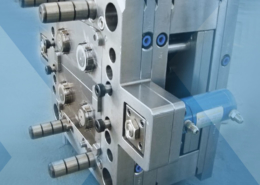
Plastic and aluminum injection molding - aluminum molds for plastic
Author:gly Date: 2024-10-15
The main difference between thermoset plastic and thermoplastic is that thermoplastics can be reheated and reformed, while thermoset plastics can not be remelted and remain in a permanent solid state once set. Once thermoset plastics have been hardened, they become more resistant to high temperatures than thermoplastics. They cannot be melted down again to form a new shape, unlike thermoplastics which can be reheated and cooled multiple times to form different shapes.
Just about any plastic part you can think of can be injection moulded. Commonly used plastics products made by injection moulding are –
The mould design, testing and toolmaking process increases the initial costs of injection moulding, particularly for complex geometries that may need to be tested for certain defects such as warpage and surface blemishes. A skilled and experienced injection moulding company will know how to mitigate risks involved with complex parts and cooling rates and will be able to advise on material selection.
Over moulding can be used to improve grip or reduce vibration on handheld tools or medical equipment by adding a soft touch material. Because it is a separate process, different coloured plastics can also be used to improve designs and aesthetics.
Owen Greenings & Mumford Ltd is the trading name of OGM Ltd, a company registered in England and Wales with company number 00742307
Cost-effectiveness, versatile material selection, efficiency, speed and design flexibility are some of the benefits of using plastic injection moulding for making your parts.
Clean room moulding is used for producing plastic parts in a climate-controlled and sterile environment to avoid the risk of contamination from dust and other particles. This is important for certain industries such as medical, precision electronics, aerospace and defence. Cleanroom injection moulding applications include medical device housings, dental products, surgical equipment, fluid delivery containers, semi-conductors and advanced electronics.
In addition to the Thermoplastic polymers listed, there is also a wide range of Thermoplastic Elastomers (TPE) and Thermoplastic Urethanes (TPU) as well as more unusual materials such as PCU (Polycarbonate Urethane) which passes USP XXII Class VI Biological Reaction. These are generally soft, rubber compounds, used for seals, cushioning features and soft touch surfaces. These materials can be moulded in on their own as components or bonded to polymers with matching chemistry, for a chemical bond, as opposed to a mechanical bond using either overmoulding or 2-shot moulding technology.
With over 55 years of experience providing original equipment manufacturers and manufacturing businesses with premier plastic injection molding services, we have the expertise and the capabilities to help you choose the perfect thermoplastic polymer for your product. Are you looking for a partner that will work with you to reduce lead times and production costs without sacrificing quality? Then you’ve come to the right place. Get in touch with us to discuss your options today!
Commodity Polymers – such as PP, PE and ABS are low cost and readily available. Many of these grades are ISO 10993 compliant for Biocompatibility.
GoodWag represents an innovative approach to managing pet waste with an all-in-one pail and scoop system designed for pet owners called the PooPail. The company’s mission is to simplify pet waste cleanup, making it quick, environmentally friendly, and less burdensome for pet owners. This project success story explores GoodWag and Universal Plastic Molds (UPM) collaboration, … Continue reading Plastic Molding Success Story: GoodWag & UPM Collaboration »
Plastic injection moulding is a highly adaptable manufacturing technique that enables efficient production of diverse plastic parts and components in large quantities. The process involves introducing plastic pellets into a heated chamber through a hopper. Inside the chamber, the plastic undergoes melting, blending, and is subsequently propelled under pressure (injected) into a metallic mould. As the molten plastic fills the mould, it rapidly cools and solidifies, assuming the precise shape of the intended component.
Engineering Polymers – such as Copolyester, PBT and PET, PC, PC-ABS, Nylon and PPO. These are more expensive than commodity polymers, but provide improved thermal properties, electrical, wear and solvent resistance. Most have a higher melting point and require more expertise and knowledge for processing.
Injection, dwelling and cooling – plastic pellets or granules are fed into a hopper where they are mixed with additives, fillers and pigments. These are then transported through a barrel by a reciprocating screw and heated to form hot, melted plastic resin. This is then injected through a nozzle into the cavity of the mould tool where it starts to cool and harden to form the shape of the component.
Understanding the terms related to the plastic injection moulding process and the features of your moulded parts will help you communicate effectively with plastic injection moulders, designers, or engineers involved in the process. In our demystifying blog series, we have aimed to explain common plastic injection moulding terminology.
Although the first plastic injection moulding machine was invented over 150 years ago, plastic injection moulding manufacturers continue to innovate and produce ever more complex parts. This is largely due to developments in new technology, new materials and increasing demand driven by the wide range of products that are now being mass produced from plastic.
Choosing a plastic injection moulding company is a critical decision that should follow a similar approach as selecting any other crucial supplier for your business. Our series of blogs is designed to provide you with valuable insights into the factors you need to consider when choosing the right plastic injection moulding partner.
High Performance Polymers – such as polyketones, polysulfones (PPSU), polyarylates, polyamides, and liquid crystal polymers (LCP) such as PEEK are characterised by a combination of high modulus, melting points (greater than 250°C), biocompatibility, electrical insulation and low-friction surfaces.
A further reason is design freedom and rapid prototyping that can bring new innovations to market much quicker than some other manufacturing processes.
3k or 3-shot moulding is also known as triple shot injection moulding and is similar to 2-shot but combines three different materials often to improve the strength and performance of the finished part. This process is even more complex and requires an experienced injection moulding company with specialist machines.
These are just a few examples. The process allows for precise and complex shapes, making it a popular choice for a wide range of products. When selecting a plastic injection moulding company for your large part production, it is crucial to consider several key factors.
Additives are often mixed with plastic resin during the injection moulding process and coatings are added to the moulded component as part of the finishing process.
By exploring resources such as the blog “How Does an Injection Moulding Machine Work?“, you can gain a comprehensive understanding of the steps involved in plastic injection moulding.
Let’s explore the over moulding and insert moulding processes in detail and understand the benefits of using these plastic injection moulding methods
Think of thermoplastics like cheese and thermoset plastics like a burger patty. Cheese comes in a variety of different shapes but when melted it can take on a new form. Once cooked, a burger patty can’t be melted to take on a new form – it can only be further charred, which can ruin the quality of the burger.
Selecting the right material for plastic injection moulding is a crucial step that requires careful consideration. To make an informed decision, it is essential to evaluate several aspects.
Additives include pigments, glass or carbon fibres for strength and stainless-steel fibres for controlling electromagnetic interference (EMI) and radiofrequency interference (RFI). Fillers such as clay or talc may also be added to improve hardness of the finished product or reduce warpage during the injection moulding process.
2K or 2-shot moulding is sometimes also called twin shot or double injection moulding. This process can produce complicated parts by blending two completely different types of thermoplastic. It is different to overmoulding because it involves controlling the injection of the different materials in one cycle which is an automated process requiring specialist 2-shot moulding machines.
Plastic polymer materials used for plastic injection moulding are called thermoplastics because they become molten when heated but harden again when cooled. The mould design, properties required for the finished component and its function will determine thermoplastic selection.
There are several reasons why the injection moulding process is popular for producing plastic parts. Simply put, it enables uniform, consistent, high-quality parts to be made in large volumes, within relatively short timeframes and with low material waste which contributes to a low overall part cost. Due to the accuracy and ability to produce complex geometries, there is also little need for finishing once the part has been successfully ejected from the mould.
Some plastic injection moulders offer a full end-to-end service which adds considerable value throughout the design and manufacturing process. This includes highly skilled services such as design, prototyping and toolmaking through to testing and a full validation service.
When it comes to injection molding, two main types of polymers are used: thermoplastics and thermosetting plastics. Even though they sound alike and share similarities, they have very different properties and are used in a variety of unique applications.
Insert moulding is often required to add strength and functional elements to a product. The components that are inserted are usually made from metal such as threaded screws that will allow the finished product to be firmly held together with the fewest parts possible.
GETTING A QUOTE WITH LK-MOULD IS FREE AND SIMPLE.
FIND MORE OF OUR SERVICES:
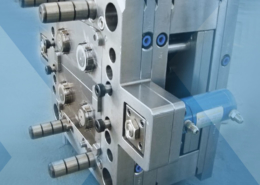
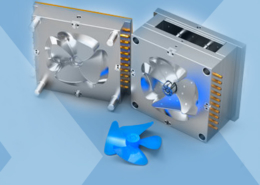
Plastic Molding

Rapid Prototyping
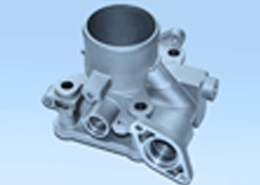
Pressure Die Casting
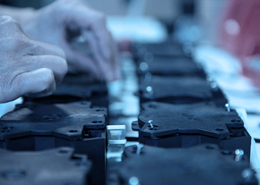
Parts Assembly
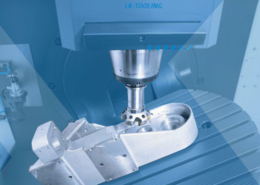