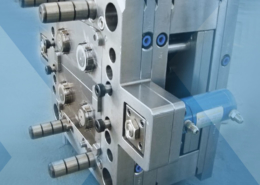
Plastic and aluminum injection molding - aluminum mold for plastic injection
Author:gly Date: 2024-10-15
The decision on whether to injection mould using TPE or to compression mould using rubber is usually a function of quantity and service environment.
An aluminum injection mold will last 3,000 to 10,000 cycles. Each cycle represents the mold closing, the mold being filled, the mold opening, and the part being ejected. If the mold has a single cavity, customers can expect to get up to 10,000 parts from an aluminum mold.
In contrast TPE’s are processed on conventional injection moulding machines with cycle times similar to moulding conventional thermoplastics.
In contrast TPE’s require tooling designed and manufactured to injection moulding standards. Material is processed and injected in the same way as ABS or PC would be for rigid parts. It is more sophisticated than compression mould tooling and as a result more expensive.
Aluminum can be used to make molds for the injection molding process. Aluminum is an affordable material that is easy to work with and has many applications. However, aluminum molds, while slightly cheaper to produce, are considered inferior to steel molds. ICOMold by Fathom uses only high-strength steel to manufacture injection molds.
We are here to help, whether you have 30 years of experience and know exactly what you need or are just starting out on your 3d printing experience and need some advice. Either way we have capability to deliver what you need, when you need it.
Materials that can flex are frequently referred to generically as rubbers. However, there are two basic categories simply differentiated by their processing technique, thermoplastic and thermoset.
Flash is what happens when the plastic injection material seeps into the mold seams during the injection process. The excess material will need to be removed in post-processing. This post-processing can be expensive depending on the amount of flash and the work required to remove it. Aluminum molds for injection molding are prone to flash. Aluminum is a soft metal and is therefore easier to deform and allow the injected material to leak out of the machined cavity. Steel is a harder material, which reduces the chance for flash. Steel molds will not deform as easily as an aluminum mold.
Aluminum molds have a limited manufacturing life span. Aluminum is a soft metal and cannot with stand the repeated pressure and temperature of the injection molding process. Aluminum molds will produce 3,000 to 10,000 cycles before needing to be replaced. Steel molds are more resilient and will produce 30,000 to 100,000 cycles before needing to be replaced or repaired.
Steel molds are much more durable and can last up to 100,000 cycles or more. While aluminum molds may be cheaper to machine, the steel mold will last ten times as long – producing parts long after the aluminum mold has been scrapped and replaced several times. The cost of machining a new aluminum mold after every 10,000 cycles will add up quickly.
*(Note flexibility can be achieved through additive techniques but tear strength, chemical resistance and elongation to break will be significantly reduced.)
An aluminum mold will hold up for short part runs and is an ideal choice for small orders. However, steel molds are more durable and suited for extended manufacturing runs. Aluminum molds do not have the corrosion resistance or thermal stability found in steel molds. Steel molds are also better able to resist the constant wear and tear of the injection molding process. These characteristics allow the steel injection molds to achieve higher production cycles and withstand non-conformities in the product. Aluminum molds must be anodized or plated with nickel to reach the same level of hardness as steel molds. Anodizing and plating will increase the tooling cost and negate the benefit of using the less expensive aluminum to machine the mold.
ICOMold’s fast-turn, low-cost, high-value injection molding enhanced by joining Fathom’s manufacturing platform. Learn More
We are product developers. We use our passion and experience to build manufacturing partnerships that our customers can trust. With UK onsite toolmaking and injection moulding we are always here to support your requirements, be they low volume fast turnaround development parts or ‘make to stock’ with a scheduled call off.
Quantity is important as the cycle times of the two processes are wildly different. Rubber (whether synthetic or natural) is a thermoset and as such must cross link during processing – which is referred to as vulcanisation. Depending on a variety of parameters, vulcanisation can take from minutes to hours.
However, ultimately the additional expense of injection mould tooling and faster cycle time will pay off, and needs to be considered. (material properties being equal)
However neither of these options will truly emulate a production TPE or rubber, especially in areas such as elongation, temperature resistance or stiction. Thus if the goal is to create anything more than a visual prototype there is little option but to manufacture a bridge tool and prototype in the production intent material.
Prototyping flexible parts can be a challenge. Whilst it is possible to 3D print materials that demonstrate a level of elongation in a variety of harnesses’, their properties fall well short of production intent materials.* Vacuum Casting can offer a better solution, although more costly, again in a range of harnesses’.
If you need your component to be recyclable, then thermoplastics are your only option. Rubbers being a thermoset means components are destined for landfill at the end of their life.
Thermoplastic elastomers (TPE’s) are copolymers that are a blend of rubber and plastic, processed by injection moulding or extrusion. Within TPE’s there are six sub sets, which is where names like TPU and TPV come from.
Plunkett Associates can support both your prototyping requirements and production requirements, in either class of materials. Drawing on strengths in both tooling and moulding, we will ensure you get to market on time.
Steel molds can be modified and repaired after initial tooling. Aluminum molds cannot be changed or repaired if there is a problem with the initial design. Steel molds can be modified with welding. If a part re-design requires less plastic in an area, and therefore, more steel in that area of the injection mold tooling, the steel mold can be modified. This is not the case with aluminum. Consider using a steel mold if there is any chance your part may undergo design revisions that will require modifications. Steel molds can also be repaired in some instances. This will save customers thousands of dollars by simply repairing the mold instead of machining a new mold. The ability to repair a mold will depend on the tooling. Not all steel molds will be able to be repaired.
Thus for a low call off of say 100 parts per year, the lower tool cost and greater cycle time of compression moulding is unlikely to be an issue. As the quantities rise, the number of cavities in a tool can be increased, so a ten, twenty or more cavity tool is possible (geometry permitting).
Steel molds offer more options for surface finishes. The high-density nature of steel allows more texture selections. Custom, tall, or deep details in the tooling can be achieved by adding steel inserts. The number of surface finishes possible with an aluminum mold is limited and custom finishes are not available. The difference in available surface finishes is based on the mold material. This limitation affects all mold makers, not just ICOMold.
Aluminum cannot be used as the injection molded material. The manufacturing process of metal injection molding does exist, however, aluminum cannot be injected molded. ICOMold by Fathom specializes in injection molding custom plastic parts. ICOMold can also manufacture custom metal parts with Computer Numerical Control (CNC) machining. As part of the Fathom manufacturing network, ICOMold will work to match customers to manufacturers in order to meet their specific aluminum machining needs.
Aluminum injection molds cannot be used for complex parts. Aluminum is a softer metal that can only be used for simple injection molded designs. Designs with complex geometry will need to be made with a steel mold. The steel is better able to handle complex designs and any thin walls in the design. Aluminum molds cannot handle thin walls or complex geometry because the metal is not as structurally strong as steel and will deform during the molding process. This is a universal limitation for all mold makers – not unique to the ICOMold by Fathom manufacturing process.
Injection molded material can impact the life expectancy of the tool. Aggressive materials like ASA/glass-filled Nylon and Ultem can reduce the lifespan of injection molds. Steel injection molds can be hardened through heat treatment to become extremely durable. The heat treatment will allow steel molds to handle the aggressive material without issue. Aluminum molds for injection molding cannot be hardened and will not be able to handle the high injection pressure and temperature required when injecting these aggressive materials.
Service environment is also important and both maximum and minimum operating temperatures as well as exposure to solvents need to be taken into consideration. Some rubbers can be better at retaining there elastomeric properties, particularly in high temperature environments and silicones excel in situations where the material must be highly inert.
Tooling is a requirement to process either option. A large range of rubbers including silicone, nitrile, neoprene, EPDM and Viton can be moulded in compression tooling. This is relatively simple compared to injection mould tooling and multiple cavities can be used to offset longer cycle times.
Flexible components are present in most assemblies. Whether you want a simple gasket, a seal, a more intricate connector, or a bellows, the common denominator is that the part is required to flex in its operation or assembly.
Injection molding is a manufacturing process that uses a metal mold to manufacture large numbers of plastic parts. ICOMold by Fathom uses only high-strength steel when making plastic injection molds. Steel molds have several advantages over aluminum molds. Steel molds consistently produce a higher quality product when compared to aluminum molds. Steel molds are built to last — up to ten times longer than aluminum molds. Steel molds may have a higher up-front price but they can save significant time and money down the road.
We are here to help, whether you have 30 years of experience and know exactly what you need or are just starting out on your 3d printing experience and need some advice. Either way we have capability to deliver what you need, when you need it.
GETTING A QUOTE WITH LK-MOULD IS FREE AND SIMPLE.
FIND MORE OF OUR SERVICES:
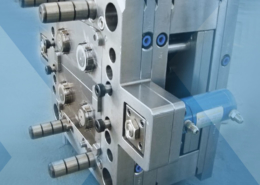
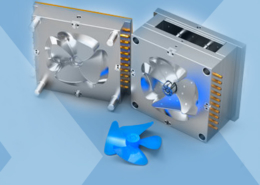
Plastic Molding

Rapid Prototyping
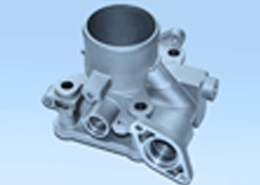
Pressure Die Casting
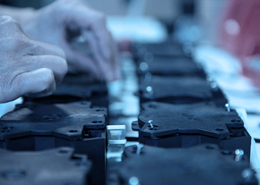
Parts Assembly
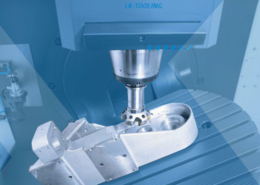