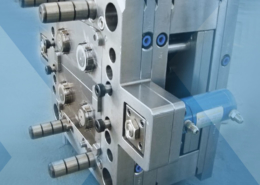
Moxietec Plastic Injection Molding - Moxietec - foam injection molding companies
Author:gly Date: 2024-10-15
Below you’ll find the physical, mechanical, and molding properties of some POM trade names. The only homopolymer listed is Delrin 100, and the other POM plastics are acetal copolymers.
By signing up, you agree to our Terms of Use and Privacy Policy. We may use the info you submit to contact you and use data from third parties to personalize your experience.
Accelerate development with instant quotes, expert DFM, and automated production updates.
POM does not readily absorb moisture and has an absorption rate of only 0.2 to 0.5%. However, it’s often recommended to dry POM resin prior to processing, typically for 3 to 4 hours. The exact drying temperature depends on the POM grade.
Proper modeling is important because POM is prone to shrinkage rates of 2 to 3.5%. Most shrinkage occurs while the part is still within the mold during the cooling stage, but a small amount of shrinkage still occurs after ejection, especially for Delrin®. This homopolymer POM variant has higher shrinkage rates than copolymer acetals.
Thanks to this automation, injection molders can optimize machine operating times, reduce energy consumption, and increase overall production efficiency. Additionally, process automation enables companies to continuously monitor their production processes and make immediate adjustments where needed, resulting in fewer errors and waste.
If POM is heated past its decomposition temperature, this engineering thermoplastic can break down into corrosive by-products that damage the injection mold. Therefore, it’s important to keep the temperature of molten POM below 210°C. In addition to the proper temperature, molders need to use a short heating cycle. As the temperature increases, the recommended residence time decreases. For best results, maintain mold temperatures between 60 to 100 °C.
If you are serious about contributing to a greener future in the automotive sector, choosing an injection molder who shares these values is indispensable. Contact us for a consultation or for more information on how we can help you achieve your sustainability goals.
Injection molded POM can withstand continuous service temperatures up to 105°C. Homopolymer POM has higher instantaneous heat resistance and copolymer POM has a better long-term thermal resistance. POM plastic is flammable, however, and it won’t self-extinguish once it’s ignited.
Lowering the overall weight of a vehicle is a direct way to improve fuel efficiency and hence sustainability. With plastic injection molding, light yet durable components can be produced that can replace metal parts.
Injection molded POM has good resistance to creep, the tendency of a solid material to undergo slow deformation when subjected to persistent mechanical stresses. POM can also be subjected to long-term loading with minimal permanent deformation.
POM injection molding produces parts made of polyoxymethylene (POM), an engineering thermoplastic that includes both homopolymer and copolymer versions of acetal. Homopolymer acetal has a highly ordered crystalline structure for increased strength, but can be difficult to process because of its precise melt temperature. Copolymer acetal has a wider range of processing temperatures, but is mechanically weaker because it only has regions of crystallinity.
By signing up, you agree to our Terms of Use and Privacy Policy. We may use the info you submit to contact you and use data from third parties to personalize your experience.
Although POM has a relatively high shrinkage rate during injection molding, this plastic provides excellent dimensional stability once parts have cooled. This enables injection molded POM to retain its form and maintain its tolerances in demanding applications.
POM can be challenging to process, but injection molded POM parts have excellent properties such as high lubricity, mechanical strength, and fatigue resistance. When you partner with Ficiv, we provide design for manufacturing (DFM) feedback along with your injection molding quote and manufacturing guidance every step of the way. And you can rest assured that our carefully vetted network of manufacturing partners have POM injection molding experience and the skill to produce the quality parts you need, no matter how complex your design is.
Because POM plastic resists most fuels and solvents, it’s often used to mold fuel tanks and chemical storage tanks. POM can be damaged by phenols, however, and it doesn’t resist strong acids and bases.
This article examines the material properties of POM plastics, the advantages of POM injection molding, and some design guidelines and processing parameters. And if you’re working on injection-molded POM parts, you’ll find tips, tricks, and best practices in our Injection Molding Design Guide.
Ready to get started? Create your free Fictiv account and request an injection molding quote today — we make complex parts at ridiculous speeds!
By signing up, you agree to our Terms of Use and Privacy Policy. We may use the info you submit to contact you and use data from third parties to personalize your experience.
As the data above shows, POM has excellent tensile and flexural strength but a high shrink rate. The homopolymer Delrin® has the greatest tensile strength because of its highly ordered crystalline structure. Note that some POM grades can be modified with fillers to increase mechanical strength, corrosion resistance, or UV (ultraviolet light) resistance.
Another crucial element in choosing an injection molder is the availability of relevant certifications. Certifications such as ISO 14001 for environmental and quality management are a strong indication that an injection molder is serious about sustainable and efficient production. These certifications provide an additional layer of reliability and can help sift through the options when selecting an injection molder.
Firstly, modern injection molders can choose from a wide range of plastics that can be recycled after use. By using materials such as PET, PP, and HDPE, it is possible to produce components that can be melted and reused for the production of new parts at the end of their life cycle. This cyclic process reduces the need for new material and minimizes waste.
By signing up, you agree to our Terms of Use and Privacy Policy. We may use the info you submit to contact you and use data from third parties to personalize your experience.
Injection molded POM products can be made of grades that are rated as food safe in accordance with FDA, USDA, NSF, Canada AG, or 3-A Dairy material standards. Applications include injection molded plastic parts for food processing equipment.
The industrial revolution 4.0 has brought process automation to the fore as a game-changer for many sectors, including injection molding. Advanced software and robot systems allow for automated production lines that can operate with astonishing speed and precision.
By signing up, you agree to our Terms of Use and Privacy Policy. We may use the info you submit to contact you and use data from third parties to personalize your experience.
By signing up, you agree to our Terms of Use and Privacy Policy. We may use the info you submit to contact you and use data from third parties to personalize your experience.
We exist to eliminate bottlenecks in new product development by integrating the people, processes, and platform you need to source custom parts.
Nieuwe ontwikkelingen in de sector hebben de weg vrijgemaakt voor het gebruik van biobased kunststoffen of kunststoffen die zijn afgeleid van hernieuwbare bronnen. Dit vermindert de afhankelijkheid van fossiele brandstoffen en maakt de weg vrij voor een duurzamere productie.
The automotive industry is one of the most dynamic and technologically advanced sectors in the world. In addition to focusing on innovations and improvements in safety, comfort, and performance, the sector also faces increasingly stringent environmental requirements. Here, injection molding, a technique that produces plastic components, plays a crucial role. But how does an injection molder precisely contribute to sustainable production for automotive?
POM has excellent lubricity because of its low coefficient of friction, so this engineering thermoplastic is ideal for applications where there’s exposure to sliding friction. Injection molded POM also has good resistance to wear, aka the ability of a material to resist the progressive loss of surface volume due to mechanical actions (such as repeated rubbing).
By signing up, you agree to our Terms of Use and Privacy Policy. We may use the info you submit to contact you and use data from third parties to personalize your experience.
POM plastics have excellent mechanical properties for rigidity, tensile strength, and flexural strength — but homopolymer acetals have better mechanical properties. Applications for high-strength POM include conveyor belts and safety restraints.
An essential aspect of evaluating a product's sustainability is Lifecycle Analysis (LCA). This analysis assesses the total environmental impact of a product from raw material extraction to production, use, and final disposal. In the context of injection molding, an LCA can provide insight into the most efficient and sustainable materials and production methods. For companies in the automotive sector, this offers valuable data to measure and possibly improve their sustainability goals.
Injection molding is an art of precision, and this is reinforced by the technology and design of injection molds. A well-designed mold ensures that every produced part meets strict specifications, crucial in the automotive industry where even minor deviations can have significant consequences.
By signing up, you agree to our Terms of Use and Privacy Policy. We may use the info you submit to contact you and use data from third parties to personalize your experience.
In today's automotive industry, the emphasis on sustainability is omnipresent. The call for ecologically responsible production methods has led to innovations in the use of reusable and recyclable materials in injection molding.
Our trained employees ensure your parts will be delivered on time and to spec.
To successfully injection mold POM parts, molders need to maintain a medium to high injection speed and an injection pressure between 70 and 120 MPa.
Secondly, biobased plastics, made from plant-based raw materials, offer an alternative to traditional, fossil fuel-based plastics. They not only reduce the CO2 footprint but also decrease dependence on finite resources.
If you are serious about contributing to a greener future in the automotive sector, choosing an injection molder who shares these values is indispensable. Contact us for a consultation or for more information on how we can help you achieve your sustainability goals.
Sustainability in the automotive sector is more crucial than ever. The ability of injection molding to contribute to these goals—through lighter components, reusable materials, precision and efficiency, and the use of green materials—makes it an indispensable technique. Additionally, lifecycle analyses and certifications add extra weight to an injection molder’s sustainability efforts.
By signing up, you agree to our Terms of Use and Privacy Policy. We may use the info you submit to contact you and use data from third parties to personalize your experience.
Access a wide breadth of capabilities through our highly vetted network.
POM can be challenging to process because of its high-temperature sensitivity. For injection molders, there are four key considerations.
Many suppliers offer copolymer acetals but only DuPont makes the resin that is used in Delrin®, a homopolymer with exceptional properties. Delrin® plastics are graded based on strength, stiffness, viscosity, and resistance, with applications that support both plastic injection molding and CNC machining. Applications for injected molded POM parts include components that are used in automotive, fluid handling, medical, and healthcare applications.
POM has excellent fatigue resistance and can be used in applications that have multiple load/unload cycles, such as gears. Homopolymer POM (e.g., injection molded Delrin®) has greater fatigue strength than copolymer POM.
Create high quality custom mechanicals with precision and accuracy.
Advanced technologies in mold design and production minimize the risk of production errors. The result is less waste and a higher yield of usable products, meaning less material is wasted on rejected products, which is both cost-saving and environmentally friendly.
We exist to eliminate bottlenecks in new product development by integrating the people, processes, and platform you need to source custom parts.
GETTING A QUOTE WITH LK-MOULD IS FREE AND SIMPLE.
FIND MORE OF OUR SERVICES:
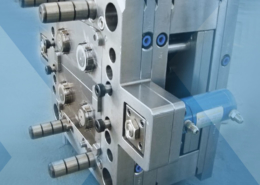
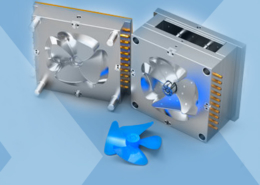
Plastic Molding

Rapid Prototyping
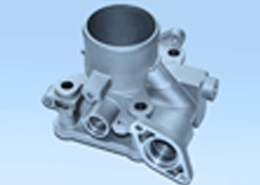
Pressure Die Casting
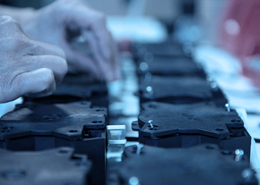
Parts Assembly
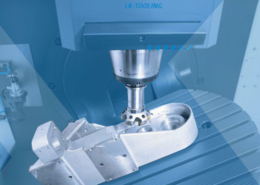