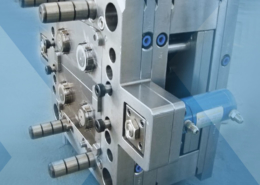
Plastic Injection Molding Services - large plastic injection molding companies
Author:gly Date: 2024-10-15
We work with a leading range of polymer and elastomer suppliers, as well as additive suppliers and chemists to tap into a large knowledge pool to help recommend the best material for your application.
P20 steel is a combination of carbon, chromium, manganese and molybdenum and has great machining and superior polishing properties. Because it is pre-hardened, it doesn’t have to be heated which reduces production lead times. P20 is extremely versatile and is often the first-choice steel for use in plastic injection moulding by product designers and engineers. It is particularly useful for prototypes.
OGM medical mould tools often conform to SPI class 101, with European grade materials and components, including key elements such as the hot runner system for example. We do this to ensure tool longevity and reliability.
At OGM, we have a team of in-house technical experts who can help you with your injection moulding project. Our technical team, with over 40 years combined experience and knowledge, use the latest 3D CAD and Moldflow® simulation software to fine tune your part design for the best outcome.
Production toolingFor production, fully hardened steel tooling is the industry standard for the injection moulding process, and normally comes with a 1 million shot warranty. Hardened steel tools are used for high volume production when hundreds to thousands or millions of plastic injection moulded parts are required.
Injection mould tools can be manufactured in several different materials, the most common are P20, H13 steels and aluminium.
Owen Greenings & Mumford Ltd is the trading name of OGM Ltd, a company registered in England and Wales with company number 00742307
There are several benefits of choosing P20 steel over aluminium when it comes to creating development tools. One of the main reasons is that P20 steel is readily available and an easy to work with material. It can be machined, sparked, wired, welded, and textured. Secondly, P20 is less costly than aluminium and thirdly, and perhaps most importantly P20 is generally more resistant to scratching and similar cosmetic damage than aluminium.
H13 consists of Carbon, Chromium, Manganese, Molybdenum, Nickel and Silicon. It is a robust, strong steel with exceptional resistance to heat, wear and tear, cracking and tempering. H13 is suited to very high-volume production runs and can handle the manufacture of plastic parts that contain abrasives as well as production cycles that have continuous cooling and heating.
Why is material choice so important?Your choice of raw material for your injection mould tools is critical. The properties of the materials impact the quality of your final components, determine product reliability and tool lifetime, and overall part cost.
When designing medical injection mould tools, OGM often use stainless steel throughout the tool construction, all the way from the bolster (the outer frame) through to the core and cavity inserts (the parts in contact with the plastic) which could be made in high performance grades such as BÖHLER M333 and Uddeholm Stavax. OGM can supply cores and cavities with latest Conformal Cooling technology, for optimum cycle time performance, using metal additive manufacturing.
Development toolingBefore embarking on a fully hardened multi-cavity production tool, OGM often recommend designing and manufacturing a single or two cavity “development tool”. Following detailed discussions with the customer, the development tool is often designed to be manufactured in a “metal safe” condition. The aim is to produce a tool that can be tweaked numerous times to fine tune the part geometry until it is correct, and the customer is happy. We then transfer the “lessons learnt” to a larger multi-cavity tool, pursuing a “right first time” approach.
GETTING A QUOTE WITH LK-MOULD IS FREE AND SIMPLE.
FIND MORE OF OUR SERVICES:
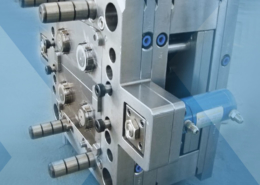
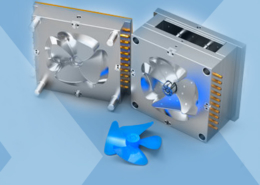
Plastic Molding

Rapid Prototyping
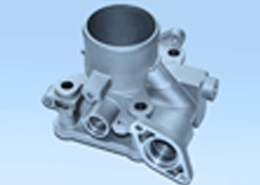
Pressure Die Casting
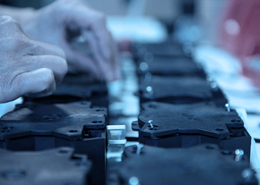
Parts Assembly
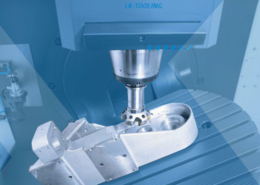