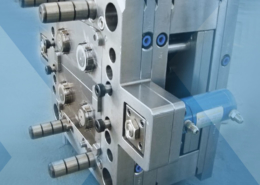
Plastech Solutions Ltd - Home - plastech molding solutions
Author:gly Date: 2024-10-15
Proto Labs, Inc. 5540 Pioneer Creek Dr. Maple Plain, MN 55359 United States P: 877-479-3680 F: 763-479-2679 E: [email protected]
Polyethylene is the most widely used form of plastic. Because of its unique chemical properties, polyethylene is a diverse plastic with many uses. This plastic is lightweight, tough, resistant to corrosion, impermeable, and a great insulator.
Instead of several heavy, metal pieces, your design can become one lightweight polyethylene piece. We can also create variable wall thicknesses, to create a pleasing, durable custom molded part for you. Aesthetics are made easier with polyethylene. Changing colors, creating a piece that is opaque or translucent is easy with a polyethylene mold. Parts can be used as insulators, are relatively stress-free, and resist corrosion.
The term “back to the drawing board” is more than a cliché. Planning for and producing multiple iterations of any product is the most effective way to reduce overall project costs. And this is no different than when designing a part made from plastic. It also helps avoid long-term risk and delivers the most optimized part design possible. And no matter how skilled the engineer or powerful the design software they use, that means prototyping.
Part size, surface finish quality and feature size/resolution requirements should also be considered when choosing a service for prototyping.
The terms “plastic injection mold” and “prototyping” have long been exclusive of one another. That’s because the high-volume production tooling needed to manufacture the lion's share of plastic parts is both expensive and requires months to develop. We changed this paradigm at Protolabs with quick-turn aluminum tooling, which can mold hundreds of prototype parts and is typically delivered within a week or so.
Get machined parts anodized and chromate plated with our quick-turn finishing option. Eligible materials include aluminum 6061/6082 and 7075.
Converting your product to plastic has many advantages for you. Molding with polyethylene is an excellent choice if your business wants to cut costs, make product design more effective, increase durability, or simplify an intricate, outdated part.
Tough Black (Loctite Henkel 3843) and Ceramic-Filled (BASF 3280) are two new advanced photopolymer materials now available for 3D printing.
Quality, innovation, and value have laid the foundation for our success as a nationwide rotational molder. Roto Plastics goes above and beyond by rotomolding custom parts with polyethylene to meet and exceed our customers' needs. We listen to our clients' concerns and assist them in creating the parts they need, even if they've never considered plastics for their product before.
Designers at Roto Plastics are leaders in converting metal products to polyethylene parts. Consider converting your metal piece into plastic.
Metal is expensive and heavy. Polyethylene molds are inexpensive and lightweight, which cuts costs in transportation as well as production. With a polyethylene mold, you can create a varied design with hollow parts, complex undercuts, or varied shapes and sizes. Roto Plastics can take an intricate design and simplify it using polyethylene.
Let’s start the discussion with a brief overview of the technology that quite literally launched the rapid prototyping industry more than three decades ago: 3D printing. In those early days, the only option was stereolithography (SLA). Today, however, manufacturers can choose from a range of technologies, including selective laser sintering (SLS), jetting processes like PolyJet and Multi Jet Fusion (MJF), and SLA’s faster though slightly less accurate cousin, Carbon DLS.
Fortunately, there are several options available for prototyping plastic parts. Each provides its own distinct advantages (and limitations) that might determine which is most suitable for your application.
Our digital factories create prototypes and low-volume parts fast, while our manufacturing network, offers advanced capabilities and volume pricing.
Because Protolabs has always specialized in fast turnarounds, we've developed standardized tooling sets that allow us to deliver custom-machined parts in a day or two. The lead time is similar to 3D printing, and the price is not significantly higher (depending on the part geometry,
The caveat is that it takes time. Time to design the mold, time to machine it, time for testing and final approval. It's still much faster and far less costly than the "hard tool" alternative just described, but could be prohibitively expensive in situations where 3D printing or machining will solve the immediate problem. As suggested earlier, it's a lot to think about, so give us a call or upload your part design to our digital quoting platform to evaluate the options and receive automated design for manufacturability (DFM) feedback. Happy plastic prototyping.
For example, medical device manufacturers must assess the ergonomics and functionality of a surgical instrument before offering it to physicians. Commercial drone designers might make dozens of test flights in wind tunnels to determine their craft’s airworthiness, robot builders want to see how efficiently their latest droid design performs its assigned tasks, and smart automakers perform numerous form, fit, and function checks on countless components with every new model. Each of these activities requires a prototype (or more likely, multiple prototypes).
Whatever manufacturing technology you choose for a plastic prototype, ensuring that your part is manufacturable via the intended production method is crucial. In other words, don’t paint yourself into a corner by 3D printing prototypes, only to discover when quantities ramp up that the parts can’t be injection molded.
There's no need for a lengthy list of pros and cons here, as this decision tree has but one or two branches. If you need a hundred or more injection molded prototypes for functional testing, quick-turn tools give customers parts made of real material, really fast, and boasting tolerances and surface finishes nearly identical to those made with production tooling. Quick-turn molds can also serve as a bridge tool until that production mold is complete, or for pilot runs to test the molded part design.
Our helpful design aid demonstrates part features that are too thin or too thick, bad bosses, right and wrong ribs, and other considerations to be mindful of while designing parts for injection molding.
We’ve published numerous design tips covering these technologies, so refer to those for the technical details behind accuracy, raw material selection, and surface finish capabilities. Suffice it to say that all are excellent for making prototypes; several are also fast enough and their feedstocks robust enough to support low-volume, end-use part production. Here are some additional benefits and challenges with 3D printing.
This is especially true for plastic parts, where demand for the winning design hopefully skyrockets and requires subsequent investment in high-volume production tooling, aka plastic injection molds. What better way to avoid a costly design mistake than to prototype until it is perfected? On the flip side, manufacturers from all industries often evaluate their newest metal brainchildren by first 3D printing, machining, or molding plastic versions of them. Again, it’s about reaching the finish line in the most effective manner.
GETTING A QUOTE WITH LK-MOULD IS FREE AND SIMPLE.
FIND MORE OF OUR SERVICES:
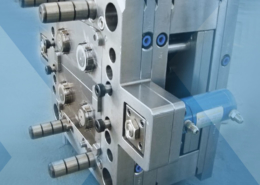
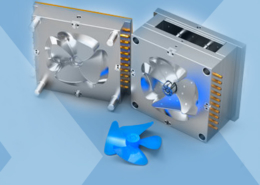
Plastic Molding

Rapid Prototyping
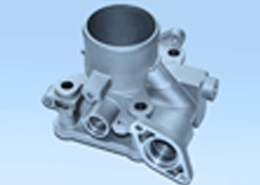
Pressure Die Casting
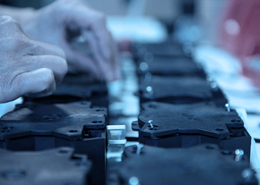
Parts Assembly
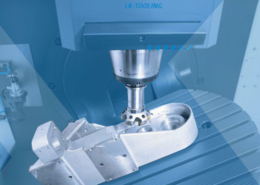