors such as part geometry, wall thickness, and draft angles. Advanced CAD/CAM software enables engineers to create intricate mould designs with precise dimensions and features. Optimizing the mould design for uniform cooling and minimal cycle times is essential for achieving high productivity and consistent part quality.
Injection Moulding Process
The injection moulding process for plastic bucket production involves several stages, including material preparation, mould filling, cooling, and ejection. During mould filling, molten plastic is injected into the cavity under high pressure, ensuring complete filling and minimal defects. Proper cooling is crucial for achieving uniform part quality and dimensional accuracy, while efficient ejection mechanisms facilitate the removal of finished parts from the mould.
Applications and Industries
Construction and Industrial Use
Plastic buckets find extensive use in the construction industry for storing and transporting materials such as paints, adhesives, and chemicals. Their durability, lightweight design, and resistance to corrosion make them ideal for harsh construction environments. Additionally, plastic buckets are widely used in industrial settings for storing lubricants, solvents, and other fluids.
Food and Beverage Packaging
In the food and beverage industry, plastic buckets serve as convenient and hygienic packaging solutions for products such as sauces, condiments, and dairy products. Food-grade plastic materials and compliance with regulatory standards ensure the safety and integrity of packaged goods. Plastic bucket moulds enable manufacturers to produce containers of various sizes and shapes to meet diverse packaging requirements.
Agricultural Applications
Plastic buckets play a vital role in agriculture for tasks such as harvesting, storage, and transport of crops and produce. From collecting fruits and vegetables in the field to packaging fertilizers and pesticides, plastic buckets provide practical and cost-effective solutions for agricultural operations. Their lightweight construction and ergonomic handles enhance efficiency and ease of use in farming activities.
Future Trends and Innovations
The future of plastic bucket moulds lies in embracing sustainable materials, advanced manufacturing technologies, and digital integration. Biodegradable and recycled plastics offer environmentally friendly alternatives to conventional materials, addressing concerns about plastic pollution and resource depletion. Additive manufacturing techniques such as 3D printing enable rapid prototyping and customization of mould designs, reducing lead times and production costs. Furthermore, digital twins and predictive maintenance systems enhance the efficiency and reliability of plastic bucket moulding processes, paving the way for smart and connected manufacturing ecosystems.
Conclusion
In conclusion, plastic bucket moulds play a vital role in modern manufacturing, enabling the production of durable, versatile containers for various applications. Understanding the design, manufacturing processes, and applications of plastic bucket moulds is essential for appreciating their significance in diverse industries. Embracing innovation and sustainability is key to driving progress and shaping the future of plastic bucket moulding technologies.
GETTING A QUOTE WITH LK-MOULD IS FREE AND SIMPLE.
FIND MORE OF OUR SERVICES:
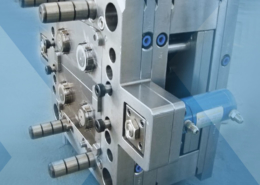
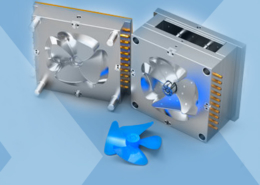
Plastic Molding

Rapid Prototyping
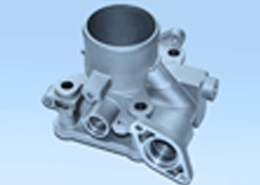
Pressure Die Casting
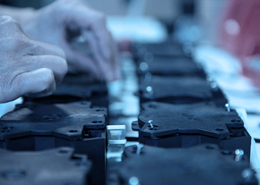
Parts Assembly
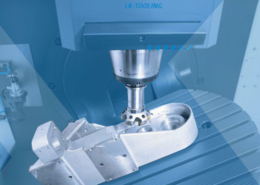