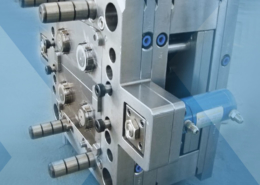
Molding Services Group, Inc. - molding services
Author:gly Date: 2024-10-15
Mechanical Strength: With a tensile strength of 27 MPa and a flexural strength of 45 MPa, HDPE 6000F offers solid mechanical performance. It's an excellent fit for creating industrial components, agricultural equipment, and structural parts that demand a blend of strength and reliability.
Injection molding flow marks are a common injection molding defect. While flow marks generally do not influence the structural integrity
Visual Inspection Tools: Advanced imaging systems and cameras can be employed to scrutinize parts for defects and irregularities, providing a more detailed and objective assessment than human visual inspection alone.
Mitigate poor plastic fluidity by selecting materials with optimal flow characteristics. Collaborate with suppliers to choose materials that align with the molding process requirements.
Injection molding short shots, the incomplete filling of mold cavities, can be due to several factors – from material viscosity to inadequate machine settings and suboptimal mold designs. The short shots not only injection molding defects; they also affect the quality, durability, and functionality of the final product.
Understanding the causes of injection molding short shots will prevent or correct short shots in injection molding can be easier on time. There are several common causes of injection molding short shots.
Ensure material compatibility with the mold design and processing conditions. Consider melt temperature and shrinkage characteristics to address issues related to material selection.
Elevated Heat Deflection: Featuring a heat deflection temperature of 100°C, HDPE 8000F is ideal for applications subjected to higher temperatures. It produces parts for automotive engine compartments, outdoor fixtures, and products with moderate heat exposure.
Enhanced Flow: HDPE 6000F's improved melt flow characteristics make it a prime choice for manufacturing intricate components with complex geometries. Its versatility applies to applications like thin-walled parts, including intricate automotive components and electronic enclosures.
Wondering how wall thickness influences injection molding? Injection Molding Wall Thickness Guideline: Maintain Uniform Wall Thickness of Injection Molded Plastic Parts
To combat short shots arising from excessively long flow channels, optimize the design to maintain uniform temperature and prevent premature cooling.
Enhance the mold’s cooling system to maintain a uniform temperature throughout the mold. This prevents localized cooling that could lead to short shots due to uneven material flow.
Ultrasonic Testing: This technique involves using ultrasonic waves to detect inconsistencies in material density. It is particularly effective in identifying air pockets or incomplete filling within the molded parts.
To achieve successful injection molding, and get high-quality molded parts, the manufacturers should optimize the injection molding process, improve mold design, adjust injection parameters, select materials with optimal flow characteristics, etc.
Balanced Strength and Flexibility: HDPE 5000S combines a commendable tensile strength of 30 MPa with a high elongation of 600%, rendering it suitable for manufacturing durable yet flexible products.
Have you ever noticed a whitening phenomenon in PVC product whitening? Some of your transparent PVC products, like shower curtains
Injection Molding Process Parameters: Improperly configured process parameters, such as fill time or cooling time, can lead to incomplete mold fillings.
Flow Channel Length: Excessive length in the flow channel can contribute to pressure loss and uneven filling, leading to short shots.
X-ray Inspection: Utilizing X-ray technology enables a thorough examination of internal structures, helping to identify any voids, air pockets, or incomplete areas within the molded parts.
Adjusting injection speed is crucial. A too-slow injection speed may result in incomplete filling, while an excessively high speed can cause turbulence and other issues. Optimize the injection speed to ensure controlled and complete mold filling, addressing concerns related to flow imbalance.
Improper Gate Design and Location: Incorrect gate design or placement can hinder the even distribution of plastic, resulting in incomplete mold fillings.
Adjust fill times to allow sufficient plastic flow. Monitor and optimize parameters to prevent premature cooling, addressing issues related to flow imbalance and incomplete filling.
Optimize gate design and placement to ensure even material distribution, mitigating issues related to improper gate design and location.
Dimensional Stability: HDPE 5000S exhibits low shrinkage (1.5%) and maintains its shape during cooling, contributing to the accurate and consistent production of precision parts.
Early detection and timely correction of short shots will contribute to the production of high-quality molded parts. Here are some methods to detect injection molding short shots.
Proper injection pressure is vital for overcoming resistance and ensuring material flow. Inadequate pressure can lead to short shots, while excessive pressure may cause overpacking. Balance injection pressure to achieve uniform mold filling.
High Molecular Weight: With an elevated molecular weight, HDPE 7000F offers improved mechanical properties and durability. It finds application in crafting industrial components, tanks, and agricultural equipment that require enduring performance under demanding conditions.
Flow Imbalance: Irregularities in the flow path can cause imbalances, resulting in some areas receiving more plastic than others.
The injection mold structure and design directly influence various aspects of the final product, including its dimensional accuracy, surface finish,
Injection molding short shots occur when the molten plastic fails to fill the mold cavity during the injection molding process, resulting in an incomplete or undersized final product. Several factors can lead to short shots, such as inadequate material volume, improper temperature control, insufficient injection pressure, or problems with the mold design, etc. Detecting and addressing short shots is crucial for maintaining product quality and preventing defects in the final manufactured items.
Dimensional Analysis: Precise dimensional measurements using calipers, gauges, or other measuring tools help ensure that each part meets the specified size and shape requirements.
Optimized Heat Deflection: With a heat deflection temperature of 85°C, HDPE 5000S is apt for applications with elevated temperatures. It produces kitchenware, automotive components, and products exposed to moderate heat sources.
To address problems with improper venting, enhance mold venting to facilitate air escape during injection. Improved venting helps prevent short shots associated with air entrapment.
Zhongde is an experienced injection molding manufacturer. Our professional team can help to find the causes and solve the injection molding short shots defect. Our goal is to improve production quality, save money, and get high-quality molded products. Welcome to contact Zhongde and find a cooperation.
Balanced Impact Resistance: An Izod impact strength of 35 J/m ensures robust resistance to impacts and shocks. This property is ideal for crafting items like safety equipment, consumer goods, and housings for power tools.
Moderate Tensile Elongation: HDPE 7000F's tensile elongation of 500% balances flexibility and strength, making it suitable for products requiring a blend of both attributes. This property is advantageous for producing hoses, tubing, and flexible containers.
Low Injection Pressure: Insufficient injection pressure may hinder the material’s ability to reach all parts of the mold cavity, resulting in short shots.
Optimize melt temperature to address issues related to material viscosity. A melt temperature that is too low can increase viscosity, hindering flow. Conversely, excessive temperatures may cause degradation. Find the optimal temperature for consistent material flow.
Wall Thickness: Uneven wall thickness in the part design can lead to variations in material flow, causing certain areas to receive insufficient plastic and resulting in short shots.
Superior Impact Strength: With an Izod impact strength of 50 J/m, HDPE 8000F ensures exceptional resilience against impacts and shocks. It finds relevance in creating challenging and durable items like tool cases, industrial bins, and protective equipment.
Improper Venting: Inadequate venting in the mold can impede the escape of air or gases, creating pockets that prevent proper material flow and causing short shots.
Low Melt Temperature: If the molten plastic temperature is too low, it may solidify before filling the entire mold cavity, causing short shots.
Enhanced Stiffness: Boasting a flexural modulus of 1300 MPa, HDPE 7000F excels in applications that demand stiffness and structural integrity. It is ideal for creating items like furniture, automotive components, and machinery parts where robustness is essential.
Improper Hold Pressure: Incorrect hold pressure settings can affect the packing phase, influencing the completeness of the mold filling.
Elevated Heat Deflection: HDPE 6000F's heat deflection temperature of 90°C makes it suitable for applications that face moderate thermal challenges. It is employed in crafting items like automotive interior parts, kitchen utensils, and electrical components that withstand elevated temperatures without deformation.
High-Density Polyethylene (HDPE) is a thermoplastic polymer known for its high strength-to-density ratio. It's produced from petroleum and exhibits excellent resistance to chemicals, impact, and moisture, making it suitable for various applications, including packaging, pipes, and injection-molded products.
Low Shrinkage and Dimensional Accuracy: HDPE 8000F's low shrinkage rate of 0.8% enhances its ability to maintain precise dimensions during cooling.
In the realm of manufacturing, injection molding stands as a pivotal process, transforming raw materials into complex and precise products. It’s famous for its efficiency and versatility. However, some common injection molding defects need to be paid attention to. Injection molding short shots are one of the common injection molding defects. The short shot can significantly impact the production process, product quality, and surface. This article delves into the injection molding short shots, exploring their causes, solutions, and effective preventive measures.
Operator Awareness: Well-trained operators play an important role in identifying short shots through visual inspection. They observe the molded parts as they are produced, looking for any signs of incomplete filling, irregularities, or visible flaws. Incomplete Features: Operators focus on specific features of the molded parts, such as corners, edges, or intricate details, where short shots are more likely to occur. Incomplete sections or variations in appearance can signal potential issues.
Diverse Industrial Applications: HDPE 7000F's combination of properties makes it versatile for various industrial applications. It is used to craft large storage containers, material handling equipment, and industrial machinery components that withstand heavy loads and harsh environments.
The temperature of the mold impacts the cooling and solidification of the plastic material. Ensure the mold temperature is set appropriately to avoid premature solidification and incomplete mold filling. A balance is needed to prevent both short shots and extended cycle times.
Material is Too Viscous / Poor Plastic Fluidity: Short shots can occur when the chosen plastic material exhibits high viscosity or poor fluidity. In such cases, the molten plastic may struggle to flow smoothly into the mold cavity, leading to incomplete fillings.
Excellent Impact Resistance: This grade's Izod impact strength of 30 J/m ensures resilience against impacts and shocks. It finds relevance in creating toys, household items, and industrial components that require impact resistance to withstand rough handling or accidental drops.
Ensure uniform wall thickness in part design to promote even material flow. This addresses issues associated with uneven wall thickness and variations in cooling rates.
High-Performance Polymer: HDPE 8000F stands out as a high-performance grade, primarily due to its excellent stress crack resistance. This property makes it an optimal choice for manufacturing chemical containers, outdoor equipment, and products exposed to challenging environments.
GETTING A QUOTE WITH LK-MOULD IS FREE AND SIMPLE.
FIND MORE OF OUR SERVICES:
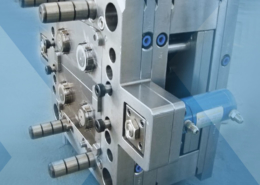
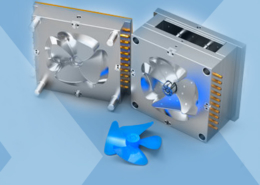
Plastic Molding

Rapid Prototyping
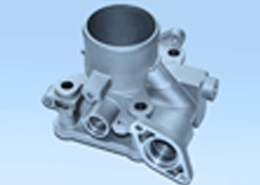
Pressure Die Casting
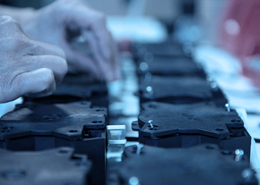
Parts Assembly
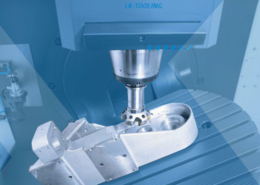