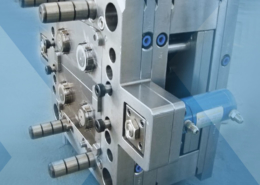
Molding Technology for DURACON® POM - pom injection molding
Author:gly Date: 2024-10-15
Recycled HDPE comes in both food-grade and non-food-grade and can be used in containers, recycling bins and outdoor decking among many other applications.
One of the most-commonly recycled plastics, HDPE is used in milk bottles and pipes to shampoo bottles and shopping bags. In the UK, the majority of recycling facilities accept HDPE. Once collected, sorted, and cleaned, HDPE is melted down and cooled into pellets to be re-used. It is more cost-effective and sustainable to recycle HDPE over creating virgin HDPE (and use large amounts of fossil fuels in the process).
· High thermal expansion· Poor UV resistance (additives are available)· Subject to stress cracking· Difficult to bond (glues)· Flammable· Can look cheap· Poor temperature capability
Keep an eye out for BEC’s new recycled range (released early 2023) which will include a recycled HDPE for use by our customers. Get in touch to find out more email hello@becgroup.com or call 01425 613131 today.
Plastic injection moulding HDPE is one of the most commonly used plastics in injection moulding. HDPE, or High-Density Polyethylene is a thermoplastic polymer renowned for being tough, cheap, and versatile. Due to these and other benefits, it is one of the most popular manufacturing plastics, accordingly over 30 million tonnes of HDPE are bought and sold around the globe every year. HDPE can be blow moulded, compression moulded, and injection moulded.
Going from a product design to full production can be costly, time consuming, and cumbersome. The MPM machines are ideally suited to produce prototypes and first article parts for approval or test marketing.
At BEC Group plastic injection moulding HDPE is used to make everything from bath toys, food containers and household goods. HDPE can also be used in the manufacture of filters – we used it for IMI Webber ‘s specialist over-moulded sintered filter. Its excellent chemical resistance properties made it the best material choice for the automotive environment. Part of a pneumatic manifold for a 4×4 suspension system, HDPE is comparatively a good materials candidate for this project and surpassed all other material options.
· Low cost· Tough· Good chemical resistance (a lot of chemicals are supplied in HDPE containers)· Widely recycled· Food grades available· Can be heat welded (gas pipes)· Doesn’t leach into food and water, containers etc· Rigidity
MPM machines are cost effective and easy to set up and get running. The single cavity V-mold and tooling inserts can be produced quickly and economically. High quality initial or low volume production runs of finished product are easily produced by MPM injection molded machines. Our application engineering team can guide you through the machine selection process to meet your Bridge Manufacturing requirements.
Many injection molded parts do not require a high volume (greater than 100,000 parts per year) injection molding machine. Higher production machines are expensive, require considerable floor space, and require expensive multi-cavity hard steel tooling. MPM machines are optimized for lower volume plastic molded parts. They are cost effective, require a small footprint, and can use single cavity low cost tooling. Low Volume injection molding machines are a good fit for smaller production orders, prototyping, bridge manufacturing, and ASTM specimen applications.
Bridge Manufacturing is the step between producing high volume finished production parts and smaller quantities that may be needed as prototypes, first articles for approval, test marketing or initial customer orders. You may need to get initial parts produced while you are waiting for a production machine to be received or available. Also, production tooling can often require considerable time to be designed and produced (16-24 weeks) delaying the time to get product to the customer or approval party.
If you need to produce parts in smaller production batches, you should consider low volume injection molding (LVIM) machines:
MPM low volume injection molding machines are ideal for bridge manufacturing, research and development, product testing, and low-volume production. A wide range of industries use our machines, including medical, automotive, consumer products, and more. With the ability to use the same plastic grade as a multi-cavity mold, engineers can test plastic blends and manufacturing optimization, marketers can test designs and colors, and your entire part or product can be optimized before full-volume production begins.
GETTING A QUOTE WITH LK-MOULD IS FREE AND SIMPLE.
FIND MORE OF OUR SERVICES:
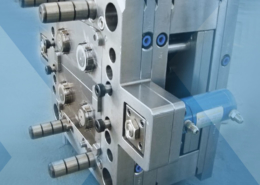
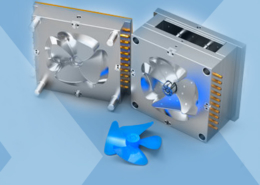
Plastic Molding

Rapid Prototyping
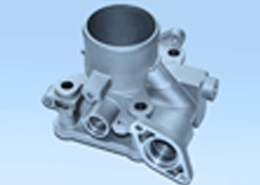
Pressure Die Casting
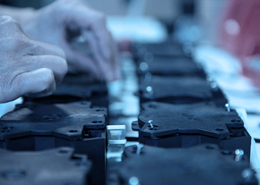
Parts Assembly
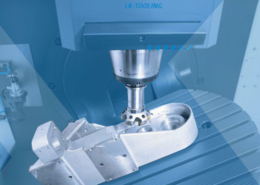