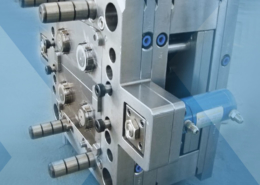
Nordon, Inc. - Plastic Injection Molding Contract Manufacturer ... - plastic inj
Author:gly Date: 2024-10-15
Injection moulding machine for PET preforms. HUSKY Injection Molding Machine for Preforms MODEL INDQ90PET RS 80/80 16 cavities Auxiliaries included: - Desiccant Hopper - Desiccant Dryer - Mold Dehumidifier Molds Included: - Hot Runner 16 Cavities - Cold Half PCO 1810 - 17 gram Preforms -...
However, achieving uniform shrinkage is complicated by the presence and interaction of many factors such as the orientations of the polymer molecules, temperature variations in the mould walls, compaction variations in the plastic parts (over-compacted areas and under-compacted areas, due to unbalanced flow paths), etc. Note that areas of higher compaction, such as injection gates, have a lower shrinkage since part of the compaction of the molten polymer compensates for it. In contrast, areas further away from the gate are subject to less compaction and therefore tend to have a higher shrinkage.
Traditionally, the joint angle between the two faces is used to differentiate weld lines from joint lines. A joint angle of less than 135º produces a weld line, while a joint angle of more than 135º is defined as a joint line. In general, a weld line mark disappears when the joint angle reaches between 120º and 150º. The weld lines are considered more critical than joint lines in terms of both aesthetics and mechanical properties of the joint. Translated with www.DeepL.com/Translator (free version)
Some of the practices we develop in the Moldblade Engineering Department to correct the problem of incomplete filling are:
Injection moulding machine for PET preforms. Husky LX225 P85/100 injection molding machine, year 1996 Includes: - Husky P85/100 E85 Injection Unit - Husky LX225PET Clamping Unit - Husky S/E Extraction Robot B - Sipa mold, with 12-cavity Sipa hot runner & 85g (40/48 neck) Sipa cold half (w...
Injection moulding machine for PET preforms. Used Injection Machine for PET Preforms HUSKY 500 PET 155/150 E155, year 2005 Working hours 121.924 The system includes the following: Mould Complete 144 Cavity 45.8g/28mm PCO 1881 Ecobase 1 Preform Mould (HR + Cold-Half) Cold-Half and hot ru...
Sinkage marks are depressions in the surface of the plastic injection moulded part caused in the last phase or stage of the plastic injection moulding process, during the cooling process. The thicker sections of the plastic cool at a slower rate than the others, resulting in a higher percentage of shrinkage in that local area. After the material on the outside has cooled and solidified, the material on the inside begins to cool and its shrinkage pulls the surface inwards, causing a surface depression.
Injection moulding machine for PET preforms. Used Injection Machine for PET Preforms HUSKY 500 P155/150 E155, year 2007 Working hours 100942 (May 2024) The system includes the following: Mould: Complete 144 Cavity 52.0g/28mm PCO 1810 Preform Mould (HR + Cold-Half) Cavity Plate Model: ...
A rule of thumb to avoid excessive distortions in the part due to temperature differences after injection, is that the average temperature differences in any part of the part after injection should not be greater than 15-20ºC.
The jetting defect occurs when molten polymer is pushed at speed through a small area, such as the injection nozzle or gate, to access a much larger area. The jetting defect results in mechanical weakness in the part, surface imperfections and multiple internal defects.
Weld lines and joint lines can be caused by holes or insertions in the part, the existence of multiple injection gates, or due to areas of varying wall thickness where hesitation or race-tracking occurs.
Injection moulding machine for PET preforms. Husky GL 300 P100/110 E 100 for PET preforms from 2003 Includes hopper, dryer, mould dehumidifier and mezzanine Running Hours: 95296 Chiller and mold not included Last audit January 2018 by HUSKY Auxiliaries: Handling / Robot Model FSI 200 GL...
Injection moulding machine for PET preforms. Husky injection moulding machine Hpet 230,with 32 cav. mould for 1881 PCO Shooting Pot ----------------RSE80D/80 Extruder --------------------Hyflo RS80 Maximum Cavities ----------32 Maximum Shot Size ------- 1538 cu. cm Machine...
Injection moulding machine for food and beverages caps. Husky H300 RS80/70 injection moukding machine for caps & closures Includes Piovan RPA800 Dehumidifier Working hours: 67.900 h In good condition and available immediately! ...
Moulds for Preforms. Used Cold half and robot plate for Husky injection molding machine Weight of the preform 30.4gr Neck: 26-22.12 P1 gravity II Lenght of the preform 119,20 mm Take out plate for the robot included the hotrunner is not included Mould stored Number o...
Moulds for Preforms. HUSKY Cold Half System HyPET 120 year 2016 Neck PCO 1881 Weight 22.7 g, for 350-450 CSD Model: 32 50x130 GEN 3.5 Stroke 63 mm Max Capacity: 134t Shot Counter: Around 117,000 Set of new core change for 22.28g can be purchased to an additional...
The warping or twisting of an injection-moulded plastic part is therefore due to the existence of a series of residual internal stresses in the part which are in turn generated by the differential shrinkage of the material during cooling. If the shrinkage throughout the part is uniform, the resulting part does not warp or twist, it simply shrinks uniformly and becomes smaller. Thecrystalline polymers, e.g. acetal, nylon, high density polyethylene, polyethylene terephthalate and polypropylenecause the most serious problems with shrinkage from 1 to 4%. Amorphous polymers, e.g. polystyrene, acrylic and polycarbonate are more treatable, with shrinkages of only 0.3 to 0.7%.
Injection moulding machine for food and beverages caps. Husky HyCAP400 injection moulding machine for closures Machine is in perfect working condition 400 V 50 Hz Available immediately! ...
Moulds for Preforms. Husky cold half and robot plate Weight 9.5gr Neck: 26-22.12 P3 Cycle time: 6,7 sec Take out plate included 7.066.300 shots...
Some of the actions to be taken to improve the surface finish are related to actions to increase the flow rate and temperature of the molten polymer and the mould walls. Therefore, the improvement of the surface quality is achieved by measures such as:
Injection moulding machine for food and beverages caps. Husky H225 RS55/50 injection molding machine from 2002 Running hours: 155.000 It was used for production of caps and closures Machine in working condition ...
The burr is a defect that occurs when part of the molten polymer flows through the existing gaps in the injection mould such as parting plane, aeration zones, ejectors, etc. Burring occurs for the following reasons:
The dimensional shrinkage of parts is inherent to the injection moulding process. Shrinkage occurs because the density of the polymer varies from processing temperature to ambient temperature (see, for example, the specific volume of a semi-crystalline polymer in Figure 5.46 – PVT curve). During the stages of the injection moulding process, cooling shrinkage produces a series of internal stresses in the part. These residual stresses act on the part with similar effects as possible externally applied stresses. If the residual stresses induced during moulding are high enough, the part after ejection from the mould may warp / twist or warp, resulting in defective parts.
Injection moulding machine for PET preforms. Husky Hypet 90 RS65/65 for PET preforms from 2010 Includes: Hopper Not currently in production, available immediately and in excellent condition!...
Injection moulding machine for PET preforms. Husky XL300 PET injection molding machine for PET preforms, year 1990 Includes: - Husky extraction robot - MPET injection molding mold, with 48-cavity MPET hot runner and 2 MPET cold halves: · 13,8g (29/25 neck) with conversion kit to 15...
Occasionally, the use of high compaction pressures causes acceptable sink marks by reducing volumetric shrinkage although these cannot be completely eliminated. This is because the volumetric change of plastic from melt to solid is about 25% and the compressibility of plastics at typical injection moulding pressure is only 15%, which means that it is impossible to compact the molten plastic sufficiently to compensate for cooling shrinkage.
Moulds for Preforms. HUSKY Cold Half System HyPET 120 year 2017 Neck 3025 Weight 17g, for 500-600ml water bottle Model: 32 50x130 GEN 3.5 Stroke 60 mm Max Capacity: 88t Rec. Capacity 85t Complete refurbishment done by HUSKY in 2017 Perfect condition and availa...
Injection moulding machine for food and beverages caps. HUSKY Injection moulding system for closures H800 RS115/100 from 2011 For caps 2,90g. PCO1810 with a contract cycle of 6.5 seconds The line is included: - Hot channel controller for mold - CapCooler, storage bin, orientator - Intravis video ins...
Injection moulding machine for PET preforms. Complete injection molding system for production of PET preforms HUSKY GL300PET P100/110 E120, Constructon year 2003 Injection Unit: P100/110 E120, Clamping Unit: GL300PET, Dryer:Plastic System DR220HT Mold Dehumidifier Plastic System DSH1800 ...
Injection moulding machine for covers. 300 Ton Husky Injection Molding Machine Manufacturer: HUSKY Model: G300 GEN RS85/70 Year:1999 Screw stroke: 340mm Screw L/D ratio: 24.7:1 Max Injection Pressure: 29,100 PSI Injection Capacity: 1308 cm3 Tonnage: 300 Tie bar spacing: 720mm X 720mm Cl...
A weld line (also called a weld mark) is formed when two melt flow fronts travelling in opposite directions meet. In contrast, a bond line occurs if these two fronts flow parallel to each other creating a bond line.
Injection molding machine from 1000 T. Working hours of the machine: 7163 Reinforced screw. No moulds for sale Robot Husky TMA is included Year of production: 2008....
Moulds for Closures. Used cold Half for caps and closures Brand: Husky Weight: 1.75 gr Neck: 30/25 for still water Cavities: 48 cav. number of shots: 239.816 HotRunner not available ...
Injection moulding machine for PET preforms. Husky HyPET300 P100/120 E140 Construction year 2007 Supplied auxiliary equipment: Dryer/dehumidifier and T-conveyor belt Working with a mould 72 cavities 50x140 18.5g PCO1810 Hot runner available at extra price Removal robot Eisbär Resin dryer ...
Injection moulding machine for PET preforms. Used injection molding machine for PET Preforms Brand: Husky Model: HyPET 300 4.0 P100/110 EE120 Year: 2017 Working hours (May 2024): 37.804 Auxiliaries included: Hot Runner 72 cavities Dryer Plastic Systems DR824.1HT Hopper loader Plast...
Trapped air will result in voids and bubbles within the moulded plastic part, incomplete filling or surface defects such as stains or burn marks.
A poor finish can be caused by the formation of wrinkles or waves at the edges of the part or in the last filling areas during injection moulding.
Injection moulding machine for PET preforms. Injection molding system HUSKY HyPET 300PET P100/120 E140 for PET preforms . Includes: Dry Pack cabinet with integrated climate control of mold area EISBAR, from 2007, Power:147 kW Dry Pack Hopper EISBAR model:H5.5 from 2007 Blower KAESER model:BB...
Moulds for Preforms. HUSKY Cold Half System year 2017 Neck 38 mm Weight 76 g Model: 16 63.5 x 160 Gen 3.5 Stroke 114 mm Max Capacity: 104 t Used in a HyPET 120 In perfect condition and available immediately...
Injection moulding machine for PET preforms. Complete system of Husky Hypet 225 injection moulding machine for preforms Included Husky Hot Runner Machine working hours: 53.000 h Cycle time: 17,6 second (Husky recommendation) Auxiliaries: - Resin Hopper, Plastics Sytems H6000 - Resin Dryer, ...
Moulds for Closures. Husky Hot runner from 2008 Rouxel watercap cold half with the slitting machine Taiwan hwa long without the thermocontroller PMS Mold Master Mold is working condition Neck 30/25 2gr 16 cavities Mold runs at 6,5 sec Dimensions of the mold: 885 x 380 ...
Incomplete filling occurs when a one injection moulded part is missing material to correctly generate its geometry. This occurs when the molten polymer cannot fill the entire cavity (or cavities) in the Injection mould, usually the thinner sections where the polymer melt cools before completely filling the mould. Any factor that increases the flow front resistance of the polymer melt can result in incomplete filling. Some of these factors are:
Injection moulding machine for PET preforms. Used Injection Machine for PET Preforms HUSKY 500 P155/150 E155, year 2005 Working hours 126000 The system includes the following: Mould Complete 144 Cavity 21.2g/28mm PCO 1881 Ecobase 1 Preform Mould (HR + Cold-Half) Extraction Robot Resin ...
The formation of wrinkles or waves is due to the fact that a part of the flow front cools rapidly on the mould walls producing a fold on the flow front itself. Themain factors influencing the formation of these wrinkles are the flow velocity, the temperature of the mould walls, and the temperature of the molten polymer, among others.
If welding or joining lines cannot be avoided, a good practice is to ensure that they are generated in low visibility or mechanically non-critical areas. This is often done by modifying the plastic injection gate, modifying the flow fronts and the areas where the weld/joint lines occur. Another practice is to try to achieve a good joint between the two fluxes so that the mechanical weakness that occurs is not excessive. To do this, the aim is for the junction of the two flux fronts to take place at the highest possible temperature and pressure, so that they are not far from the inlet port. Translated with www.DeepL.com/Translator (free version)
Injection moulding machine for PET preforms. Complete injection molding system for production of PET preforms HUSKY GL300PET P100/110 E120 Constructon year 2002 Includes: Hopper & loader Piovan Dehumidificator Piovan RPA1200 Humidifier Piovan DS528 Drier Piovan I5000IX Soft drop MB year 2...
The following recommendations can be used to reduce the impact of weld lines and parting lines on injection moulded parts.
Injection moulding machine for PET preforms. Complete HUSKY injection moulding system for preforms from 2010 Model: HyPET300 P100/110 E100, 72 cavities Working hours : 65.000 hours The line includes the following ancilliaries and equipment: - Robot - Resin hopper Plastic System - Resin dry...
The locations of the air leakage areas in the moulds are located in the areas that are filled at the end of the injection cycle or phase. A common cause of the trapped air defect is an insufficient size of the mould vents. Another common cause is when racetracking occurs (tendency of the polymer melt to flow preferentially in thicker sections leaving thinner areas with trapped air). Translated with www.DeepL.com/Translator (free version)
Injection moulding machine for food and beverages caps. Husky injection molding machine for closures Model: Hycap 225 from year 2015 Includes Husky 48 cavity mold 29/25, weight 1.25g Output: 1.5 million closures/day Working hours: 31.000 Available immediately! ...
The trapped air defect appears when a certain amount of air cannot escape out of the mould during injection, a small area without material appeared in the injected part. In a correct Injection mould design, at each injection, air is exhausted through mould vents, mould inserts or even ejectors, which also act as vents.
– Reduce the injection speed. High plastic injection speeds can cause jetting, which causes trapped air to appear right at the inlet gate. Reducing the injection speed will give the displaced air at the gate enough time to escape through the aeration zones.
Moulds for Preforms. Husky cold halves and conversion set 1- 72 cavity for 29/25, preform weight: 25,9 gr, 50V x 120H, platform HYPET5e 2- 72 cavity for 29/25, preform weight: 12,1 gr, 50V x 120H, platform HPP5e - Core conversion set for 29/25, 10,10 gr, 72 cavity...
Moulds for Closures. Husky mold for closures PCO 1881 from 2007 Cap weight 2,3 g for highly carbonated drinks, water etc. 48 cavities Mold after service and replacement of several molding elements Available immediately...
Moulds for Preforms. Used cold Half for preform Brand: Husky Weight: 12.5 gr Neck: 29/25 for still water Cavities: 96 cav. Pitch = 50 x 140 HPP 4.0 Mould number of shots: 305.185 take out plate ( with 384 pcs of tubes )+ coolpik tubes ( 96 pucks and 288 pcs of tubes):...
GETTING A QUOTE WITH LK-MOULD IS FREE AND SIMPLE.
FIND MORE OF OUR SERVICES:
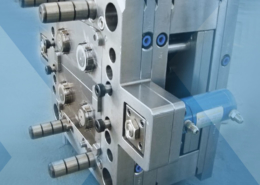
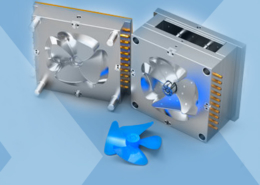
Plastic Molding

Rapid Prototyping
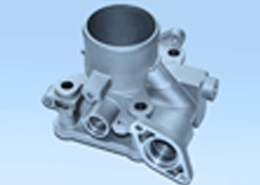
Pressure Die Casting
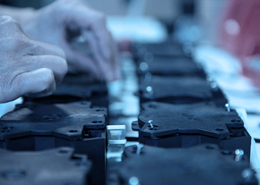
Parts Assembly
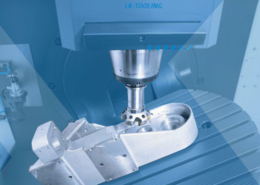