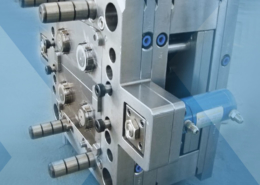
Ontario - Plastic Molding Manufacturers - plastic part manufacturer
Author:gly Date: 2024-10-15
Any type of gate may be used. When using tunnel gates, the short type is preferred. Insulated, hot tip runners are preferred for homopolymers; both internally and externally heated hot runners may be used in the case of copolymers.
If you're up for an even deeper dive in the world of plastic injection molding, check out this video from a previous blog post. In it, one of our capable engineers explains the ins and outs of injection molding. The video is about 12 minutes long, and packed with great information.
Acetals are tough, resilient materials and exhibit good creep resistance, dimensional stability, and impact resistance even at low temperatures. Acetal grades are either homopolymers or copolymers. Homopolymers have better tensile strength, fatigue resistance and hardness but are difficult to process. Copolymers have better thermal stability, chemical resistance and processibility. Both homopolymers and copolymers are crystalline and have low moisture absorption.
Acetals have a low coefficient of friction and good dimensional stability. This makes it ideal for use in gears and bearings. Due to its high temperature resistance, it is used in plumbing (valve and pump housings), and lawn equipment.
No one would blame you for looking for a glossary of terms right about now. Fear not. Below, we break down the components of an injection mold in simple, easy-to-understand language. It even includes labeled cutaway drawings. I promise, if you didn't understand how an injection mold worked before, you will after reading this.
POM injection molding processing condition Generic Class POM (Polyacetal or Polyoxymethylene) Applications Acetals have a low coefficient of friction and good dimensional stability. This makes it ideal for use in gears and bearings. Due to its high temperature resistance, it is used in plumbing (valve and pump housings), and lawn equipment. Injection Molding processing conditions Drying Not usually required but the material should be stored in a dry atmosphere. Melt Temperature 180 - 230 C (356 - 446 F) for homopolymer; 190 - 210 C (374 - 410 F) for copolymer Mold Temperature 50 - 105 C (122 - 221 F); Higher mold temperatures are preferred for precision molding which reduce post-molding shrinkage Material Injection Pressure 70 - 120 MPa Injection Speed Medium - High Runners and Gates Any type of gate may be used. When using tunnel gates, the short type is preferred. Insulated, hot tip runners are preferred for homopolymers; both internally and externally heated hot runners may be used in the case of copolymers. If you need high quality cutom aluminium casting parts Pls contact us sales@viewmold.com If you need high quality injection mold tooling, Contact us. Chemical and Physical Properties Acetals are tough, resilient materials and exhibit good creep resistance, dimensional stability, and impact resistance even at low temperatures. Acetal grades are either homopolymers or copolymers. Homopolymers have better tensile strength, fatigue resistance and hardness but are difficult to process. Copolymers have better thermal stability, chemical resistance and processibility. Both homopolymers and copolymers are crystalline and have low moisture absorption. Copolymers may be used continuously at air temperatures up to 100 C (212 F); homopolymers have slightly higher temperature resistance. Many grades of acetal materials are available, tailored to different applications. High crystallinity levels of acetals lead to relatively high shrinkage levels of 0.02 - 0.035 mm/mm. Differential shrinkage is observed with reinforced grades. If you need to look for more plastic resin injection molding processing condition, could you please click it. If you need high quality plastic extrusion services, Pls contact us sales@viewmold.com If you need high quality sheet metal parts, Pls contact us sales@viewmold.com The following is other plastic processing condition: ABS injection molding processing condition, HDPE injection molding processing condition, LDPE injection molding processing condition, PA12 injection molding processing condition, PA6 injection molding processing condition, PBT injection molding processing condition, PC-ABS injection molding processing condition, PC-PBT injection molding processing condition, PEI injection molding processing condition, PETG injection molding processing condition, PMMA injection molding processing condition, POM injection molding processing condition, PPE injection molding processing condition, HDPE injection molding processing condition, PP injection molding processing condition, PS injection molding processing condition, PVC injection molding processing condition, SAN injection molding processing condition,
Plastic flows through the sprue bushing in a sprue, then to individual runners which take the material to the gates - the entry point of the material to the individual cavities.
East West is a global manufacturing services company focused on the realization of products, from design through distribution. As specialists in onshore, nearshore and offshore manufacturing, we offer a seamless path to scale and an exceptional speed-to-market strategy while driving down costs and adhering to the highest quality standards. We are one integrated family, working together to support our customers throughout the entire product lifecycle. Our vision is to make the world a better place – cleaner, safer, healthier and smarter.
Liquified plastic is pushed through the nozzle of the barrel of the molding machine. The nozzle seats against a surface on the mold called the sprue bushing and locating ring, which help center the nozzle to the mold.
Cavities are areas of the mold where the part is formed into desired shape. Molds must be balanced, so there are typically only a certain number of cavitations allowed (1,2,4,8, etc...)
Mold halves are attached to the molding platens by the clamp plates. Mold clamps use large bolts to hold them in place; other machines hold the mold onto the platen with magnets.
So you've designed a product. You've gone through the RFQ process, sharing your CAD drawings with engineers who probably made even more tweaks. The part is going to be made of plastic using the injection molding process. But you've never made a plastic injected part before. There are a lot of new words and phrases being tossed around and you don't really know what they all mean.
Copolymers may be used continuously at air temperatures up to 100 C (212 F); homopolymers have slightly higher temperature resistance. Many grades of acetal materials are available, tailored to different applications.
High crystallinity levels of acetals lead to relatively high shrinkage levels of 0.02 - 0.035 mm/mm. Differential shrinkage is observed with reinforced grades.
Plastic is injected hot and is cooled by cooling channels that allow conduction to cool the part. Working fluid is typically water, although oil can be used in high temp applications.
50 - 105 C (122 - 221 F); Higher mold temperatures are preferred for precision molding which reduce post-molding shrinkage
Filed Under: Plastic Injection Molding, Injection Molding
Cavity and core mold halves are insured to be in proper alignment during mold close by the use of guide pins (or pillars) and guide bushings (or sleeves).
An injection mold is a tool comprised of a series of parts that allows molten plastic to be formed and cooled in such a way as to create a discrete part shape.
The ejector pins are mounted in an ejector plate. The motion of the ejector plate forward allows the pins to move forward, pushing the part off the core. The ejector retaining plate holds the pins into the ejector plate.
GETTING A QUOTE WITH LK-MOULD IS FREE AND SIMPLE.
FIND MORE OF OUR SERVICES:
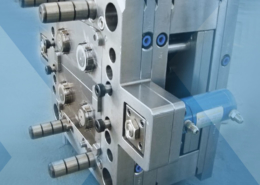
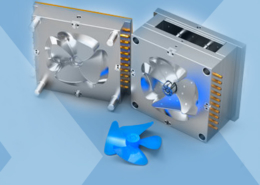
Plastic Molding

Rapid Prototyping
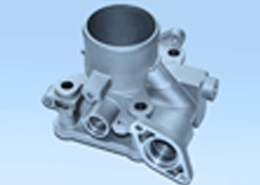
Pressure Die Casting
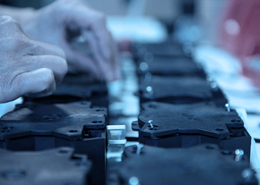
Parts Assembly
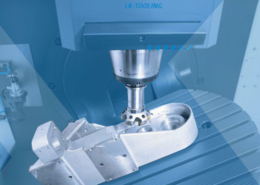