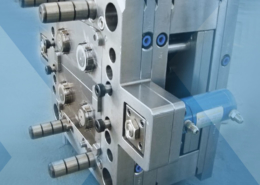
PEEK Injection Molding: Properties ... - Prototool - peek injection
Author:gly Date: 2024-10-15
(1) Poor plastic fluidity – If the plastic material doesn’t feature a great fluidity, it will solidify before reaching the furthest end of the cavity or flowing to the overflow tank, which often results in a short shot.
(2) Try to evenly mix the recycled material and the raw material. Because the recycled pellets, as well as their density are relatively larger than the raw material, if the mixing is not uniform, the amount of the molten material is easily reduced, resulting in reduced injection volume accordingly.
All in all, the reasons for short shot are multifaceted, which are also mutually restrictive and mutually influential. To reduce and correct such a defect, we need to make adjustments through an overall consideration of the relationship between these aspects, while making constant practice and accumulating experience continuously to quickly identify the causes of underfill, thereby reducing resource waste and improving product yield.
Welcome to BPY Plastics Ltd, your one-stop shop for all your injection moulding needs! As a leading supplier in the industry, we offer a wide range of products and services to meet our customers' needs. Our commitment to quality and innovation has earned us a reputation for excellence.
(1) Improper injection molding process – The low barrel temperature, slow injection speed, short injection time, and insufficient backpressure lead to a shortage of plastic.
In order to eliminate such defects, the melt / mold temperature, and the injection pressure / speed can be increased to allow the melt to reach the end of the cavity before solidifying. In such a case, a great plastic fluidity is of particular importance, so selecting the plastic with a better fluidity is also a solution. If the flow coverage is too long and the plastic cannot properly fill the injection molded part, it is recommended to change the gate location to reduce the plastic flow length.
These properties make Nylon 6 a versatile and reliable material for a wide range of injection molding applications, including automotive components, electrical housings, consumer goods, industrial parts and many more.
(3) Poor venting. When filling the cavity, air is trapped to cause counter pressure. When the melt is injected into the cavity, the cavity is often closed by the melt in the very beginning, with air trapped in the unfilled local areas. Also, because the filling speed is too fast, sometimes there is not enough time for the air to be vented through the parting surface but compressed instead, resulting in partial unfilled areas in the cavity, thus short shot in the molded part.
Nylon 6 quickly found widespread use due to its excellent mechanical properties, chemical resistance, and versatility in applications ranging from textiles and carpets to industrial and automotive parts.
During the product design process, the principle of uniform wall thickness must be followed. If it is impossible to maintain a uniform wall thickness, please change the mold design in a timely manner. Increase the number of runners or ribs in the area where the feeding is difficult, so as to avoid the defect of underfill caused by too-thin wall thickness.
(2) Oversupply of plastic – If too much plastic enters the barrel, the injection pressure is lost due to the compression of the pellets, thus reducing the pressure required to inject the melt from the nozzle, which is necessary for injection molding, resulting in insufficient injection pressure. The solution is to adjust the amount of feed, i.e., the amount of melt, and make the amount just right for the molding.
BPY work with Nylon 6 on a daily basis, making parts like screws for numberplates, corner protectors for amplifiers, and parts for shooting sticks among others.
(1) Local short shot caused by the flow imbalance in each cavity of a multi-cavity mold – When the injection molding capacity of the injection molding machine is sufficient, this defect is mainly caused by the uneven flow in each gate, i.e., the mold cavities are not distributed in a balanced way.
(1) Insufficient injection molding capacity – This is caused by an overestimation of the capacity of the injection molding machine, which may also occur due to insufficient plasticizing capacity or insufficient injection volume. Among them, the insufficient plasticizing capability can be increased by extending the heating time, increasing the screw speed and raising the backpressure. If the injection volume is not high enough, the injection machine with a larger injection capacity can be used to solved the problem.
(2) The flow range of the melt is too long, and the flow resistance is too large – The parts that hinder the flow of the melt include the nozzle, the sprue, the runner, the gate, and the thin walls of a product. The flow resistance of the nozzle can be reduced by increasing the nozzle diameter / temperature, and using a nozzle with a small flow resistance.
If you have an injection moulding project and are considering using Nylon 6, please get in touch with our technical team on 01280 706335 for a free consultation!
Short shot refers to incomplete filling of a mold cavity which results in the production of an incomplete part due to the insufficient plastic fluidity. The main causes are the inappropriate injection pressure and speed (including excessive pressure loss caused by resistance), which are mainly affected by the following aspects:
(3) Unstable production cycle – Frequent machine shutdown, and production inconsistent with the normal cycle make some plastics stay in the barrel for too long with reduced density and viscosity, thus resulting in plastic underfill.
Nylon 6 was discovered by Paul Schlack, a German chemist working for IG Farben, a major German chemical conglomerate, in 1938. Schlack developed Nylon 6 through the polymerization of caprolactam, a process that resulted in a material with properties similar to those of Nylon 6,6, which had been developed by Wallace Carothers at DuPont a few years earlier.
GETTING A QUOTE WITH LK-MOULD IS FREE AND SIMPLE.
FIND MORE OF OUR SERVICES:
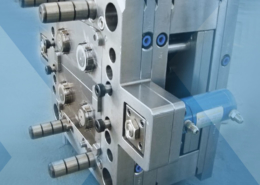
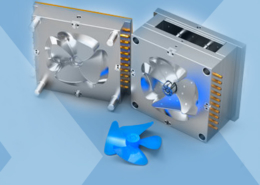
Plastic Molding

Rapid Prototyping
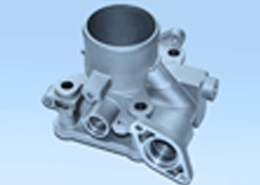
Pressure Die Casting
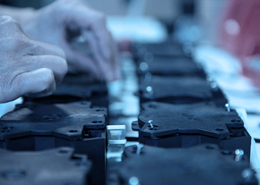
Parts Assembly
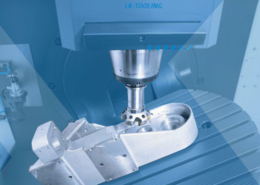