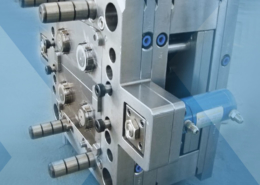
On-Site: Injection Molding 'Outside the Box' at MGS Mfg. ... - mgs injection mol
Author:gly Date: 2024-10-15
A simple case of mass production of portable ECG monitor buttons with a wide range of injection molding applications in the medical industry.
Click on the different category headings to find out more. You can also change some of your preferences. Note that blocking some types of cookies may impact your experience on our websites and the services we are able to offer.
With our precise molding methods, you can rest assured that all of your plastic automotive parts are of the best possible quality.WIT MOLD makes it a priority to ensure that all dimensions of your plastic automotive parts are as accurate as possible.
This case shows the insert molding process to produce drone remote control housing from a Chinese plastic component manufacturing factory
We pride ourselves on our ability to produce over 200 sets of molds in a year and supply them worldwide. This has earned us the reputation of being able to fulfill any order, no matter how big it is. No matter how big the order is, we are fully capable of fulfilling it.
A simple case of mass production of thermal paper printer housing with injection molding applications in the consumer electronic industry.
We fully respect if you want to refuse cookies but to avoid asking you again and again kindly allow us to store a cookie for that. You are free to opt out any time or opt in for other cookies to get a better experience. If you refuse cookies we will remove all set cookies in our domain.
Injection molding excels in crafting intricate components with stringent tolerances, setting a new standard for precision and complexity in the automotive industry.
The minimum wall thickness is also influenced by many factors, such as the strength of the mold material, injection molding process parameters, the size and position of inserts, and the design of the gate. Generally, the minimum wall thickness should be above 2mm to ensure the strength and stability of the mold.
Yes, FirstMold can provide material selection and design consultation for clients’ PC injection molding projects. We have extensive experience and expertise, allowing us to offer customized solutions that meet diverse client needs and challenges.
WIT MOLD serves automotive and parts customers worldwide and over 10 years of experience allows the WIT MOLD team to provide customers with fast development times and consistent quality to ensure that new projects run well.
One of the main advantages of our injection molding technology is the very short lead times. Simply provide us with the exact specifications and dimensions of your plastic automotive parts, and we can produce your product in record time.
Thermoplastic injection molding, using materials like polypropylene, nylon, and ABS, is the go-to method in the automotive industry.
Through communication with clients, we understand the specific requirements and constraints of the projects, providing appropriate materials and design solutions to optimize product performance and appearance while reducing production costs and risks.
FirstMold offers robust post-delivery support for PC injection molded parts, including technical assistance for integration and performance issues, quality follow-up to ensure the parts meet operational standards, and replacement services for any defects. Additionally, clients receive comprehensive documentation and training on maintenance and usage, with options for part customization and optimization based on feedback and evolving needs. This ensures continuous satisfaction and performance enhancement for all products.
Cost-Effectiveness: Offers a cost-efficient solution for producing automotive components. Speedy Production: Boasts fast production rates, meeting the demands of the automotive sector. Multifunctionality: Versatile in applications, addressing a range of automotive part requirements.
Designed for producing parts from elastic materials like rubber and silicone, elastic injection molding shares similarities with thermoplastic molding but introduces exceptional shock absorption and vibration reduction.
Accuracy and Reproducibility: High precision and reproducibility are paramount in automotive manufacturing, a core reason for the industry’s preference for injection molding. Complex Shape Design: Injection molding enables the production of intricate components with a process called “screw-injection,” facilitating the creation of detailed and complex parts. Rapid and Efficient Manufacturing: The swift production process ensures that automotive manufacturers can meet their part demands efficiently. High Surface Finish Quality: Components produced through injection molding boast excellent surface finish quality, offering smooth and flawless surfaces. Color Variety: Injection molding allows for the production of parts in various textures and colors, eliminating the need for post-molding coloring processes. In summary, injection molding in the automotive industry embodies precision, versatility, and efficiency, revolutionizing the way complex automotive components are designed and manufactured.
We also use different external services like Google Webfonts, Google Maps, and external Video providers. Since these providers may collect personal data like your IP address we allow you to block them here. Please be aware that this might heavily reduce the functionality and appearance of our site. Changes will take effect once you reload the page.
WIT MOLD engineers will analyze the fill to get the best gate position for optimal flow and design the best cooling channels to ensure minimal package distortionWe have a very good We have a very good injection operator to help set the best injection parameters to avoid any wasted development time and improve the reliability of molding parameters.
FirstMold conducts thorough testing of the mechanical properties of PC injection molded products by adhering to international standards like ASTM and ISO. Tests include tensile, flexural, and impact assessments to evaluate strength, stiffness, and toughness. Additionally, hardness and thermal analyses like DSC and TGA are performed to ensure the material’s performance under various conditions. Dimensional accuracy and structural integrity checks are also crucial to meet precise design specifications.
We provide you with a list of stored cookies on your computer in our domain so you can check what we stored. Due to security reasons we are not able to show or modify cookies from other domains. You can check these in your browser security settings.
Shock Absorption: Elevates the durability of automotive components through effective shock absorption. Vibration Reduction: Ensures a smoother ride and prolonged lifespan with superior vibration reduction. Cost-Effective Durability: Combines longevity with cost-effectiveness, a crucial aspect for automotive manufacturing.
The cost factors involved in PC (Polycarbonate) injection molding primarily include the cost of PC materials, the cost of manufacturing the injection molds, equipment costs, labor costs, and more. For detailed information, please refer to “Injection Molding Costs”
When making durable automotive parts, manufacturers can use reinforced composites that are stronger than ordinary resins. These are commonly used for bumpers and body work.
PS injection molding is ideal for complex and corrosive conditions across various industries. In the pharmaceutical and chlor-alkali industries, PS resists high concentrations of acids, alkalis, salts, and solvents. It’s also used for automotive instrument housings, electrical product casings, daily goods, and packaging materials due to its transparency, insulation, colorability, and shock resistance.
These cookies collect information that is used either in aggregate form to help us understand how our website is being used or how effective our marketing campaigns are, or to help us customize our website and application for you in order to enhance your experience.
Dimensional Precision: Ensures automotive parts meet stringent size tolerances consistently. High-Temperature Resilience: Resists melting or deformation at high temperatures, a key consideration for automotive manufacturers. Repeatability: Guarantees the production of identical components with every manufacturing cycle.
Over ten years of production experience, guaranteed quality, and mature technology, all to provide you with a superior product.
The testing process involves initial material verification, production of test samples under standard conditions, and comprehensive mechanical and thermal testing. FirstMold compiles detailed reports of all testing phases and maintains close communication with clients to ensure the products meet both regulatory standards and client-specific requirements, ensuring reliability and suitability for intended applications.
We may request cookies to be set on your device. We use cookies to let us know when you visit our websites, how you interact with us, to enrich your user experience, and to customize your relationship with our website.
We can design according to customer drawings or samples, independently design molds, and perfectly process complex parts from various materials.
Key practices include ensuring dimensional accuracy, optimizing wall thickness for strength and flexibility, and incorporating generous corner radii to minimize stress concentrations. The use of finite element analysis (FEA) to predict stress points and thorough prototyping to test functionality are also recommended to ensure the durability and performance of snap-fits.
WIT MOLD has always maintained high standards of control. We follow the strictest quality controls and any plastic automotive parts we distribute are tested by our dedicated team of experts. Rest assured that any product you receive from WIT MOLD will be of the best quality.
Bumper, dashboard parts, air intake grille, wing, radiator grille, trim, engine parts, water tank parts, air conditioning parts, air filter parts, various water bottles, seat parts, floor parts, roof parts, bar parts, steering wheel parts, door trim, rear view mirror and various fasteners, front and rear lights, etc.
Factory area exceeds 30,000 square meters, with production capabilities in both China and Mexico, ensuring large-scale custom PS parts production while maintaining quality.
FirstMold's custom hair trimmer manufacturing meets stringent customer requirements for appearance and performance. This is a case.
FirstMold has repeatedly fulfilled the demand for precision PS injection molded parts, such as high-end automotive lights and precision medical components. Our designers excel in precision PS mold design, supported by mold flow analysis, ensuring adequate quality assurance.
Injection molding stands as a cornerstone in modern manufacturing, especially in the automotive sector. Its overarching advantages redefine how complex-shaped parts with strict tolerances and exceptional surface finish are produced.
FirstMold’s professional team will design and manufacture the mold according to client needs and product characteristics, ensuring the mold wall thickness meets production requirements while maintaining the mold’s stability and lifespan.
PVC is one of the most widely used materials in the automotive industry. Because of its chemical resistance, it is used for components such as instrument panels and cable insulation.
Because these cookies are strictly necessary to deliver the website, refusing them will have impact how our site functions. You always can block or delete cookies by changing your browser settings and force blocking all cookies on this website. But this will always prompt you to accept/refuse cookies when revisiting our site.
This material is a perfect replacement for glass because it is both transparent and very resistant to breakage. They are perfect for interior screen and headlight cover applications.
One of the key advantages that our injection molding technology can bring to you is the rapid production of prototypes. By using 3D printers and CNC machines, we can produce your prototype automotive plastic parts in the shortest possible time.
These cookies are strictly necessary to provide you with services available through our website and to use some of its features.
FirstMold can apply PS materials to processes such as two-color injection molding and overmolding. We are proficient in molding various specifications and grades of PS materials, including HIPS, antistatic modified PS, high-temperature resistant modified PS, PS + fiberglass, PS + talc powder, and more.
The widespread use of injection molding in the automotive industry stems from its superiority over traditional manufacturing techniques.
The maximum wall thickness FirstMold can achieve in PC injection molding primarily depends on the design and manufacturing quality of the mold, as well as the performance of the PC material. Generally, the maximum wall thickness can exceed 20mm.
Due to its water resistance, this material is perfect for exterior components. It is particularly effective as a material for bumpers, cable insulation and battery covers.
The multifaceted nature of injection molding makes it a versatile solution for various automotive parts. Its scalable process allows for the mass production of thousands of identical components.
This material is typically used for automotive parts such as bearings and bushings. While they are resistant to wear and chemicals, they are not resistant to liquids.
If you are interested in using some of our injection mold services, we are very capable of providing you with an instant quote. This helps streamline the process and increases the efficiency of all our transactions.
Additionally, FirstMold utilizes high-grade tooling materials and advanced simulation software to ensure the mold’s integrity and performance. Techniques like sequential valve gating and gas-assisted injection molding are also applied to precisely control material flow and cooling, ensuring high-quality production of complex parts.
This type of plastic is weather resistant and ideal for injection molding and 3D printing applications. They are commonly used for covers and instrument panels.
This flexible, spongy material is primarily used for automotive seats, but because of its flexibility, it can also be used for suspension bushings, insulation panels and gaskets.
By using injection molding for your plastic auto parts, you can rest assured that you are saving money. Countless parts can be made with just one injection mold. This means you will save on materials and production costs.
FirstMold handles undercuts and complex features in PC injection molds by employing advanced design and specialized molding techniques. Mold designs incorporate features like sliding cores and lifters to facilitate the creation of complex geometries. For intricate undercuts, mechanical components such as side-actions or hand-loaded inserts are used, which can be retracted or removed post-molding.
In the automotive industry, automotive injection molding plays a critical role in producing high-quality components. Automotive plastic injection molding is widely used to create durable and precise parts, making injection molding automotive a key process in manufacturing. Companies specializing in automotive plastic molding provide essential services for car manufacturers, with many automotive injection molding companies offering specialized solutions. The production of plastic injection molding automotive parts ensures that vehicles are built with reliable and cost-effective components. Whether it’s injection molding automotive parts or working with automotive plastic injection molding companies, the focus is on delivering excellence. Injection moulding automotive parts and injection molded plastic auto parts are essential for creating everything from small fittings to large body components. The expertise in automotive mold design and production is what drives innovation and quality in the automotive sector.
Utilizing materials such as epoxy resin and polyester, thermoset injection molding highlights precise dimensions, repeatability, and resistance to high temperatures.
GETTING A QUOTE WITH LK-MOULD IS FREE AND SIMPLE.
FIND MORE OF OUR SERVICES:
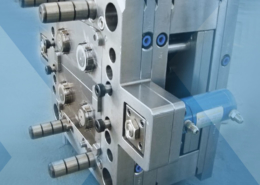
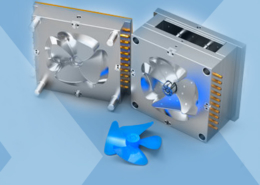
Plastic Molding

Rapid Prototyping
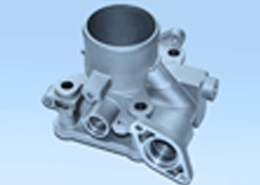
Pressure Die Casting
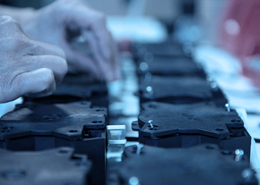
Parts Assembly
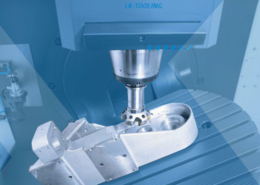