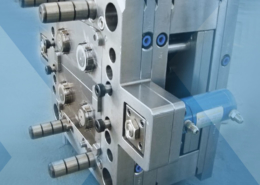
Plastic Injection Molding Service Provider - injection molding services
Author:gly Date: 2024-10-15
Let’s turn our attention to the “gold standard” for most molding projects: steel. Why does steel occupy the top spot over aluminum? The answer lies in three specific benefits.
Do businesses always want the durability of steel for a molding project? Not necessarily. Manufacturers choose aluminum most often when they need to quickly produce parts without requiring a very high volume. Since aluminum tools wear out faster, their optimal use is for lower part production volumes. They’re also an excellent choice when you need to rapidly produce prototype parts for testing, modification and redesign.
Injection molding is a common industrial manufacturing process with multiple businesses relying on the technique to produce items for every industry from healthcare to aerospace. However, not all injection mold tooling is the same—and the choice that you make regarding tooling materials for your project could have a significant impact on the outcome as well as your overall costs.
In simple terms, aluminum injection molding is an injection molding process that uses mold tooling made entirely out of aluminum rather than steel. Companies often use this process for large production runs, and the long-term durability of steel is a common demand. However, advances in tooling creation make the use of aluminum a more viable solution for certain scenarios. There is nothing different about the molding process aside from the tooling material.
As with aluminum, there are some downsides to using steel tooling. It’s crucial to include these factors in your considerations during the project planning stage.
To give a brief definition, polystyrene is the product obtained from polymerizing styrene. It is a common product used to manufacture many plastics found in the hospitality and food packaging industry. The demand for polystyrene in these industries is attributed to its features. We have identified some of these essential features that make polystyrene suitable for food packaging. They are as follows;
The short answer to the question above is yes. Polystyrene is one of the polymers that turns into its fluid state when it is heated. It is possible to channel the molten polystyrene into a suitable mold to form the plastic products at a standard temperature. While it is excellent for injection molding, there are some things to note about the process. This post is focused on polystyrene injection molding, its features, and how the best results can be obtained during and after the injection molding process.
Which should you choose: steel or aluminum? With clear pros and cons to each material, the answer depends on the specific needs of your projects. Partnering with an experienced and highly capable plastics manufacturer offers you the insights that you require to make smart decisions at every step, including in material selection.
Also, there is no chance of contamination with polystyrene if all other conditions are kept normal. The material is sterile, which is great for making different products in the medical industry.
There are several key benefits to using aluminum molds for plastic injection, not only its suitability for prototyping. Consider a few of the perks that make manufacturers choose aluminum just as often as steel.
Polystyrene injection moulding is the first step to making a whole range of products. These are products that we use every day and probably dispose of after a while. That is why it is essential to use environmentally friendly materials. Here are some of the main products that manufacturers design using polystyrene; The rigid feature of this polymer makes it an excellent choice for making food trays, spoons, cups, plates, knives, etc. Polystyrene is also used to make different sizes of bowls. We know there are still so many studies ongoing to discover more ways to use polystyrene. Therefore, we have kept our fingers crossed because it is certain this polymer can be used to make so many other products. Regarding this post, polystyrene is so effective for making products through injection moulding polystyrene. In its fluid form, it enters even the tiniest crevices to give the plastics products vivid details.
With Reliant Plastics, an injection molding provider with decades of experience, we can help you to make sense of your options and chart a course towards the best production decisions possible. To explore rapid prototyping with aluminum mold tooling or solutions for producing your parts at a larger scale, contact the Reliant Plastics team today for a free quote.
Overall, with aluminum molds, you’ll experience lower initial costs, lower rejection rates and more opportunities to quickly begin production thanks to shorter tooling production times. With steel, you’ll enjoy durability for very high part volumes, less concern about wear and tear, and opportunities to create more advanced parts.
Polystyrene has low thermal conductivity. This is why it is an essential polymer that can be used to package foods. We know that people who order meals from food delivery services need their food hot. Because polystyrene has a low thermal conductivity, it is the best product to keep contained food warm until the package is delivered.
The final plastic products made through injection molding polystyrene are transparent. These products have an attractive aesthetic appeal which is also great for the market. That is why polystyrene is a good choice for making fancy plastic cutleries for different food delivery services.
Polystyrene ranks among the top six polymers used in many industries to produce plastic products on a global scale. The high demand for polystyrene is all about its features which we have discussed below; Consistent fluid state In its molten form, polystyrene is consistent. This is one of the reasons why it is a favorite choice for producing different plastic products. If you want to make these products for bulk orders, then go for polystyrene. You can be sure that your products and the final outcome will all have the same best features for market sales. Engineers have rated polystyrene highly when designing and making plastic products with the best structural details. This is attributed to the consistency of the material after it has been melted. However, we always advise manufacturers to monitor their heating systems regularly. This will ensure the polystyrene is melted within the acceptable temperature range that is best for making plastics. Low energy consumption for melting We also observed that in factories, they can avoid excessive energy consumption when working with polystyrene. This is so because the material melts at a temperature that does not require too much energy. Viscosity Also, polystyrene has an amazingly viscous property. This is why it is best for mass-producing smaller plastic products that must have similar structural details. The viscous molten polystyrene flows easily into the injection mold, where it is shaped to get the desired outcome. We evaluated the melt flow index for polystyrene. It is very impressive. That is why many engineers claim it is among the easiest polymers to work with in the plastic industry. It is less dense than other polymers Compared to PE, we know that polystyrene has a significantly lower density. This is an excellent property that enhances its suitability for making different plastic products. Injection molded polystyrene weighs very little, which is why it is also preferred for food packaging. The food businesses can send out orders in bulk without worrying about the weight or impact on the courier service vehicles. Low shrinkage rate Many polymers shrink during injection molding. Shrinking can cause severe distortion in the product’s shape and physical features. It is best to evaluate the plastic material’s capacity to hold its form before and after injection molding. With polystyrene, there is a low chance of shrinkage. The final product will have sufficient plastic surface space to paste posters and logo designs depending on the business. Therefore, using a polystyrene injection moulding product also promotes your ability to create more awareness about the brand. Overall, we know that polystyrene has many of the desirable mechanical properties needed to perform adequate injection molding at any time. The conditions for this process are basic, which means all you need is a suitable injection molding machine to complete the process. Finally, regardless of the evident features, you should do preliminary tests to ensure that the polystyrene material you have is best for the injection molding machine you want to use to produce the plastics. Also, it is crucial to choose the right injection molding company. We are open to answering your inquiries and taking your orders. Contact us now.
Traditionally, injection mold tooling uses steel as the primary material, but it is not the only option. Today, aluminum molds have earned a place in the industry. Let’s explore aluminum injection molding and why it is worth your consideration in some cases.
It is not your regular plastics that are difficult to keep in shape. The hard frame of polystyrene makes it an excellent option for packaging different types of products.
While there are some obvious benefits to using aluminum, there are several reasons why steel molds for plastic injection has remained a dominant choice. Aluminum comes with some disadvantages you must consider, including the following.
GETTING A QUOTE WITH LK-MOULD IS FREE AND SIMPLE.
FIND MORE OF OUR SERVICES:
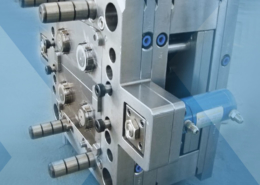
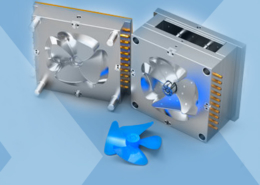
Plastic Molding

Rapid Prototyping
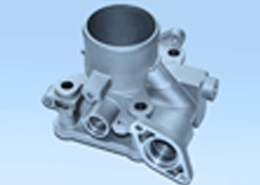
Pressure Die Casting
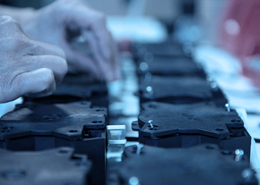
Parts Assembly
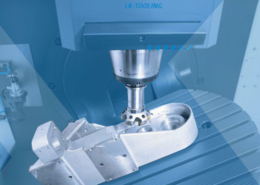