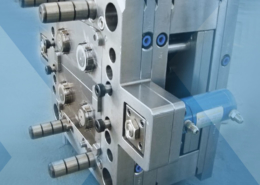
Plastech Molding Solutions, 50 Mellen St, Hopedale, MA ... - plastech molding so
Author:gly Date: 2024-10-15
To ensure consistent, defect-free part production using high-heat resins, tooling design must address several key factors:
PP can also be combined with other materials, such as rubber, to create a stronger copolymer. However, polypropylene is not without its downsides. This polymer is susceptible to UV degradation, has poor resistance to chlorinated solvents, and has limits regarding very high-temperature applications, accompanied by high flammability.
For complex applications, there are rarely any easy solutions — and that includes identifying a high-temperature thermoplastic and maximizing its use during injection molding.
PEEK material falls within the family of semicrystalline thermoplastics known as Polyaryletherketones (PAEK). Polymers within the PAEK plastics classification all have high-temperature stability and excellent mechanical strength. Key differences appear in the temperatures at which the polymers’ textures change — the glass transition temperature (Tg) and melt temperature (Tm).
Mention “high-temperature thermoplastic” and chances are that polyether ether ketone (PEEK) comes to mind. Its high heat tolerance, mechanical strength, and chemical resistance make PEEK resin ideal for many demanding applications including those in the automotive, electronics, aerospace, medical, and other markets. But is it the only choice?
Plastic injection molding offers a wide variety of resins providing all sorts of unique characteristics. But polypropylene is one of the most popular material choices for businesses looking to create tough and flexible parts. The customizability, easy processing traits, and affordability of this plastic allow it to be used in many diverse applications. If you’re wondering whether you should consider this material for your next project, we’re here to help by providing the benefits, types, and applications of polypropylene in plastic injection molding.
Due to its positive traits and affordability, there’s much to gain when using polypropylene in plastic injection molding. Knowing its characteristics opens up so many possibilities when it comes to planning your next project. At Midstate Mold, we have experienced molding numerous different thermoplastics, and we can perform production on your parts and closely inspect them for quality. If you’re looking to partner with a manufacturer experienced with polypropylene and so much more, contact us today.
Filed Under: Our blog Tagged With: affordable plastics, block copolymer, homopolymer, plastic injection molding, Polypropylene, PP, random copolymer, Thermoplastic Highlight, thermoplastics, types of polypropylene
While not directly related to tool design, it’s important to note injection molding at elevated temperatures is particularly susceptible to moisture. Materials must be completely dry prior to processing or failure could occur even when the most accurate tools are used.
Myriad considerations go into the final decision. It requires input from an experienced injection molding partner such as Kaysun, and guidance like that which you'll find in our white paper, Processing High-Temperature and Engineered-Grade Resins. Click the button below to download your copy of this valuable resource now.
In short, Tg correlates to the temperature at which a solid, glassy polymer transitions to a viscous, pliable state. Tm refers to the temperature at which the structured molecules of crystalline polymers become random chains of molecules (or, amorphous) — essentially, the thermoplastic begins to melt.
Polypropylene (PP) is so prevalent in plastic injection molding because it is amongst the least expensive thermoplastics available, yet it boasts so many beneficial characteristics. Some of the biggest advantages of using polypropylene in plastic injection molding include:
There are two main types of PP: homopolymers and copolymers. However, copolymers can be broken down into two separate categories: random copolymers and block copolymers. Here are some of the differences between these market-available PP types:
Typically, high-temperature resins can be run on conventional injection molding equipment — with one important caveat. The tooling used with PAEK materials must be able to achieve and withstand high temperatures (at least 165℃) in order to process unreinforced and reinforced PEEK, PEK, PEEKK, and other PAEK materials at processing melt temperatures generally ranging from 370℃ to 410℃.
The Tg and Tm temperatures of PAEK plastics don’t vary greatly, yet even the seemingly minor differences can impact critical properties of an injection-molded part, including:
Due to PP’s beneficial physical, chemical, and mechanical properties, there are countless applications for which this material is used. PP is a food-grade thermoplastic, making it safe for food containers, cups, and children’s toys. Also, due to it being lightweight and strong, it can act as a replacement for metal parts in the automotive industry. Its chemical resistance also makes it ideal for use in medical products, and it’s even durable enough to be used in autoclaves. Beyond these examples, this plastic is also used in construction, household appliances, power tools, and much more.
GETTING A QUOTE WITH LK-MOULD IS FREE AND SIMPLE.
FIND MORE OF OUR SERVICES:
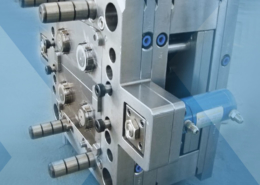
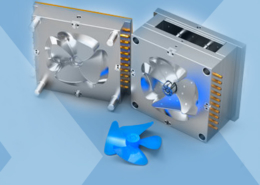
Plastic Molding

Rapid Prototyping
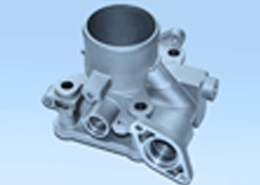
Pressure Die Casting
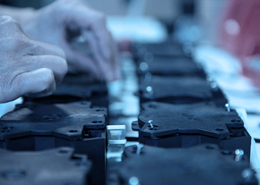
Parts Assembly
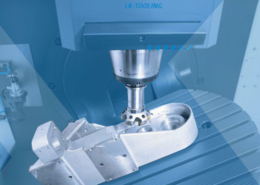