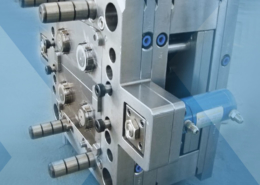
Plastic Injection Molding Service Provider - plastic molding services
Author:gly Date: 2024-10-15
With almost 50 years of injection molding experience, our experts can find the perfect solution for your project. We look forward to the challenge of designing and producing your custom polyurethane foam product.
UV Resistant PC: By adding UV stabilizers, the weather resistance of PC for outdoor use is enhanced, reducing discoloration and performance degradation due to prolonged UV exposure.
PC/PBT or PC/PET Alloy: By blending with PBT (Polybutylene Terephthalate) or PET (Polyethylene Terephthalate), chemical resistance and impact resistance are enhanced, often used for products requiring chemical corrosion resistance and high impact strength.
Let’s quickly understand the various types of Polycarbonate (PC) and the nature of modified PC. Modified PC refers to the materials obtained by adding different reinforcing materials or additives to the base PC resin to improve or enhance its original properties. Common types of modified PC include:
Transparent Casings and Goggles: PC’s high transparency and strength make it ideal for manufacturing various transparent casings and goggles.
A screw is used to inject the plastic material under high pressure into the mold. The shape of the mold and its design will determine processing factors such as the pressure and flow rate at which the plastic is injected into the mold. Shrinkage rate of the plastic is also considered to ensure the proper size of the final product, and to avoid deformation during cooling off.
Carbon Fiber Reinforced PC: Incorporating carbon fibers improves the material’s strength and thermal stability, suitable for lightweight and high-performance applications in aerospace and automotive industries.
These modified PC materials, with their unique combination of properties, find widespread applications in various industrial fields. Through modification, the application range of PC has been greatly expanded, meeting more stringent or specific performance requirements.
Plastic products are very common in our daily lives. Cases for computers, mobile phones and electronics, daily household items, storage containers, automobile panels, furniture etc. are nearly all made of plastic. The method most often used to produce these products is a process called plastic injection. This article will address some of the key points that need to be taken into consideration during the plastic injection molding process, and what processes are required for injection molding.
PC/ABS Alloy: Mixing PC with ABS (Acrylonitrile Butadiene Styrene) combines the high strength and heat resistance of PC with the ease of processing and surface smoothness of ABS, along with stress crack resistance. This is widely used in automotive parts, electronic device casings, and more.
Safety Helmets: The high impact resistance of PC makes it an ideal material for manufacturing safety helmets, which are extensively used in construction, sports, and other fields requiring head protection.
Optical Discs: Optical discs, such as CDs and DVDs, are typically made of PC material, benefiting from its excellent optical properties and processability.
In conclusion, mastering polycarbonate in injection molding opens up a realm of high-performance applications due to its unique properties. By understanding the right techniques, parameters, and modifications, manufacturers and designers can harness the full potential of PC, ensuring durable, high-quality, and versatile products in a wide range of industries.
PC/ASA Alloy: Alloying with ASA (Acrylate-Styrene-Acrylonitrile) improves weatherability and UV resistance, suitable for applications that are exposed outdoors for long periods.
High and Low Molecular Weight PC: High molecular weight PC has longer chain lengths, typically showing higher strength, better heat resistance, and superior mechanical properties. It’s suitable for high-performance applications like bulletproof materials and high-end mechanical parts. Conversely, low molecular weight PC, with shorter chain lengths, is easier to process and mold but usually means lower mechanical strength and heat resistance. This type of PC is more suitable for general consumer products and non-heavy-duty applications.
Glass Fiber Reinforced PC: Reinforcing PC with glass fibers enhances its mechanical strength and dimensional stability, making it more suitable for applications requiring high strength and rigidity.
Understanding the right parameters for injection molding of PC is crucial for optimal product quality. Here’s an overview:
The raw plastic material is melted at high temperature in the material tube of the injection molding machine. The processing temperature is carefully controlled according to the characteristics of the selected plastic material, the mold, and the product being produced.
Five plastic injection molding processes The plastic injection molding process has five stages: plasticizing, injection, pressure holding, cooling, and removing from the mold. Because these five stages of the manufacturing process continue simultaneously under controlled automated production, products can be efficiently produced in large quantities.
Polycarbonate (PC) plays a crucial role in various injection molding products due to its unique characteristics and is widely used in the following areas:
Casings for Electrical Products: PC is also widely used in manufacturing casings for electrical products, such as electric meter housings. The choice of PC is mainly due to its flame-retardant properties, weather resistance, and high strength and toughness, ensuring the safety and durability of electrical products.
These applications demonstrate the widespread use of PC in modern industry and everyday life. Its features, such as high transparency, strength, and flame retardancy, play an important role in many fields.
Flame Retardant PC: The addition of flame retardants improves PC’s flame retardant properties. Unmodified, PC has a V2 flame retardant rating, insufficient for many products. With added flame retardants, it can reach a V0 rating. Flame retardants can be halogenated or non-halogenated.
After the plastic raw materials has been injected into the mold, pressure is maintained on the plastic to ensure that it makes complete contact with the mold, and to avoid backflow of the plastic.
Electronic Device Casings: Including casings for computers and headphones, the application of PC material provides a solution that is lightweight, durable, and aesthetically pleasing.
Transparent PC: Although PC is inherently transparent, specific modifications can further enhance its transparency and optical properties, suitable for optical products and decorative items that require high transparency.
Polycarbonate (PC) is an amorphous thermoplastic material, a high polymer containing carbonate groups (-O-C(=O)-O-) in its molecular chain. It is synthesized through a polymerization reaction involving Bisphenol A (BPA) and Phosgene (COCl2). Known as a high-performance thermoplastic, PC is widely used for its outstanding transparency, heat resistance, and impact resistance.
These parameters should be adjusted and optimized according to actual machine conditions, material characteristics, and product design requirements. Correct injection molding parameters are essential for ensuring product quality and production efficiency.
What is plastic injection? Plastic injection technology is used to manufacture a broad range of plastic products that we use daily. The principle of injection molding is to heat and melt granular plastic pellets into a flowable liquid which is then injected under high pressure into a mold. After a period of cooling down, the mold is opened and the final completed plastic product is removed.
GETTING A QUOTE WITH LK-MOULD IS FREE AND SIMPLE.
FIND MORE OF OUR SERVICES:
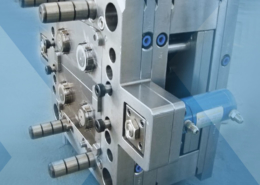
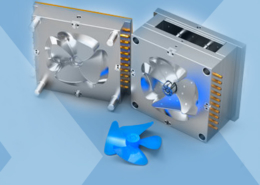
Plastic Molding

Rapid Prototyping
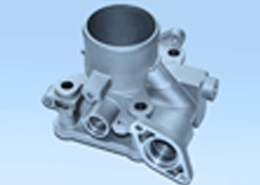
Pressure Die Casting
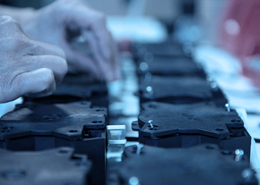
Parts Assembly
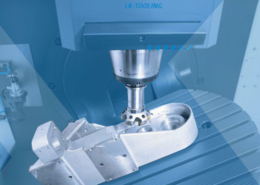