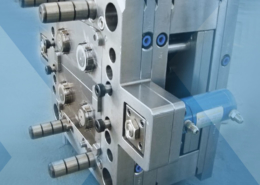
Plastic Injection Moulding | Plastic Manufacturing Product ... - plast mould par
Author:gly Date: 2024-10-15
Low-volume prototype tools are created through 3D printing, machining, and cast urethane. With these prototype tools, machinists can troubleshoot the tooling design, reducing the chance for error in the manufacturing and assembly process – and saving time and expense — later.
After the heated material fills the pre-formed mold, it begins to harden as it cools. Then, the hardened plastic and the tool can separate, leaving a new part and a tool that is ready for re-filling.
In the healthcare sector, where timely intervention can be a matter of life or death, the speed of production in medical device manufacturing takes on heightened importance. Injection moulding is particularly advantageous in this regard. The process boasts rapid cycle times, often as quick as a few seconds, which facilitates accelerated production schedules. This expediency isn’t just about speed for its own sake; it’s about how quickly medical devices can transition from manufacturing to market. Quicker market entry means the ability to meet immediate medical needs more effectively, thereby solidifying the advantages of injection moulding in producing essential healthcare equipment.
Whether the job calls for an intricate or simple part, tooling determines the quality of the plastic injection molding process and the components created.
This first tool is put through its paces to test its functions properly and produce the specified part. During this stage, modifications and mold texturing can occur. Once this stage is complete, the samples are sent to the contract manufacturer.
Sensors placed on the surface of the tool can monitor the cooling rate and the cavity pressure profile. Tooling engineers also pay close attention to the following factors:
Just as a baker pours their batter into the right baking pan, a skilled machinist pours liquidized plastic into a mold that is in the shape of a part. This mold, typically known as tooling, is the key to the creation of a high-quality precision component.
Plastic molding tooling can produce molded parts that meet the unique requirements of each project. Tooling design begins with the prototype phase.
Meridian Medical is an established and experienced contract medical device manufacturer specialising in a wide range of medical devices. We offer design, regulatory assistance, cleanroom injection moulding, cleanroom assembly, contact packaging and sterilisation Management. We have over 30 years’ experience supplying UK and European companies.
Scalability is often a make-or-break factor for success. One of the advantages of injection moulding that truly sets it apart is its capacity for effortless scalability. Whether the requirement is for a limited series of prototypes or a full-scale production run, the process is designed to adapt seamlessly. Modular mould designs allow for straightforward adjustments, enabling manufacturers to easily switch from low to high-volume production without extensive retooling. Moreover, automated systems and process optimisation techniques further streamline scalability, allowing for rapid adjustments to meet fluctuating market demands or regulatory requirements. This flexibility in production volumes not only saves time but also optimises operational costs, exemplifying why injection moulding is so effective and versatile in addressing the varied needs of the medical device sector.
The ultimate goal of this complex interaction is to create a high-quality precision part that is on time and on budget. If you have questions about plastic injection tooling and how it can work for your company, please contact us today.
For example, tool design engineers use flow analyses to optimize the mold, including finding the best locations for parting lines, gates, and ejection locations. Design engineers then collaborate with toolmakers in creating a tool sample.
Anaesthesia is a cornerstone of modern surgery, allowing patients to undergo procedures minimising pain or discomfort. Single-use anaesthetic medical devices, including those used for Total...
Since they are the foundation of the plastic molding process, tool design requires time, effort. And expertise. The suitable mold material is the first consideration. Most plastic injection molds are made of steel, aluminum, or alloys.
Injection moulding is uniquely positioned to meet the stringent demands for precision and consistency within the medical device industry. The process involves injecting molten material – often specialised medical-grade polymers – into a custom-designed mould under high pressure. This technique ensures that every component is shaped exactly as intended, down to the micron level. In a sector where minuscule deviations can have significant implications for patient care and treatment outcomes, the exacting nature of injection moulding proves invaluable. For manufacturers, this translates into fewer defects and reduced costs associated with quality control, further emphasising the advantages of injection moulding.
Sophisticated components demand sophisticated tooling. The tooling process requires accurate monitoring for consistent, reliable part production.
The unique and highly specific demands of healthcare applications require a manufacturing process that allows for a high degree of customisation and flexibility. In this context, injection moulding excels. Not only does it allow for the production of complex geometries and internal structures, but the moulds themselves can be customised to incorporate features like engravings or identifiers, essential for traceability in medical devices. Manufacturers also have the flexibility to adjust various parameters, from material composition to temperature controls, allowing the tailoring of products to meet stringent sterility and biocompatibility requirements. Furthermore, advancements in technology enable the use of multi-cavity moulds, facilitating the simultaneous production of multiple components with varying designs. These capabilities underscore the advantages of injection moulding and its suitability for producing highly specialised medical equipment.
2022 © Meridian Medical · Unit 1, Thorgate Road, Lineside Industrial Estate, Littlehampton, West Sussex, BN17 7LU · +44 (0) 1903 732 344 Registered office: Unit 1, Thorgate Road, Lineside Industrial Estate, Littlehampton, West Sussex, BN17 7LU · Co. Reg. No. 2609505 Site by LWS : Marketing, website design and graphic design in Arundel, West Sussex
In the highly regulated world of medical device manufacturing, ensuring that each aspect of your production consistently meets specification is critical. A robust Medical Device Validation Plan...
In the world of orthopaedic medical device manufacturing, precision and reliability are essential. At Meridian Medical, we are committed to our role as a leading subcontract manufacturer of...
Get in touch with the experts at Meridian Medical to discuss your requirements for medical device manufacturing, injection moulding, cleanroom assembly and full device project management.
From intricate designs to customisable solutions, the advantages of injection moulding in medical device manufacturing are hard to ignore. As medical technology continues to evolve, this method will undoubtedly play a central role in producing innovative devices that improve patient outcomes and contribute to advancements in healthcare globally.
I acknowledge that you will process my personal details in accordance with your privacy policy in order to respond to my enquiry.
The next step is to place the new design on the production line. Here the tool is carefully observed and validated. After it passes this scrutiny, the mold enters a regular production schedule, where it is routinely monitored for wear and tear and any other issues that could affect part quality.
The process from prototype to production line can take months to complete, but each step creates more value in the long run. In fact, once the design and testing process is complete, the actual manufacturing process is automated and efficient.
To find out more about how Meridian Medical can help you with your medical device manufacture, get in touch today by filling out our online form or contacting us on 01903 732344 or info@meridian-medical.com.
In medical device manufacturing, cost-effectiveness is not merely an advantage, it’s a necessity. Injection moulding stands out by offering a myriad of financial benefits over traditional manufacturing methods such as machining or casting. This process allows for the creation of multiple components in a single cycle, substantially increasing throughput. Moreover, the high efficiency of injection moulding minimises waste material, further contributing to cost savings. Another significant benefit is the reduced need for post-processing, often eliminating the need for additional finishing, thus saving time and labour costs. All these factors combine to create a cost-effective production ecosystem that benefits not just manufacturers but ultimately contributes to more affordable healthcare solutions for end-users.
Think about it. Plastic injection molding involves the science of shooting hot, molten resin into the cavity of a mold. However, the design process is undertaken through a process of intuition, technique, and plain old trial and error.
Our Policies Privacy PolicyTerms and ConditionsCookie PolicyEthical Trading PolicyAnti-Bribery PolicyEnvironmental and Sustainability Policy
As you can see, there is more that goes into the manufacture of precision molded parts than meets the eye. Plastic injection tooling is both a scientific and a creative process.
Since steel can tolerate high temperatures and pressure, steel tooling can produce millions of plastic parts. On the other hand, aluminum tooling is less expensive to create but can only produce in the thousands of plastic parts.
Injection moulding’s unique attributes make it a preferred choice for a wide array of applications. From disposable items like syringes and catheters to more complex, life-saving devices like heart valves and surgical robots, the technique is invaluable. The advantages of injection moulding come to the fore when one considers the stringent sterility requirements and material compatibility needed in these devices. Advanced moulding techniques even allow for the incorporation of antimicrobial agents directly into the mould, offering an additional layer of patient safety.
Sign up for our quarterly e-newsletter to stay up-to-date with Meridian Medical news, industry insights and information on medical device manufacturing.
In the fast-paced world of medical device manufacturing, efficiency, precision and cost-effectiveness are paramount. Among the manufacturing techniques that rise to meet these challenges, injection moulding stands out. This versatile and highly efficient process has not only become a cornerstone in the production of medical devices but also offers a host of other benefits. This blog aims to explore the advantages of injection moulding, and how this technique has revolutionised the medical device industry
This website uses functional cookies which make it work and we also use marketing cookies to help us better understand website usage and make our service better. You can reject the marketing cookies if you wish. (Read More)
At ASPM, we showcase our established history of quality tooling and molding by implementing our rigorous approach to plastic product development. We offer complete support from product design and feasibility, through routine injection mold maintenance and repair. Our highly trained staff is prepared to handle plastic projects with varying complexity in our robust 24-hour facility. Contact us today to discuss your next project.
Tooling for a plastic injection mold project also includes acquiring all the components and machinery needed for the job, including gauges, jigs, fixtures, and other equipment. The effort and efficiency of this process have much to do with the quality and the cost of the end part.
In the domain of medical device manufacturing, the selection of materials holds particular significance due to direct or indirect contact with the human body. Injection moulding rises to the challenge by offering compatibility with a myriad of medical-grade materials. These range from biocompatible polymers and thermoplastics to silicone and high-performance resins. Such material diversity provides the flexibility to meet not only sterility and biocompatibility requirements but also offers scope for customising mechanical properties like strength and flexibility. This adaptability underlines yet another advantage of injection moulding, making it an ideal choice for a plethora of healthcare applications
Stringent quality control isn’t just a regulatory requirement; it’s a moral obligation. One of the most compelling advantages of injection moulding lies in its inherent capability to offer granular control over each step of the production process. From the input material quality to the precision of the mould and the calibration of injection parameters, every element can be rigorously monitored. Furthermore, state-of-the-art injection moulding machines are equipped with advanced sensor technology and real-time feedback systems. These systems not only facilitate immediate adjustments to ensure optimal performance but also allow for statistical quality control, thereby significantly reducing the risk of defects and waste. Such meticulous quality assurance mechanisms make injection moulding an ideal choice for the exacting standards required in medical device production.
GETTING A QUOTE WITH LK-MOULD IS FREE AND SIMPLE.
FIND MORE OF OUR SERVICES:
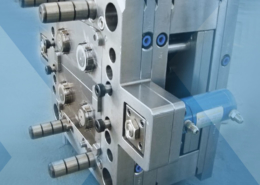
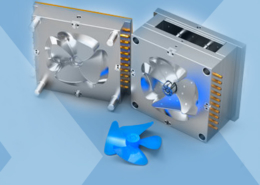
Plastic Molding

Rapid Prototyping
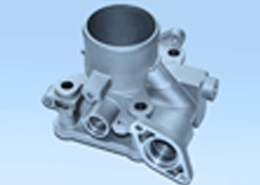
Pressure Die Casting
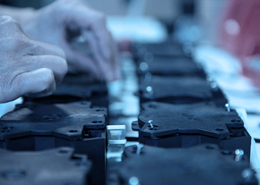
Parts Assembly
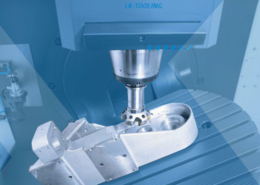