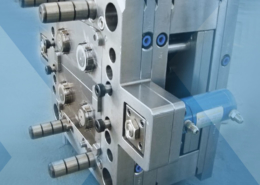
Melting Point of Plastics | The Basic Guide - melting and molding plastic
Author:gly Date: 2024-10-15
Considering the emphasis on production efficiency in two-shot molding, mold designs should aim for automatic degating whenever possible. This means that at the end of the injection molding process, excess material from the injection ports can be automatically removed from the product without manual intervention. This reduces labor costs and enhances production efficiency.
Mercury Marine is very selective in who they use as suppliers. Companies must meet the high quality standards and flexibility that Mercury Marine requires. Nicolet Plastics has consistently met these criteria.
When discussing two-shot molding technology, it’s common to compare it with overmolding. Though these two techniques seem similar in many aspects, involving multiple (two or more) injection molding processes, there are key differences between them.
Two-shot injection molding, also known as dual-shot or double injection molding, is an efficient injection molding technology that creates composite components made of two different colors or types of plastic materials within a single molding cycle.
This video shows the trial process of 2-shot molding. Because the product is small and has an undercut feature, it can’t be automatically removed from the mold. It might get stuck on the mold’s lifter, so it needs to be taken out manually.
Choosing compatible materials is crucial for a successful bond. The substrate and overmolding materials must be compatible in their molten states without adverse chemical reactions. Material suppliers often provide guidance on which material pairings achieve the best adhesion.
Mercury Marine is very selective in who they use as suppliers. Companies must meet the high quality standards and flexibility that Mercury Marine requires. Nicolet Plastics has consistently met these criteria. Nicolet Plastics and Mercury Marine engineering and purchasing departments worked together to redesign and prototype an existing part. Each prototype met all the specialized criteria, and through combined innovation Nicolet Plastics was able to move the part into production. The cost came in very low, allowing Mercury Marine to save money and use a better quality part. Nicolet Plastics adapts very quickly to change, can do custom work and provides each client with the personal attention they deserve.
The parameters during the injection molding process, such as temperature, pressure, and cooling time, need careful adjustment to suit the characteristics of both materials. Proper temperature and pressure can promote good material bonding, while the right cooling time ensures that the materials solidify without internal stress, affecting the bond strength.
We’re one of the most trustworthy plastic injection molding companies you can go to for excellent plastic parts. We’re passionate about injection molding and continuously strive to enhance our capabilities. Plus, our state-of-the-art injection molding facility is equipped with the latest injection molding machines.
Two-shot molding has the distinct advantage of producing complex, high-quality products with diverse appearances in a single molding cycle. It can reduce post-processing steps, enhance production efficiency, and lower costs. However, this technology demands high requirements for mold design and manufacturing, leading to relatively high initial investments.
We stand behind the molds we source and run. Tools are guaranteed per the quoted cycles and receive the proper maintenance to ensure long term performance.
Contact us now for all your plastic part needs, whether it’s a complex or simple design. We’ll guide you through the process – from concept to completion.
Mold design is also critical in ensuring a good combination of the two materials. The mold must precisely control the flow path of each material, ensuring that the second material forms a stable and uniform coverage over the first material’s surface.
Speed of innovation is a great advantage in a competitive global market where getting ahead means reducing the costs behind the product.
Mold Opening and Ejection: After cooling and solidification, the mold is opened, and the finished two-color product is ejected.
Reduced Production Steps and Costs: This method consolidates the injection of multiple materials into one cycle, eliminating subsequent processes and lowering both production costs and time.
The mold design and review process must be highly meticulous. Given the high cost of two-shot molds, any flaws in the design could lead to modifications in both sets of molds, thereby incurring additional costs. Therefore, the design stage of the molds must carefully consider various elements, including the design of gates and runners, the arrangement of sliders, and the layout of the cooling system. These aspects require thorough verification and validation to ensure no oversight.
Two-shot molding, a sophisticated injection molding technique that simultaneously uses two different materials or colors in the same molding process, demands highly precise molds. Ensuring the success of this process involves strict control over several aspects.
Primarily, injection molding is used to create different objects, from everyday household items to parts for cars, computers, and much more.
The precision of mold alignment is crucial. Two-shot molding employs molds that include two sets of lower molds (moveable) and two sets of upper molds (stationary), which need to rotate or shift during the molding process to align interchangeably. It is essential to ensure that both sets of molds are completely consistent in terms of outer dimensions, internal cavities, and height.
A materials overview for common plastic mold materials. Compare relative cost, mechanical properties, molding characteristics, and more.
First Injection: The process begins with the injection of the first material into one of the injection units of the molding machine, forming part of the product. Once this step is completed, the partially formed component remains fixed within the mold or is moved to another position through rotation or shifting of the mold.
I have been working with Nicolet Plastics for 13 years and have never been disappointed. The people at Nicolet Plastics have a true open door policy, and extreme flexibility. They want to be involved in the entire process of your project so they can truly understand the objectives that need to be fulfilled. In my experience, it is rare to find a plastic injection molding company that has the combination of in-house tooling and molding that they do. The quality produced is phenomenal. Nicolet Plastics is an outstanding company. They are knowledgeable, easy to work with, provide exceptional customer service, produce high quality parts, provide flexible lead times, are always competitive on price and do precision color matching work.” Nicolet Plastics is a cutting edge company that is always willing to take on a challenge.
Enhanced Product Quality: Two-shot molding can produce more durable, structurally stable products. The integration of two materials can improve overall performance, such as impact resistance and sealing properties.
Nicolet Plastics and Mercury Marine engineering and purchasing departments worked together to redesign and prototype an existing part. Each prototype met all the specialized criteria, and through combined innovation Nicolet Plastics was able to move the part into production. The cost came in very low, allowing Mercury Marine to save money and use a better quality part.
With our plastic injection molding machine, we can craft custom plastic parts for those looking to achieve specific mechanical and aesthetic features. Our goal is to help you produce high-quality plastic parts that meet your specifications and exceed your expectations.
With our differentiated and exceptional skills and expertise, we can create better plastic parts according to your needs and preferences. Our full-service custom injection molding service allows us to work with you every step of the way.
Responsive service is key to a successful project. We use a cloud-based, interactive project management solution to allow for 24/7 access to the project status.
Nicolet Plastics is an award-winning plastic injection molding engineering company that provides full-service custom injection molding to customers, including the latest 3D metal printing technology for the tooling industry. So, we’re your trusted plastic injection mold manufacturer that strives to provide customers with the results they deserve.
With our value added services, you can reduce labor and overhead, SKUs, and consolidate vendors. Spend more time doing what your company does best!
Nicolet Plastics adapts very quickly to change, can do custom work and provides each client with the personal attention they deserve.
Time-to-market is critical to being competitive. We pushed Nicolet Plastics to provide tools within a very aggressive timeline and they delivered samples in just six weeks.
We’ve pulled together these resources to answer our the most common topics and questions that come up when working on new plastic part designs.
Through the methods and mechanisms described above, two-shot molding can achieve a tight bond between the substrate and the overmolding layer, producing composite material products that are both aesthetically pleasing and high-performing. This technology is widely applied in various fields such as electronic devices, automotive parts, and medical instruments, offering more possibilities for product design and functionality.
In conclusion, while both two-shot molding and overmolding serve to create composite materials through multiple injection processes, they each offer unique benefits suited to different manufacturing needs.
Environmental Concerns: Utilizing two distinct materials complicates recycling efforts, as effectively separating these materials can be challenging. The complexity of recycling and the inability to reuse production rejects pose significant challenges for two-shot molding.
Higher Mold Costs: The complex requirements for two-shot molds result in higher costs. Designing and manufacturing these molds demand extensive experience and precision, significantly increasing initial investments compared to traditional molding techniques.
Using an injection molder to fulfill large orders provides an extensive range of advantages that can help us meet any project or demand you may have. These include:
Need to transfer your existing plastic mold or develop a new one? We share our experience and best practices that have stood the test of time.
In two-shot molding, the bonding between the substrate and the overmolding layer is achieved through chemical and physical processes, involving material selection, mold design, and processing conditions. This bonding process ensures that two different materials tightly integrate in the final product, forming a structurally intact and functionally robust composite. Here are several key factors in this bonding process:
This detailed process showcases the technical complexity and precision required in two-shot molding, allowing for the production of high-quality, multifunctional components used across various industries.
Increased Production Hourly Rates: Specialized two-shot molding machines are more expensive than standard injection molding machines. Additionally, operating these machines requires specialized skills, contributing to higher hourly rates.
I have been working with Nicolet Plastics for 13 years and have never been disappointed. The people at Nicolet Plastics have a true open door policy, and extreme flexibility.
The process of two-shot molding is outlined as follows, highlighting the intricate steps involved in creating a composite component within a single molding cycle:
Time-to-market is critical to being competitive. We pushed Nicolet Plastics to provide tools within a very aggressive timeline and they delivered samples in just six weeks.
Design Flexibility: It allows designers to combine different colors or types of plastics in one component, offering unique visual and tactile qualities.
In some cases, the substrate’s surface may undergo special treatments such as sandblasting, chemical etching, or surface activation to increase its roughness and chemical reactivity, thereby enhancing the bond strength with the overmolding layer.
Mold Rotation or Shifting: For some two-shot molding processes, the semi-finished product from the first injection needs to be transferred within the mold to a second injection position. This can be achieved by rotating or shifting the mold, depending on the design of the two-shot molding machine used.
Second Injection: After the first part has solidified and been moved to the second position, the second material is injected into the mold through another injection unit, bonding with the first part to form the final product. This step requires precise control to ensure good adhesion between the two materials.
The first project I ever worked on with Nicolet Plastics, Inc. was in the mid 80’s, and since then the partnership has only grown stronger. Nicolet is willing to try anything to produce the results the client is looking for.
Cooling and Solidification: Following the injection of the second material, the entire component cools and solidifies within the mold. This stage is critical for the quality of the product, necessitating precise control over cooling speed and time.
At the interface of the two materials in their molten state, molecular diffusion occurs, meaning molecules from one material penetrate into the other. This helps form stronger chemical bonds and physical entanglements, enhancing the adhesion between the two materials
We take on complex injection mold projects, a challenge we’re willing to take on to deliver innovative products. Doing business with us means we can help you develop a fantastic injection molded plastic design that will work with whatever project it’s intended for.
Injection molding is a manufacturing process in which Nicolet Plastics specializes in. It’s all about producing plastic parts in high quantities, performed by injecting melted materials (typically plastic) into molds. We often utilize this mass production process to manufacture hundreds or thousands of identical plastic items.
They want to be involved in the entire process of your project so they can truly understand the objectives that need to be fulfilled. In my experience, it is rare to find a plastic injection molding company that has the combination of in-house tooling and molding that they do. The quality produced is phenomenal.
This process requires a specialized two-shot injection molding machine equipped with two separate sets of screws and barrels. This technology is capable of producing components with both aesthetic appeal and functional strength, finding widespread applications in the automotive, consumer electronics, and medical equipment industries.
From the President of the company to the guys in shipping, the folks at Nicolet are host, hardworking and down to earth, some of the best people I’ve ever worked with.
Nicolet Plastics is a custom plastic injection molding manufacturer that’s focused on enhancing our clients’ success by creating superior plastic components, all while maintaining a commitment to speed, adaptability, and versatility. We collaborate with you to develop designs that optimize value. Excitingly, we've embraced Mantle 3D metal printing for rapid production tooling, bringing the future to the present!
Our clients are involved in the project, ensuring they get the desired results. Every industry has different needs and specifications, so we want our clients to know the process from start to finish.
They are on the cutting edge with tooling, equipment and design capabilities. Their design review team provides excellent input; they are creative solution-finders and are very easy to work with. NPI delivers a timely response on product and a quick turn around on tools.
Our people make a difference. For over 30 years, this is how Nicolet Plastics has achieved steady growth amidst a highly competitive landscape.
We’ve put together a basic glossary of terms to help customers better understand their project quote and molding technology options.
Nicolet Plastics is a Carbon 3D Production Partner which provides on-demand manufacturing and tool-free design flexibility and speed.
When challenged with difficult mold designs Nicolet is able to simplify the process, thereby reducing costs. Utilizing their in-house rapid prototype machine allows the toolmaker to better understand how the tool needs to be created. One quality control advantage that Nicolet provides for the customer is their storyboards, which detail the proper measurements and color specifications of each piece. Through this self-certification process, Nicolet offers customers the assurance of knowing that each piece is manufactured to exact specifications. I have come to expect that quality work will always be there. You don’t realize how good Nicolet is until you try to compare quality and price somewhere else.
The first project I ever worked on with Nicolet Plastics, Inc. was in the mid 80’s, and since then the partnership has only grown stronger. Nicolet is willing to try anything to produce the results the client is looking for. They are on the cutting edge with tooling, equipment and design capabilities. Their design review team provides excellent input; they are creative solution-finders and are very easy to work with. NPI delivers a timely response on product and a quick turn around on tools. When challenged with difficult mold designs Nicolet is able to simplify the process, thereby reducing costs. Utilizing their in-house rapid prototype machine allows the toolmaker to better understand how the tool needs to be created. One quality control advantage that Nicolet provides for the customer is their storyboards, which detail the proper measurements and color specifications of each piece. Through this self-certification process, Nicolet offers customers the assurance of knowing that each piece is manufactured to exact specifications. I have come to expect that quality work will always be there. You don’t realize how good Nicolet is until you try to compare quality and price somewhere else. From the President of the company to the guys in shipping, the folks at Nicolet are host, hardworking and down to earth, some of the best people I’ve ever worked with.
In summary, two-shot molding is an advanced injection molding technique that efficiently combines two different materials or colors in a single cycle, offering significant advantages in terms of design flexibility, product quality, and production efficiency. Despite its higher initial investment in mold design and machinery, the technology presents a compelling case for applications requiring complex, multi-material components with high precision and strength.
Two-shot molding necessitates the use of a specialized two-shot injection molding machine and precisely designed molds. The design of the mold must take into account the flow, cooling, and solidification characteristics of both materials to ensure they combine correctly within the mold. The steps are as follows:
Typically, a CMM (Coordinate Measuring Machine, a three-dimensional measuring equipment) is used in production to check the precision of the molds, preventing injection molding defects such as flash due to misalignment.
Working with us means we will answer any questions you may have about injection molding. We’re one of the most trusted injection molding companies that will guide you through the process, so you understand how we can finish the project and deliver perfect results. No matter how large your orders may be, we’re ready to work with you to create an innovative design that fits your standards.
Nicolet Plastics is an outstanding company. They are knowledgeable, easy to work with, provide exceptional customer service, produce high quality parts, provide flexible lead times, are always competitive on price and do precision color matching work.”
GETTING A QUOTE WITH LK-MOULD IS FREE AND SIMPLE.
FIND MORE OF OUR SERVICES:
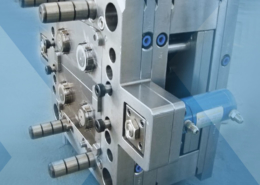
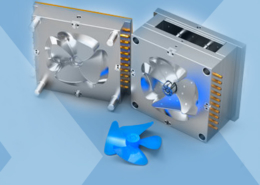
Plastic Molding

Rapid Prototyping
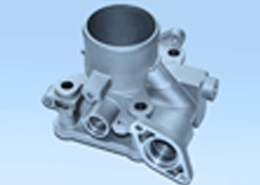
Pressure Die Casting
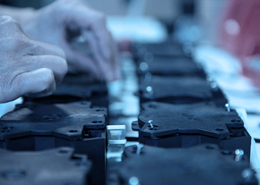
Parts Assembly
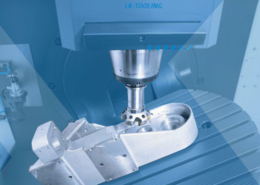