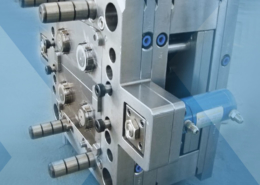
Mini Injection Molding: Revolutionizing Small-Scale Production
Author:gly Date: 2024-06-08
Introduction
In recent years, the manufacturing landscape has witnessed a paradigm shift towards miniaturization and customization. Mini injection molding has emerged as a pivotal technology in this era, enabling efficient production of small-scale plastic components with high precision and repeatability. This article delves into the world of mini injection molding, exploring its significance, applications, advantages, and challenges.
Advantages of Mini Injection Molding
Precision Engineering
Mini injection molding offers unparalleled precision in the fabrication of intricate plastic parts. The technology's ability to replicate complex geometries with minimal variance ensures consistent quality, making it indispensable in industries requiring micro-components, such as electronics and medical devices.
Cost-Effective Production
Unlike traditional injection molding, which often entails high setup costs and large batch sizes, mini injection molding offers a cost-effective alternative for small to medium production runs. Its lower material wastage, reduced energy consumption, and shorter cycle times contribute to significant cost savings, particularly for niche markets and prototyping.
Enhanced Design Flexibility
The miniature scale of components produced through mini injection molding enables greater design freedom and flexibility. Manufacturers can iterate rapidly on product designs, incorporate intricate features, and respond swiftly to market demands. This agility fosters innovation and accelerates product development cycles.
Applications of Mini Injection Molding
Electronics
The electronics industry relies heavily on miniaturized components for devices such as smartphones, wearables, and IoT gadgets. Mini injection molding facilitates the production of tiny, high-precision parts essential for miniaturized circuitry, connectors, and housings, driving advancements in compact electronics.
Medical Devices
In the medical sector, mini injection molding plays a critical role in manufacturing miniature components for diagnostic equipment, drug delivery devices, and surgical instruments. The technology's ability to produce intricate parts with biocompatible materials ensures safety, reliability, and compatibility with stringent regulatory standards.
Automotive
Even in the automotive industry, known for its large-scale production, mini injection molding finds application in manufacturing precision components for interior trim, sensors, and electronic control units. The demand for lightweight, space-efficient solutions in modern vehicles underscores the importance of miniaturization.
Challenges and Future Directions
Mini injection molding, despite its numerous advantages, faces challenges such as tooling complexity, material selection, and process optimization. Addressing these challenges requires ongoing research and development efforts focused on advancing materials science, refining process control techniques, and enhancing automation.
Conclusion
In conclusion, mini injection molding represents a transformative force in modern manufacturing, offering unparalleled precision, cost-effectiveness, and design flexibility for the production of small-scale plastic components. Its applications span across diverse industries, from electronics to healthcare, driving innovation and enabling the realization of intricate, miniature designs. While challenges persist, the ongoing evolution of mini injection molding holds promise for continued advancements in small-scale production technologies.
Through this exploration, we've uncovered the pivotal role of mini injection molding in shaping the future of manufacturing, underscoring its significance in an era characterized by miniaturization, customization, and innovation. As we look ahead, investment in research and development, collaboration across disciplines, and technological innovation will be essential in unlocking the full potential of mini injection molding and propelling manufacturing into new frontiers.
GETTING A QUOTE WITH LK-MOULD IS FREE AND SIMPLE.
FIND MORE OF OUR SERVICES:
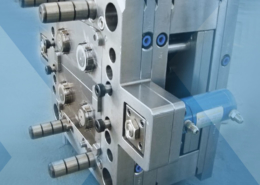
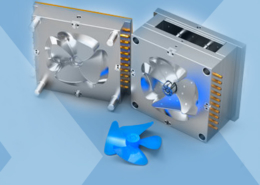
Plastic Molding

Rapid Prototyping
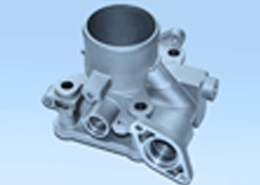
Pressure Die Casting
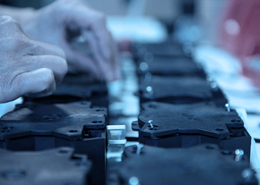
Parts Assembly
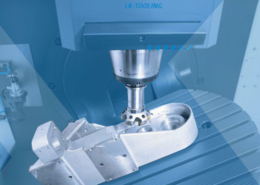