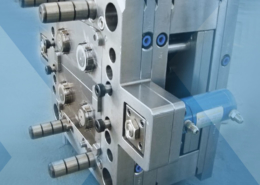
Plastic Injection Moulding Products | Comprehensive Guide | - plastic molded pro
Author:gly Date: 2024-10-15
, we prioritize Stringent Quality Control and Regulatory Compliance. Our operations underscore the importance of ensuring Patient Safety and delivering high-quality medical products through our state-of-the-art injection molding facilities.
It often occurs on the back of a reduced bosom column or ribs, or stress marks are reduced due to high core and thimble design.
It is easy to occur at the corner of thin wall of molded product or at the root of thin wall RIB. It is caused by poor force during demolding, improper setting of ejector pin or insufficient draft angle.
such as Marlee – Texen have consistently leveraged technological advancements to deliver high-quality medical injection molding services, providing a seamless blend of quality and efficiency.
Medical injection molding plays a fundamental role in the healthcare industry, touching nearly every sector with its capabilities. Its breadth of application and adaptability have made it an indispensable part of medical manufacturing. For instance,
The range of applications for medical device injection molding is extensive, stretching across diverse medical fields. From implantable medical devices and disposable medical devices to drug delivery devices, Marlee – Texen crafts each component with the utmost precision and compliance with ISO 13485 and FDA standards. They utilize cutting-edge techniques for both short-term implants and long-term implants, ensuring optimal biocompatibility and safety.
As the best medical plastic injection molding company, we use medical molding in the manufacturing of caps, containers, device components, and medical parts. They are needed in high volumes in pristine conditions for patient safety.
Our Material Selection is extensive and industry-leading. Our expertise encompasses everything from robust Plastic Medical Enclosures to flexible Liquid Silicone Rubber (LSR). Our team’s adeptness at High-Temperature Molding ensures we can work with a variety of Polymer Materials to achieve your project’s specific needs.
From Liquid Silicone Rubber (LSR) molding to complex micro-molding processes, we ensure that every enclosure, packaging solution, and component we create meets the highest industry standards.
To uphold this principle, we invest in state-of-the-art biocompatibility testing protocols. Our robust testing ensures that our plastics are not only safe for patient use but also contribute to the efficient operation of the devices they form. In this way, we assure both the quality and safety of our products.
Molds at missing parts can be modified, taking or improving exhaust measures, thickening material, improving gate (enlarge gate, increase gate), increasing injection dose, increasing injection pressure and other measures to improve.
In terms of design, we deploy state-of-the-art tools and equipment to create intricate components and assemblies. Every machine we use is operated by expert manufacturers, proficient in handling delicate materials like silicone, vital in the creation of a myriad of implants and medical device parts.
Thin-walled injection molding is defined as a thin-walled injection molding when wall thickness of molded plastic part is less than 1 mm (or 1.5 mm), or t/d (thickness t of plastic part, diameter d of plastic part, for disc-shaped plastic parts) is less than 0.05 .
process, has transformed the medical industry. This advancement ensures more efficient operation of the mold flow analysis system, leading to more precise and consistent results. It facilitates the development of medical product components, reducing the margin of error and waste during production.
Short shot refers to incomplete quality defect of plastic part due to incomplete filling of mold cavity, that is, melt has set before filling is completed.
Requirements for raw materials: large flow length, high impact strength, high thermal deformation temperature, high thermal stability, low directivity, and good dimensional stability; also consider low temperature impact rigidity, flame retardancy, mechanical assembly and appearance quality of plastic materials.
Our team’s expertise in medical device design ensures that the selection of these materials is tailored to the specific requirements of each project. We believe that every part of the process, from initial prototype design to final delivery, is integral to the successful operation of a medical device.
You can change gate, lighten runner, increase cold area of runner, increase gate, and add bite on the surface (you can also adjust line by adjusting machine or repairing mold). It can solve problems such as mold temperature, reducing injection speed and reducing injection pressure.
During design, you can reduce or change position of welding line by reducing number of gates or changing position of gates to meet design requirements of plastic parts.
Correct ejector pin, set tensioning pin, etc. If necessary, adjust deformation of male mold with bite adjustment, adjust temperature of male and female mold to reduce holding pressure, etc. Adjustment of deformation of small parts mainly depends on pressure and time, and adjustment of large pieces of deformation generally depends on mold temperature.
A robust system of automation also offers the advantage of improved traceability, a key aspect of regulation and compliance in the medical industry. Furthermore, companies like Marlee – Texen employ overmolding techniques, contributing to their recognition as one of the
industry is the adoption and mastery of Micro-Molding. This highly specialized mould design has allowed a significant shift in medical molding innovations. Specifically, it has been instrumental in the production of smaller, more intricate medical components, and the high-precision manufacturing of injection molded parts.
Small parts and corners of finished product cannot be completely formed. Due to insufficient mold processing or poor venting, design defects (insufficient thickness) are caused due to insufficient injection dose or pressure.
You can change inlet, add cold material wells, open vent grooves, or bite male mold surface, or increase material temperature, mold temperature, etc.
Analysis of common defects: Although there are many advantages to thin walled plastic parts, formability of plastic parts is reduced, so that these thin walled plastic parts cannot be molded by conventional injection molding methods. When forming thin walled plastic parts, following common problems exist:
, has paved the way in producing premium quality, high-performance medical device injection molding products. Their focus extends from simple disposable medical devices to more complex implantable medical devices, with a special emphasis on surgical instruments and diagnostic equipment.
Two crucial developments further highlight the profound influence of micro-molding in the field. One is the refinement of two-shot injection molding that allows for simultaneous injection of two different plastics into a single mold. This technique has significantly boosted the manufacturing efficiency of complex medical device components. The other is the potential of micro-molding to pave the way for polymer-drug conjugates, a novel innovation that could revolutionize the medical injection molding process.
like Marlee – Texen at the forefront, the future of medical injection molding promises to deliver even greater innovation and quality analysis, optimizing flow and reducing waste. These advancements ensure that patients around the world benefit from safer, more effective medical devices, a testament to the relentless pursuit of excellence in the medical molding sector.
Welding line is boundary formed when two or more melt flow fronts within a cavity are fused. Stress concentration is easy to occur at welding line, which weakens mechanical strength of plastic part, which is particularly detrimental to mechanical properties of plastic part, especially thin-walled plastic part. Plastic part is very easy to crack at welding line after external force.
are the backbone of the healthcare industry, and their production hinges on the precision and reliability of injection molding.
According to surveys, domestic thin-wall injection molding has been widely used in food containers, medical boxes, cosmetics, stationery and even multimedia packaging. For example: disposable packing boxes, cosmetics bottles and other daily necessities.
Transparent finished PC material is easy to appear. Because gas is not exhausted during injection process, improper mold design or improper molding conditions can have an impact.
Additional CNC machining is provided after thermoplastic injection molding. We can also put metal inserts into medical plastic parts by heat pressing.
In conclusion, these technological advancements in medical device injection molding have redefined the boundaries of what’s possible in the medical industry. From the smallest micro components to the most complex medical parts, these innovations have facilitated the creation of high-quality, disposable, and durable medical devices, elevating the overall standard of healthcare.
In the demanding field of Medical Device Design, the choice of High-Quality Materials for Medical Injection Molding is critical. An essential consideration in this sector is the range of materials available, from Polypropylene to PEEK. At Marlee – Texen, we excel in providing a comprehensive array of materials to ensure your project’s success.
Our Medical Injection Molding services are meticulously carried out in the confines of our advanced Cleanroom Manufacturing facilities. These environments ensure the sterility and safety of every device and medical device part we manufacture. As an industry-leading provider of plastic injection molding, our cleanroom facilities are designed to eliminate contaminants, ensuring the utmost safety for the end-user.
Polycarbonate (PC) is quite an efficient material that is amorphous and transparent in nature. It is a type of thermoplastic used in medical plastic packaging, a wide variety of shapes and sizes of plastic. PC injection molding is one of the best choices for manufacturing custom-tailored plastic because of its highly flexible and impact-resistant qualities.
At present, commonly used thin-wall injection molding materials are: polycarbonate (PC), acrylic-butadiene-styrene (ABS), PC / ABS blends, and PA6. As wall thickness decreases, plastics with better physical properties are needed to maintain product strength.
Every step, from mold design to post-molding operations, including state-of-the-art plastic welding techniques, is conducted under rigorous regulation and compliance with ISO 13485 and FDA standards. With an emphasis on medical device design and medical injection molding process, Marlee – Texen offers tailor-made medical plastic products for a diverse range of applications.
The transformative impact of medical injection molding on the healthcare industry is a testament to its versatile applications. With its precision and efficiency, it caters to a multitude of sectors within the industry, enabling manufacturers like Marlee – Texen to produce top-tier medical devices. One of the significant contributions of this process is in the production of
Our precision in molding extends beyond materials like polypropylene and PEEK. We are also a leading producer of micro-molding components, crucial in the development of advanced medical technologies. Our precision welding processes ensure seamless joins between components, maintaining the integrity of the overall device.
As a reliable supplier in the industry, we abide by the 13485 quality management system. Our thorough risk assessment procedures ensure the highest level of safety and reliability in our products.
Automation, combined with cutting-edge technologies like rapid prototyping, has enabled precise molding for both plastic and silicone based products. Furthermore, automation ensures enhanced cleanroom standards, paramount for medical parts production, ensuring compliance with ISO and FDA regulations.
in the industry, primarily due to our unwavering commitment to the highest quality standards and adherence to stringent regulations.
When flow length is 300mm and wall thickness of plastic part is 3.0 mm, L / T is 100 at this time, which is easily achieved by conventional injection molding technology; but when wall thickness of plastic part drops below 1.0mm, this once-to-be-achieved flow-length-thickness ratio (100) becomes very difficult to achieve.
For PC materials, sometimes mold temperature is too high, mold surface has residual glue and oil stains. It is necessary to clean mold surface in time, lighten processing, and reduce mold temperature.
Utilizing robust silicone and plastic materials, our advanced processes assure the traceability of every implant, mold, and micro-molded part. Our stringent quality control measures ensure that every weld and polymer application aligns with the highest industry standards. Our in-depth assessment procedures are followed by rigorous testing, guaranteeing the quality and safety of our output.
Reduce thickness, but keeping at least 2/3 of thickness, can be improved by thickening runner, increasing gate, increasing exhaust, increasing material temperature, increasing injection pressure, and extending holding time.
It often occurs at the junction of male and female molds, due to poor mold clamping, or improper processing of corners of mold surface. Molding temperature is often insufficient due to insufficient clamping force, high material temperature, and high pressure.
It often occurs in uneven wall thickness or flesh thickness of molded product, which is caused by difference in cooling or curing shrinkage of hot-melt plastic. Such as back of ribs, edges with side walls, back of BOSS column.
Slender pieces, large-area thin-walled pieces, or large finished products with asymmetric structures are caused by uneven cooling stress or uneven ejection forces during molding.
Biocompatible plastics, also known as Bio-Compatible Plastics, are essential for ensuring the safety and functionality of a medical device. They are engineered to interact with the human body without causing any adverse reaction. This feature is paramount in the industry, where patient safety and assurance of product functionality are non-negotiable.
companies is the use of automation. Leveraging advanced injection molding equipment and scientific molding principles, they ensure consistent production of high-precision medical device injection molding parts, regardless of whether it’s high-volume production or low-volume production.
Generally, changing holding time and injection pressure (second stage) has the greatest effect on size. For example, increasing injection pressure, pressure-retaining and shrinking effect can significantly increase size and lower mold temperature. Increasing inlet can improve adjustment effect.
At Marlee – Texen, we adhere strictly to both ISO and FDA standards. Every regulation is taken into account, and compliance is guaranteed. Our processes are regularly audited, our tools and assembly procedures are meticulously maintained, and every component we produce is verified for accuracy using advanced equipment and machines.
As a leading player in the industry, Marlee – Texen continues to embrace these technological advancements, contributing to molding industry trends and setting the bar high in terms of quality and efficiency.
Mold correction, mold re-clamping, increase clamping force, lower material temperature, reduce injection pressure, reduce holding time, reduce holding pressure.
. This critical facet of medical device production ensures the sterile and safe transport of these crucial devices, reinforcing their commitment to overall healthcare delivery.
Medical device injection molding process is used in bone repair and rearrangement. It is also used for soft tissue reattachment.
Occurs at confluence of two streams, such as confluence of two inlets, confluence of bypass bypassing core, is due to decline in material temperature and poor exhaust.
. These tailor-made solutions not only maintain the sterility of medical products but also offer efficient storage and delivery of devices.
At Marlee – Texen, we excel in high-volume production while maintaining meticulous quality control. We deploy advanced flow analysis to optimize the production process, and our commitment to creating safe, effective disposable medical products is unwavering.
Marlee – Texen is committed to providing superior solutions that cater to the demanding needs of the medical device industry. We guarantee high-quality materials, stringent testing, and dedicated service to ensure we meet and exceed your expectations.
Increase exhaust, change gate (inlet gate increases), PC flow path must be polished, strict drying conditions, increase injection pressure, reduce injection speed, etc.
It can be seen that critical value defined by thin-wall injection molding will also change, and it should be a relative concept.
Thin-wall injection molding technology is also known as thin-wall plastic injection molding technology. There are three types of definitions:
Increase draft angle, polish mold surface, increase or change pull pin when sticking female mold surface. Pay attention to horn diameter when feeding horns, add bite to male mold, reduce injection pressure, reduce holding pressure and time.
It can be processed by modifying core, ejector pin, and sandblasting of mother mold surface. It can reduce brightness of mold surface, reduce injection speed, and reduce injection pressure.
to meet your needs. Our emphasis on quality assurance and medical component assembly sets us apart in the medical molding industry, making us a trusted partner for healthcare providers across the globe.
The customization process involves a collaborative approach of Design for Manufacturing (DFM). This approach ensures every part of the device – be it orthopedic, cardiovascular, or any other field – is meticulously designed and manufactured. This process not only maximizes quality and efficiency but also significantly reduces risk and time-to-market.
We provide services like pad printing and silk screening to put 2-D designs on 3-D surfaces. These designs can be customized for labeling, branding, etc. We use standard colors and Pantone matching.
At Marlee – Texen, we are stringent about Biocompatibility Testing. Our medical-grade materials undergo rigorous testing to meet the required standards. We are adamant about quality, from the selection of polymer materials to their transformation into a functional part of a medical device.
Ratio of flow length to thickness L / T, that is, ratio between flow length L from melt entering mold to the furthest point of cavity where melt must be filled and corresponding average wall thickness T is 100 or 150, which is being called thin-wall injection molding;
Warpage deformation is a plastic defect caused by uneven internal stress. Cause of warpage deformation is uneven shrinkage, uneven orientation, and uneven cooling.
Increase R angle at the corner, increase demolding angle, increase ejector pin or increase its cross-sectional area, polish mold surface, polish ejector pin or oblique pin, reduce shooting rate, reduce injection pressure, reduce holding pressure and time.
In the intricate world of Medical Device Design, the selection of High-Quality Materials for Medical Injection Molding plays a pivotal role. A critical aspect of this process lies in the Importance of Biocompatible Plastics in Medical Devices, and this is where we position our expertise.
Safety is paramount in our operations. Our Cleanroom Molding and Sterilization Techniques are implemented with a deep understanding of the importance of safety in medical device manufacturing. We also offer rapid turnarounds, without ever compromising quality or safety.
When thickness of plastic part is reduced, influence of condensate layer on flow will increase exponentially, which also explains influence of condensate layer in thin-wall injection molding. If only considering injection molding, it is necessary for injection molding machine to have a high injection rate, so that rate at which plastic melt fills cavity exceeds growth rate of condensation layer (or growth rate of condensation layer is slowed), so that filling action can be completed before flow section is closed, thin-walled plastic parts are injection molded.
Our range of biodegradable plastics and polymer materials are expertly chosen to ensure the highest grade of biocompatibility. Our offerings include:
Alloys like PC/ABS and TPE/TPU – PC/ABS combines the strength of PC and the flexibility of ABS, making it ideal for use by a medical plastic products manufacturer. TPE and TPU are thermoplastic elastomers. They are used for making lids, sports goods, power tools, medical device parts, etc. They are used in these industries for their abrasion resistance and elasticity.
To conclude, automation and technological advancements in medical molding have made a significant impact on the medical device market. These advancements are not just about high-speed delivery and high-volume molding but also about maintaining safety and quality, ensuring each product meets the strictest medical grade standards.
Our team of expert manufacturers at our company is well-versed in the requirements of the industry, ensuring traceability of all parts and components, including sensitive implants. Our validation processes and quality checks make us an ideal choice for micro molding requirements in the medical industry.
Polypropylene(PP) is a thermoplastic resin used for its flexibility and strength. It has a very low density and is suitable for scientific molding. Its flexibility and resistance find much application in plastic medical packaging sensitive material. PP is an “addition” polymer, made from the linking of many polypropylene monomers.
The process of injection molding is complex and requires precision at every stage. Every part we create for your medical device is injection molded to exact specifications, guaranteeing performance and safety. Our thorough selection process, extensive product development capabilities, and advanced process management set us apart in the industry.
in creating effective medical packaging. Their offerings ensure safety, sterility, and efficient delivery of medical devices, embodying their commitment to overall patient health and safety.
Another significant development is the adoption of liquid silicone rubber (LSR) in the medical injection molding process. LSR is ideal for producing implantable and disposable medical devices due to its superior biocompatibility.
that comprehensively aligns with FDA Regulations and maintains an unwavering commitment to Medical Standards Compliance. We are proud holders of ISO 13485 certification, which underscores our commitment to quality and safety in the production of medical devices. Our Validation Process is thorough and rigorous, ensuring every part and component we produce is safe, effective, and reliable.
Occurs at joints of male and female modules, sliders, oblique pins, etc., which appear as uneven levels of joint surface, etc., due to improper mold clamping or problems with mold itself.
Filling and cooling processes of conventional injection molding are intertwined. When polymer melt flows, front of melt encounters a core surface or cavity wall with a relatively low temperature, and a condensation layer is formed on the surface. Melt continues to flow forward in condensate layer. As thickness of condensate layer increases, actual cavity flow channel becomes narrower. Thickness of condensate layer has a significant effect on polymer flow. Because thickness of plastic part is thicker in conventional injection molding, influence of condensation layer on injection molding is not great at this time. However, in thin-wall injection molding, when ratio of thickness of condensing layer to thickness of plastic part gradually increases as thickness of plastic part becomes thinner, this effect is great. Especially when sizes of the two can be compared with each other.
Every material used and every product produced at Marlee – Texen undergoes rigorous quality checks and verifications. Our comprehensive processes are aligned with top design and tool selection strategies to enable the effective assembly of components. Our equipment and machines are optimized for precision, allowing us to cater to diverse requirements, including surgical applications.
Our approach to Quality Control is exhaustive. From the initial design and injection phase of Medical Injection Molding to the final assembly and packaging of your device, our team ensures every step of the process is controlled, monitored, and optimized. We understand that the end-use of our products is in the critical healthcare sector, making the safety and functionality of each part and medical device we produce a non-negotiable priority.
Polyethylene or polythene is the resin made from the polymerization of ethene. PE is the most versatile synthetic resin. It has a crystalline structure and can be high density (HDPE) or low density (LDPE). It is used by the medical plastic products.
Appears as poor demolding, mold damage, or pull. Mainly because draft angle is not enough or mold surface is rough, molding conditions also have an influence.
, Stringent Quality Control and Regulatory Compliance serve as the bedrock of our operations at Marlee – Texen. We are recognized as one of the leading
It occurs at the gate, because mold temperature is not high, injection speed and pressure are too high, gate is not set properly, and plastic encounters spoiler structure during feeding.
Medical device injection molding, however, is not merely about the molding process but also involves detailed tooling design, stringent compliance, and rigorous regulation. In fact, Marlee – Texen has built its reputation as one of the
Whether you require drug delivery devices, enclosures, packaging, or disposable medical components, Marlee – Texen stands as the
Injection molding method where thickness of molded plastic part is less than 1 mm, and projected area of plastic part is above 50 c㎡;
Warping deformation defects of plastic parts can be improved by balancing cooling system, adjusting cooling time, holding pressure and holding time.
GETTING A QUOTE WITH LK-MOULD IS FREE AND SIMPLE.
FIND MORE OF OUR SERVICES:
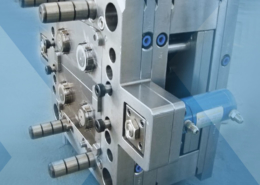
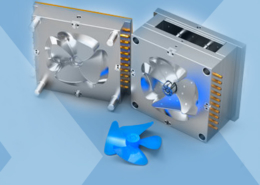
Plastic Molding

Rapid Prototyping
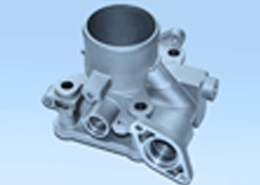
Pressure Die Casting
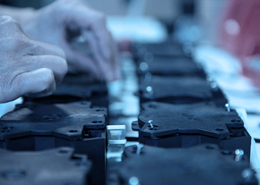
Parts Assembly
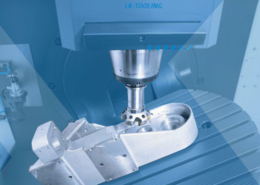