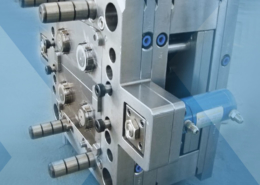
Unveiling the Advancements in Metal Molds for Plastic Fabrication
Author:gly Date: 2024-06-08
Metal molds for plastic fabrication represent a cornerstone of modern manufacturing, enabling the mass production of intricate plastic components with unparalleled precision and efficiency. This article aims to explore the intricacies and advancements in metal molds for plastic, providing readers with a comprehensive understanding of their significance, capabilities, and future implications.
Introduction: Pioneering Precision and Efficiency
Metal molds for plastic fabrication stand as a testament to human ingenuity, revolutionizing the manufacturing landscape by offering a cost-effective and scalable solution for producing complex plastic parts. From automotive components to consumer electronics, metal molds play a pivotal role in shaping various industries, driving innovation and streamlining production processes.
Background: A Legacy of Innovation
The evolution of metal molds for plastic fabrication traces back to the early 20th century, with the advent of injection molding technology. Over the decades, advancements in metallurgy, machining, and mold design have propelled the capabilities of metal molds, allowing for the production of increasingly intricate and high-quality plastic components. Today, metal molds serve as the backbone of modern manufacturing, facilitating the production of diverse products with unmatched precision and repeatability.
Advancements in Material Selection
One of the key advancements in metal molds for plastic fabrication lies in material selection. Traditional molds were primarily constructed from steel or aluminum alloys, offering durability and thermal stability. However, recent innovations have led to the development of advanced materials, such as beryllium copper and tool steels with enhanced wear resistance and thermal conductivity. These materials not only prolong the lifespan of molds but also improve part quality and production efficiency.
Enhanced Surface Treatments and Coatings
Surface treatments and coatings play a crucial role in extending the lifespan of metal molds and improving part quality. Advanced coatings, such as diamond-like carbon (DLC) and titanium nitride (TiN), offer superior wear resistance, reduce friction, and prevent adhesion during the molding process. Additionally, surface treatments, such as nitriding and ion implantation, further enhance the hardness and durability of metal molds, ensuring prolonged service life and consistent part quality.
Integration of Additive Manufacturing
The integration of additive manufacturing, particularly laser powder bed fusion (LPBF) and direct metal laser sintering (DMLS), has revolutionized the production of metal molds for plastic fabrication. These technologies enable the rapid prototyping and fabrication of complex mold geometries with minimal lead time and cost. By leveraging the design freedom afforded by additive manufacturing, manufacturers can optimize mold designs for enhanced performance and efficiency, further pushing the boundaries of what is achievable in plastic fabrication.
Conclusion: Shaping the Future of Manufacturing
In conclusion, metal molds for plastic fabrication represent a cornerstone of modern manufacturing, offering unmatched precision, efficiency, and versatility. With continuous advancements in material science, surface treatments, and additive manufacturing, the capabilities of metal molds continue to evolve, driving innovation and shaping the future of manufacturing. As we look ahead, the integration of emerging technologies, such as artificial intelligence and digital twin simulations, holds the promise of further enhancing the performance and efficiency of metal molds, ushering in a new era of manufacturing excellence.
GETTING A QUOTE WITH LK-MOULD IS FREE AND SIMPLE.
FIND MORE OF OUR SERVICES:
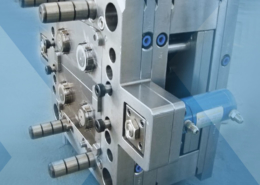
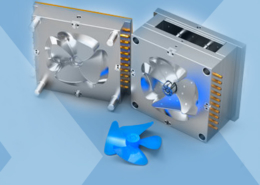
Plastic Molding

Rapid Prototyping
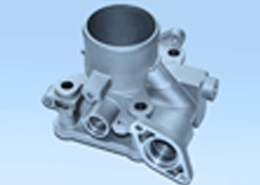
Pressure Die Casting
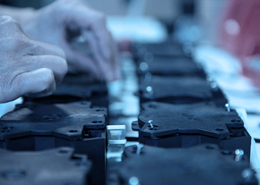
Parts Assembly
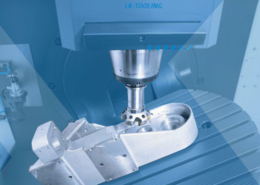