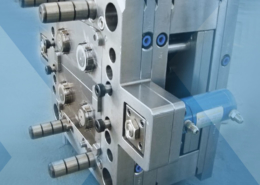
Meet our new slide injection mold - slide injection molding
Author:gly Date: 2024-10-15
Injection molding process description: mold is a tool for producing plastic products. It is composed of several groups of parts, and this combination has a forming die cavity. During injection molding, the mold is clamped on the injection molding machine, the molten plastic is injected into the molding mold cavity, cooled and shaped in the cavity, and then the upper and lower molds are separated. The products are ejected from the mold cavity and left the mold through the ejection system. Finally, the mold is closed for the next injection molding. The whole injection molding process is cyclic.
Electrical discharge machining (EDM) has become widely used in mold making. EDM is a process in which a desired shape is obtained through the use of an electrode, which is fabricated out of graphite or copper. It is then mounted in an EDM machine and positioned over the workpiece, which is submerged in a dielectric fluid.
Another advantage of the EDM process is that it allows pre-hardened molds to be shaped and eliminates the need for additional heat-treating. At times, such as with speaker grille molds, the resulting fine EDM finish serves to be the final part finish without any polishing of the mold cavity.
The electrode is then lowered to the workpiece. Then, using a controlled electrical source, the electrode is used to destroy and disperse the metal in the area opposite of the electrode. The electrode never contacts the workpiece. A spark gap of a few thousandths of an inch is always maintained between the electrode and workpiece. This process is a slower method of removing metal from a mold; however, the EDM process can produce shapes that are not possible with conventional CNC machining.
A mold is usually designed so that the molded part reliably remains on the B half of the mold when it opens. The runner and the sprue are drawn out of the A half. The molded part then falls freely when ejected from the B half.
All kinds of tools and products used in our daily production and life, ranging from the base and body shell of the machine tool to the shell of a embryo head screw, button and various household appliances, are closely related to the mold. The shape of the mold determines the shape of these products, and the processing quality and accuracy of the mold also determine the quality of these products. Because of the different materials, appearance, specifications and uses of various products, molds are divided into casting molds, forging molds, die-casting molds, stamping molds and other non plastic molds, as well as plastic molds.
In modern CNC systems, the mold design and manufacturing processes are both highly automated. The mold’s mechanical dimensions are defined using computer-aided design (CAD) software, and then translated into manufacturing instructions by computer-aided manufacturing (CAM) software. “Post processor” software then transforms these instructions into the specific commands necessary for each machine used in creating the mold. The resulting commands are then loaded into the CNC machine.
In its conventional form, standard machining requires the manual use of lathes, milling machines and drill presses. With advanced technology, CNC machining has become the predominant means of creating more complex and accurate molds, while still using standard machining methods. With CNC, computers are used to control the movement and operation of the mills, lathes, and other cutting machines.
The plastic injection mold consists of two primary components, the cavity half of the mold (A half) and the ejector half of the mold (B half). These mold halves are designed to work in conjunction as follows:
General definition of mold: in industrial production, various presses and special tools installed on the press are used to make metal or non-metallic materials into parts or products of the required shape through pressure. Such special tools are collectively referred to as molds.
In recent years, with the rapid development of plastic mold industry and the continuous improvement of strength and accuracy of general and engineering plastics, the application scope of plastic products is also expanding, such as household appliances, instruments and meters, construction equipment, automobile industry, daily hardware and many other fields. The proportion of plastic products is increasing rapidly. A reasonably designed plastic part can often replace multiple traditional metal parts. The trend of plasticization of industrial products and daily-use products is rising.
Many steel molds are designed to process well over a million parts during their lifetime. For lower volumes, pre-hardened steel molds provide a less wear-resistant and less expensive option.
Copper alloy inserts are sometimes used in areas of the mold that require fast heat removal. This can reduce cycle time and improve the aesthetic quality of the part.
A single plastic injection mold can have one cavity, producing one part at a time, to multiple cavities for extremely high-production molds (like those for bottle caps) that can have 100 plus cavities.
CS Tool Engineering ♦ P.O. Box 210-K ♦ 251 West Cherry Street ♦ Cedar Springs, MI 49319Phone (616)-696-0940 ♦ Email cste@cste.comWebsite design and hosting by Creative Technology Corp
Aluminum molds, on the other hand, can cost substantially less, but they typically are ill-suited for high-volume production or parts with narrow dimensional tolerances. Nevertheless, aluminum molds can economically produce tens of thousands to hundreds of thousands of parts, when designed and built using computer numerical control (CNC) machines or Electrical Discharge Machining (EDM) processes.
Plastic injection molds are typically constructed from hardened or pre-hardened steel, aluminum, and/or beryllium-copper alloy. Steel molds cost more, but are often preferred because of their high durability. Hardened steel molds are heat treated after machining, and they are by far superior in terms of wear resistance and lifespan.
GETTING A QUOTE WITH LK-MOULD IS FREE AND SIMPLE.
FIND MORE OF OUR SERVICES:
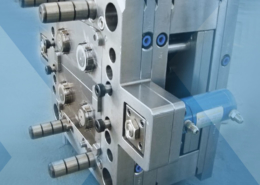
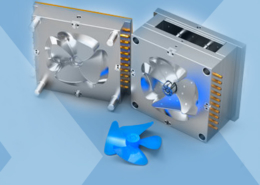
Plastic Molding

Rapid Prototyping
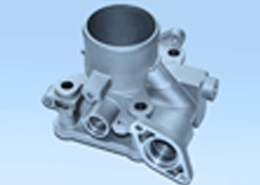
Pressure Die Casting
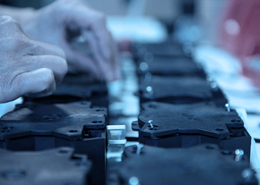
Parts Assembly
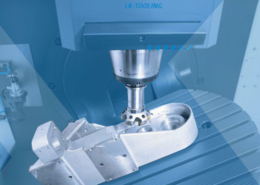