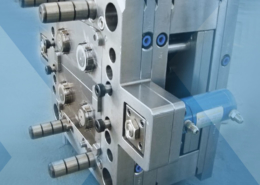
Nitrogen Gas-Assist Molding - gas injection molding
Author:gly Date: 2024-10-15
Our cleanrooms meet ISO standards, 100k (ISO Class 8) and 10k (ISO Class 7), but that’s only a starting point. Engineers and OEM part designers working on their next medical project must be aware of three core aspects of the medical micro molding process before starting their next project.
The achievement of plastic parts characterized by astoundingly tight tolerances hinges on the meticulous control of these core factors:
Within these pages, you will acquire a comprehensive understanding of this specialized molding approach, a cornerstone for crafting optics, medical instruments, electronics, and other goods necessitating unparalleled precision.
While it retains a fundamental kinship with traditional injection molding, the essence of precise injection molding lies in its specialized equipment designed to achieve unparalleled tolerances and consistency:
Critical automotive plastic parts, ranging from headlamps and dashboards to exterior trims, are meticulously produced via precise injection techniques.
Precision optics encompassing lenses, prisms, mirrors, screens, light pipes, and other optical constituents owe their existence to this methodology.
Dubbed both precise and precision injection molding, this specialized iteration of the conventional injection molding methodology establishes itself as an evolved form of its predecessor. Where conventional injection molding achieves tolerances of ±0.005 inches, precise injection molding surmounts this by attaining tolerances of ±0.001 inches, or even tighter margins.
From inhalers to surgical implements, the flawless, dependable plastic components vital to medical devices find their genesis in precise injection molding.
Precise injection molding constitutes an advanced manufacturing technique, facilitating cost-effective mass production of remarkably intricate plastic components. This methodology finds its zenith in industries like optics, medical, and electronics, where the demand for plastic components boasting micron-level precision and accuracy is unwavering. With the appropriate expertise and equipment, the finesse of precise injection techniques can replicate nearly any plastic component design with unparalleled precision.
In the same way we stretch what resins can do at micro levels, we also stretch what’s possible in part complexity and intricate cavity design. We’ve discovered one reason complex projects are often abandoned is because medical device designers are unaware their microscopic molding requirements are possible. This reason alone is why it’s best to bring our DFM team in as your advisor as early as possible.
Several compelling factors underscore manufacturers’ inclination towards adopting precise injection molding instead of the conventional approach:
This comprehensive guide delves into the depths of precise injection molding, providing a thorough exploration of its mechanics, pivotal advantages, employed equipment, design considerations, and more.
Precision plastic enclosures, connectors, insulators, and other elements tailored to meet the exacting tolerances of electronics materialize through this technique.
As parts become smaller, requiring half-micron or micron tolerances, gate and ejection pin features take up a considerable percentage of part geometry-much more than in a small injection molded component. As designers consider the medical micro molding process they need to keep in mind how they will gate the part for molding and also how they will extract it from the mold.
Industries such as optics, medical devices, electronics, and automotive stand as fervent patrons of precise injection molding, leaning on its capability to yield plastic components of unparalleled accuracy.
Medical micro molding is a highly specialized niche in the plastic injection molding industry. Medical devices from leading OEMs depend on micro-injection molded components as the miniaturize their technology, providing critical patient care in and outside the body. Micro-molding denotes plastic injection molded components with micron-sized features and extremely tight tolerances.
This exceptional level of precision unlocks the ability to produce plastic components of extraordinary complexity, boasting precision-fit assemblies, optical-grade surfaces, and microscopically detailed features.
Accumold’s primary focus since our inception over 35 years ago has been molding small components with very tight tolerances. That’s all we do. In that time, we have learned new tooling and processing techniques to make medical micro molding and micro parts possible.
The biggest misconception about micro molding is the assumption it’s simply a smaller version of injection molding. The process is completely different which is why many injection molders have difficulty getting into true micro molding with micron tolerances.
Precise injection molding stands as a pivotal method in the realm of manufacturing, facilitating the creation of plastic components characterized by remarkably stringent tolerances, intricate geometries, and precise details.
We have a very large team with decades of experience molding microscopic challenging parts. All of our tooling and automation is designed, built, and maintained in-house 24/7 and our DFM engineers are ready to help on even your most challenging medical micro molding component.
Medical device components require process validation that typically far exceeds the requirements of other industries because of strict regulatory oversight. This strict process, coupled with the very tight tolerances required for these components, can make for a very challenging molding process. This is why a specialist such as Accumold is needed.
Our medical ultra-thin and ultra-small micro molding process allows part designers and OEMs to stretch the generally accepted standards for wall thickness and part size. Our DFM engineers routinely mold components that aren’t possible according to resin supplier specifications. We often hear “oh, I didn’t know you could do that with plastic.”
This intricate procedure allows for the production of intricate components that would be otherwise unattainable through traditional injection molding techniques.
GETTING A QUOTE WITH LK-MOULD IS FREE AND SIMPLE.
FIND MORE OF OUR SERVICES:
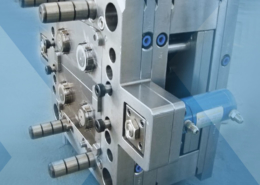
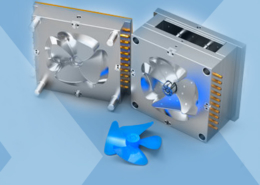
Plastic Molding

Rapid Prototyping
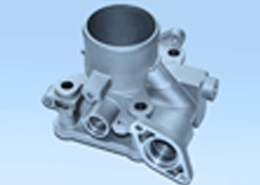
Pressure Die Casting
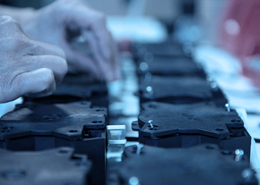
Parts Assembly
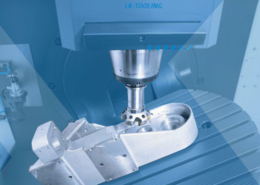