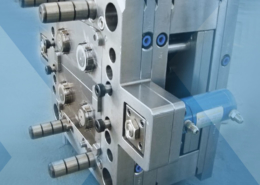
Exploring the World of PEEK Molding: Precision, Performance, and Possibilities
Author:gly Date: 2024-06-08
In the realm of advanced engineering plastics, Polyether Ether Ketone (PEEK) stands out as a versatile and high-performance material with a wide range of applications. PEEK molding, utilizing injection molding techniques, unlocks the full potential of this exceptional material, enabling the production of complex components with precision, reliability, and durability. This article delves into the fascinating world of PEEK molding, exploring its applications, advantages, challenges, and future prospects.
Introduction: Unveiling the Potential of PEEK Molding
PEEK, known for its exceptional mechanical properties, chemical resistance, and thermal stability, has gained prominence in various industries, including aerospace, automotive, medical, and electronics. PEEK molding harnesses the unique characteristics of this polymer to produce components that meet the most demanding performance requirements. From intricate medical implants to high-temperature aerospace components, PEEK molding offers limitless possibilities for engineers, designers, and manufacturers.
Material Properties: Unraveling the Strengths of PEEK
PEEK's exceptional properties make it an ideal candidate for molding applications where high strength, stiffness, and dimensional stability are paramount. With a tensile strength comparable to aluminum and a modulus of elasticity similar to steel, PEEK exhibits excellent mechanical performance under extreme conditions. Moreover, PEEK is inherently resistant to chemicals, hydrolysis, and high temperatures, making it suitable for applications where exposure to harsh environments is a concern. These unique material properties make PEEK molding an attractive choice for industries requiring high-performance components with exceptional reliability and durability.
Precision Engineering: Achieving Complex Designs with Accuracy
Injection molding allows for the production of complex geometries and intricate features with unparalleled precision and repeatability. PEEK molding takes advantage of this capability to produce components with tight tolerances, intricate details, and fine surface finishes. Whether it's medical implants with intricate geometries, aerospace components with precise dimensions, or electronic housings with intricate features, PEEK molding offers the accuracy and consistency required for demanding applications. By leveraging advanced tooling and molding techniques, manufacturers can achieve the desired design specifications with minimal post-processing, reducing time-to-market and overall production costs.
Biocompatibility: Enabling Medical Innovations and Implants
In the medical field, biocompatibility is a critical consideration for materials used in implants and medical devices. PEEK's biocompatibility, combined with its mechanical properties and radiolucency, makes it an attractive choice for medical applications, including orthopedic implants, spinal implants, and surgical instruments. PEEK molding enables the production of patient-specific implants with precise geometries and tailored mechanical properties, facilitating faster recovery times, improved patient outcomes, and enhanced quality of life. As medical technology continues to advance, PEEK molding will play an increasingly important role in driving innovation and revolutionizing healthcare.
Challenges and Future Directions: Overcoming Hurdles and Embracing Innovation
While PEEK molding offers numerous advantages, it also presents challenges, such as high processing temperatures, material costs, and tooling complexity. Addressing these challenges requires ongoing research, development, and collaboration between material suppliers, molders, and end-users. Future directions for PEEK molding include the development of advanced processing techniques, novel material formulations, and additive manufacturing methods to further enhance performance, efficiency, and cost-effectiveness. By embracing innovation and collaboration, the potential of PEEK molding can be fully realized, opening new frontiers in engineering, manufacturing, and product development.
Conclusion: Embracing Excellence in PEEK Molding
In conclusion, PEEK molding represents a pinnacle of excellence in plastic engineering, offering unmatched performance, precision, and versatility for a wide range of applications. With its exceptional material properties, precision engineering capabilities, and potential for innovation, PEEK molding continues to push the boundaries of what is possible in modern manufacturing. As industries continue to evolve and demand for high-performance components grows, PEEK molding will remain at the forefront of innovation, driving progress and shaping the future of engineering and technology.
GETTING A QUOTE WITH LK-MOULD IS FREE AND SIMPLE.
FIND MORE OF OUR SERVICES:
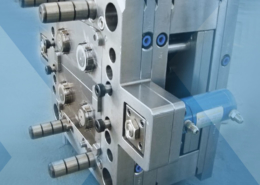
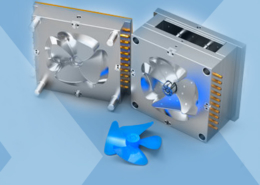
Plastic Molding

Rapid Prototyping
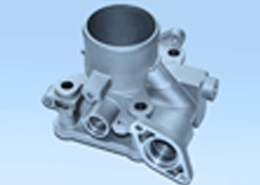
Pressure Die Casting
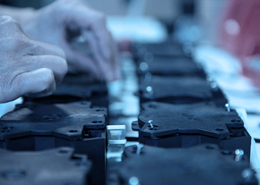
Parts Assembly
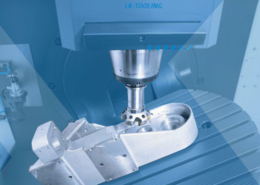