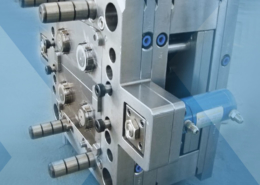
Understanding PETG Injection Molding: A Comprehensive Overview
Author:gly Date: 2024-06-08
PETG (Polyethylene Terephthalate Glycol) injection molding is a pivotal process in modern manufacturing, offering a versatile solution for producing a wide array of products. This article aims to delve into the intricacies of PETG injection molding, providing readers with a comprehensive understanding of its principles, applications, advantages, challenges, and future prospects.
Introduction
PETG injection molding stands as a cornerstone in the realm of plastic manufacturing, captivating industries with its exceptional properties and adaptability. Originating from the polyester family, PETG exhibits remarkable clarity, durability, and chemical resistance, rendering it an ideal candidate for various applications.
Material Properties
Versatility and Adaptability
PETG's versatility enables it to accommodate diverse molding requirements, ranging from intricate designs to large-scale production. Its ability to maintain structural integrity under different temperatures and pressures makes it suitable for a broad spectrum of applications, including packaging, automotive parts, medical devices, and consumer goods.
Transparency and Aesthetics
One of PETG's distinguishing features is its exceptional transparency, rivaling that of glass. This property, coupled with its inherent clarity and gloss, makes PETG an attractive choice for products where aesthetics play a crucial role. From cosmetic packaging to display cases, PETG's ability to showcase contents with pristine clarity adds value to various consumer products.
Mechanical Strength and Durability
PETG boasts impressive mechanical properties, combining high tensile strength with impact resistance. This unique blend of strength and flexibility ensures that PETG components withstand rigorous handling and environmental stresses without compromising performance. Consequently, PETG finds widespread use in applications requiring durable and long-lasting solutions.
Injection Molding Process
Mold Design and Optimization
The success of PETG injection molding hinges on meticulous mold design and optimization. Factors such as gate placement, cooling channel configuration, and part geometry profoundly influence the quality and efficiency of the molding process. Employing advanced simulation techniques aids in predicting and mitigating potential defects, thereby streamlining production and enhancing product consistency.
Injection Molding Parameters
Fine-tuning injection molding parameters is paramount in achieving optimal results with PETG. Variables such as melt temperature, injection speed, and packing pressure significantly impact part quality and dimensional accuracy. By meticulously controlling these parameters, manufacturers can ensure uniformity across production batches while minimizing scrap and rework.
Post-Molding Operations
While injection molding yields near-net-shaped parts, post-molding operations may be necessary to refine surface finish or add secondary features. Techniques such as machining, polishing, and assembly complement the injection molding process, enabling manufacturers to meet stringent design specifications and functional requirements.
Advantages and Challenges
Advantages of PETG Injection Molding
Cost-Effectiveness
: PETG's recyclability and ease of processing contribute to cost-effective production solutions.
Design Freedom
: Injection molding allows for intricate part geometries and customization, empowering designers to unleash their creativity.
Environmental Sustainability
: PETG's recyclability aligns with growing sustainability concerns, offering eco-friendly alternatives to traditional plastics.
Challenges and Mitigation Strategies
Warpage and Shrinkage
: PETG's inherent shrinkage tendencies can lead to dimensional inaccuracies and warpage. Employing proper mold design and processing techniques helps mitigate these challenges.
Mold Contamination
: PETG's susceptibility to contamination necessitates stringent cleanliness protocols during mold preparation and maintenance.
Material Compatibility
: Compatibility issues with certain additives or colorants may arise, necessitating thorough compatibility testing to ensure product integrity.
Future Outlook and Recommendations
In conclusion, PETG injection molding epitomizes the convergence of innovation and functionality, revolutionizing the manufacturing landscape. As industries continue to embrace sustainable practices and demand custom-tailored solutions, PETG's versatility and performance make it poised for sustained growth and adoption.
To further enhance the efficacy and sustainability of PETG injection molding, future research avenues may include:
Advanced Material Development
: Exploring novel formulations and additives to enhance PETG's properties and expand its application range.
Process Optimization
: Continuously refining injection molding processes through advanced modeling and simulation techniques to improve efficiency and reduce waste.
Circular Economy Initiatives
: Embracing circular economy principles by enhancing recycling infrastructure and promoting closed-loop material cycles to minimize environmental impact.
By embracing these endeavors, stakeholders can propel PETG injection molding towards greater innovation, sustainability, and global relevance in the years to come.
In essence, PETG injection molding transcends mere manufacturing processes, embodying a testament to human ingenuity and technological prowess. As we navigate the complexities of the modern world, PETG stands as a beacon of possibility, reshaping industries and driving progress towards a more sustainable future.
GETTING A QUOTE WITH LK-MOULD IS FREE AND SIMPLE.
FIND MORE OF OUR SERVICES:
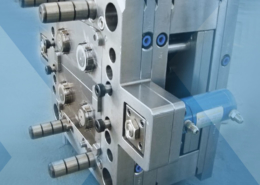
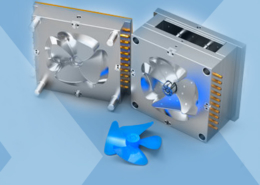
Plastic Molding

Rapid Prototyping
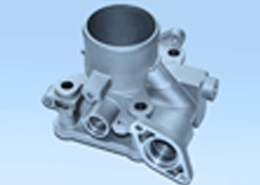
Pressure Die Casting
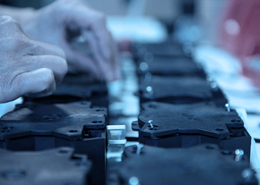
Parts Assembly
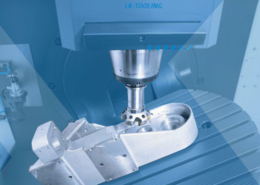