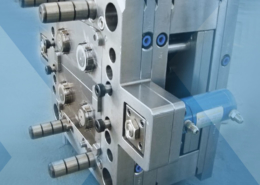
Moulding Services - plastic moulding dies
Author:gly Date: 2024-10-15
Allmould plastics is a company owned privately and controlled by a family, which was founded in 1995. It has headquarters at Orange NSW. In the course of the years, it has specialized in plastic injection molding and greatly considered the satisfaction of its customers. Allmould plastics are usually utilized by companies in the construction sectors to produce plastic parts. This company provides its customers with designs for products, prototyping of products, Polyurethane molding, warehousing and manufacturing of the products using machinery such as CNC milling. It helps in production of various equipment used in medical industries, for packaging done on food, chemicals, mining, electronics and many others. Allmould plastics Group consists of AMP Circular which helps to ensure that recycling processes are adhered to in the production process in Australia. This was formed due to the strong beliefs of the company that the environment is vital and should be kept safe.
Romar Engineering was founded in 1968 as a shop that specialized in the production of plastic tools for the automotive sector in Australia. With time and improved technology, the company has become the biggest manufacturer for consumables made of silicone in Australia in the IVF sector. Romar Engineering is best known for its proficiency in production of elastomers, silicone, plastics and every metallic product. It also takes part in micromolding, precision molding, clean room, additive manufacturing, prototyping, packaging and labeling and computer-aided engineering. The availability of vast knowledge in the above activities helps to ensure products of high quality. It is also certified by ISO 9001 and 13485. It uses recyclable plastics to ensure that the production process is environment friendly. Most sectors rely on solutions made by this company and they include mining sectors, medical sector, aerospace, aeronautical, automotive and defense sectors. Today, Romar is trying to be the first locally-owned industry in Australia to supply vertically integrated fluid and motion control for the domestic space sector.
We use the rotational molding process to create aerospace parts and high-purity containers. We also have the capability to manufacture a wide range of molded pieces in our ISO Class 7 Clean Room for high-purity applications.
B & C Plastics is also a family owned company that was founded in 1987 and helps its customers through the production process to ensure the required steps are followed. This company customizes products for its customers into their desired designs and they enter into the manufacturing process with partners based on contracts. This company has access to a large number of machinery and adequate labor force which contribute to its efficiency. B & C Plastics specializes in plastic end products and helps in the manufacture of PP, PET and HDPE plastic packaging. B & C Plastics uses modern day innovations to come up with different solutions for prototyping, CNC Machining, 3D printing and also in the assembly process. Some of the companies that B & C Plastics has worked with include Wagners, Dulux, Bradnam’s windows & doors, AMSL, Virgin Australia, Telstra and Ergon among others.
As seen above, most of the companies have been in existence for long which has helped them to acquire skills and knowledge to utilize in serving the market. Australian companies have been seen to keep the interests of their clients in mind which has made their growth significant over the years. Over the years, some of the Australian companies have gone global whereby they export their services and products. This has helped them to find ways to deal with their competitors such as China. There also consists of other companies which are going day by day and reaching more customers.
Lincoln Plastics was founded in the year 1959 and has been very efficient over the years in the provision of solutions concerning the manufacturing processes to a number of industries in Australia. This company is aware that a customer always looks for the company that has vast knowledge on the given role and provides services and end products of high quality. It guides the customer throughout the production process, from the design to the finished end product. Some of the products that are manufactured by Lincoln Plastics include materials made of plastic, synthetic resins and non vulcanizable elastomers. The company sticks to its principles which include transparency, assurance of quality and ethics which has contributed to the good relations with customers and high quality end products. Lincoln Plastics helps to produce various plastic products for industries such as automotive, construction, building, recreation and irrigation among others. This company is also certified by ISO 9001:2015 which helps to ensure end products of high quality and customer satisfaction.
A Plus Plastics is an Australian company that was founded in 1973 and specializes in coming up with designs for various products and production of products through the plastic injection molding process. Some of these products are used in various sectors such as medical sectors, engineering, automotive and agriculture among others. A Plus Plastics has proven to have the ability to make parts that weigh up to 9kgs which makes it suitable for production of parts of high complexity. It also has the ability to produce parts of a variety sizes according to the preference of the customer. This company is the number one plastics company that deals with the designing and production of non-flexible plastic containers which are used in packaging activities, supply chain and handling of materials. Over the 40 years of its existence, A plus Plastics has helped and is still helping to ensure that its customers get innovative designs, the right materials for products, the right kind of tools to use, the right prototypes and at favorable prices. It is ISO 9001 certified which makes it able to provide products of the required highest standard and best performance. This company reduces costs of labor by the use of robots in the production process and also uses recyclable plastics in favor of the environment.
C & C Plastics company was founded in 1991 and over the years it has evolved into one of the best companies involved in the custom plastic injection molding process. The company currently has 16 machines used in the process that vary between 30 to 500 tonnes. C & C Plastics specialize in services such as injection molding, assembly, insert molding, project management, custom development and also assessing and the production itself. This company is very customer centered which makes it one of the company’s strengths and also the high quality end products.
Overall, rotomolded containers and vessels are valued for their ability to maintain their structural integrity and the durability and impact resistance they can offer, alongside their chemical and environmental resistance. Rotomolding also presents cost advantages compared to other manufacturing methods for an impressive return on investment.
Each company has areas whereby it is well suited in and its specializations which makes it easy for you to know who to approach. It is crucial for you to go to the right company to ensure that the final products are of the right quality and standards. Some companies also promote other companies and their products without getting involved in the manufacturing process. To learn more about plastic injection molding, visit TDL: Plastic Injection Molding.
A mold is mounted to a multi-axis rotational molding machine. Thermoplastic resin is placed inside the mold, and in some circumstances, components such as mounting nuts or brackets are inserted at this time as well.
The mold is rotated inside of an oven. As the mold rotates, the polymer becomes molten and forms an even layer across all internal surfaces.
Rotational molding offers manufacturers a cost-effective method to produce hollow, seamless parts using thermoplastic polymers. Polymer resin is placed in a mold, which is then heated and rotated on two axes to evenly distribute the melted plastic resin through the interior of the mold. As it cools, the plastic solidifies into the desired shape, vessel, or container. The rotational molding process yields components with a high strength-to-weight ratio, which also provides chemical resistance and corrosion protection.
Plastools company has been in operation for more than 60 years since its founding in 1956. This company has the ability to come up with solutions for new products or old ones which need repair and also provide any changes needed on any kind of mold. It mainly specializes in solutions to be used in the 3D machining process. Plastools has recently extended its operations to precision machining, composite tooling and thin wall plastic tooling. Some industries such as Aerospace, automotive, building and construction and packaging use services from this company in the manufacturing of various parts.
Rotational molding is a manufacturing method that produces parts fabricated from polymer resins, which can offer excellent chemical and environmental resistance. The resistant properties of selected polymer resins are aided by the seamless interior that results from the rotational molding process.
The properties of rotationally molded containers or vessels benefit numerous applications within multiple industries, including aerospace, agriculture, automotive, mining, metallurgy, pharmaceuticals, and semiconductor fabrication.
The mold is removed from the machine and the plastic part is carefully taken out of the mold. The resulting seamless thermoplastic piece can be machined to tight tolerances, painted, or otherwise finished and assembled with other parts.
We use a variety of thermoplastic polymers in our rotational molding process, including polyethylene, polypropylene, and PVC. We also offer proprietary resins. Resin selection depends on the specific requirements of each individual project. Factors such as durability, chemical resistance, availability, and cost optimization play important roles to help determine the ideal material.
Sneddon & Kingston Plastics is a family owned company which has been operational for over six decades since it was founded in 1958. In 2014, the company joined the IML Food Packaging market. It specializes in the designing, production and distribution of products manufactured through plastic injection molding. With the improving technology, this company has enough experience and utilizes modern means to manufacture plastic end products that are of high quality and in large numbers. The company uses the 3D CAD software which enables it to have an actual picture in mind of the design. The company also produces custom plastic injection molding which helps to ensure that the given qualities and performance of the plastic products are met. Sneddon & Kingston is certified by ISO 9001 as well as HACCP. This company produces products used in the medical industry, packaging of food, automotive industries and in building and construction.
In the day-to-day manufacturing processes of industries, most industries have embraced the plastic injection molding process due to its ability to produce various parts in large numbers. This process is commenced by first forming the mold and the liquefied materials are inserted into it. The materials can be in the form of metals, elastomers, glasses, thermoplastic polymers or even confections. The final products are usually of similar features as designed by the designers through the molds. Australia is one of the countries where plastic injection molding has been embraced by many manufacturing companies. Some of the manufacturing companies include: automotive companies so as to produce various parts of cars, companies that involve the production of products that are commonly used such as toys, bottle tops, containers used for storage among others. In this article, we have discussed the top ten providers of plastic injection molding services in Australia. To know more about these companies, read on.
A seamless interior also eliminates cracks or crevices where bacteria or contaminants could accumulate, enabling rotationally molded containers and vessels to serve in high-purity manufacturing operations.
This seamless interior minimizes weak points where chemicals could potentially penetrate or react with the material. The homogeneous nature of the plastic structure enhances its resistance to various chemicals and corrosive substances.
Thin-walled, hollow parts that require tight tolerances can be manufactured using a rotational molding (rotomolding) process. Our consistent manufacturing process gives us the ability to create complex geometries in a single seamless part. We use proprietary resins and cost-effective, affordable tooling.
PlastixANZ is a private company that was founded purposely for the market in Australia and New Zealand. The aim of its formation was so as to make a shop available for the users, buyers and suppliers of plastic products more conveniently. This company has helped to promote the growth of plastic industries through creating awareness of the products to the market. For the efficiency of PlastixANZ, industries have to be transparent and give the necessary information to the company and also be ready to work with the opportunities that come from PlastixANZ. This company has embraced new technology to make the marketing process more easier, such as the use of social media to advertise products.
Formrite Group is an Australian company founded in 1957. It specializes in the designing and the manufacture of plastics used for packaging and exhibitions utilized in shelf ready trays, packagings used for medical devices, trays used to carry food, shelf management trays, freezer grades and part trays among others. The standards of their products are regulated by ISO 9001:2015 and they are also certified by HACCP in reference to the food industry. Formrite Group manufactures products to be used locally and other accepted industries across the world. The customers get to gain a great contribution by the Formrite Group in the growth of their businesses due to the provision of all services that are necessary in the production process.
GETTING A QUOTE WITH LK-MOULD IS FREE AND SIMPLE.
FIND MORE OF OUR SERVICES:
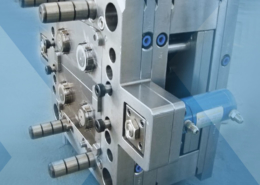
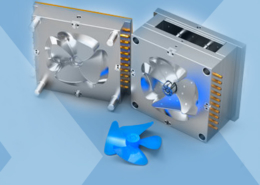
Plastic Molding

Rapid Prototyping
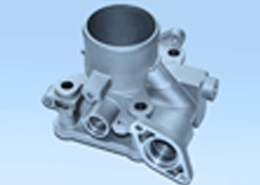
Pressure Die Casting
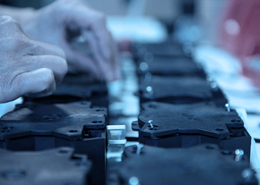
Parts Assembly
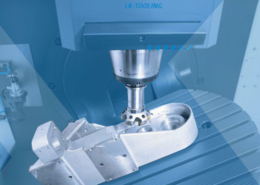