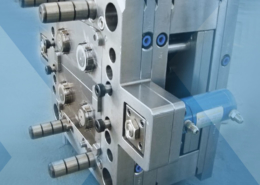
Embarking on the Journey of Injection Molding 101: Unveiling the Basics
Author:gly Date: 2024-06-08
Injection molding stands as a fundamental pillar in the world of manufacturing, offering a versatile and efficient method for producing a wide array of plastic products. This article serves as a guide to Injection Molding 101, catering to both novices and experts alike, by providing comprehensive insights into its principles, processes, and applications.
Introduction to Injection Molding 101
Welcome to Injection Molding 101, where we embark on a journey into the fascinating realm of plastic manufacturing. Whether you're a seasoned professional or a curious novice, this guide aims to unravel the complexities of injection molding, offering a deeper understanding of its mechanics, applications, and potential.
The Basics of Injection Molding
Injection molding operates on a simple yet ingenious principle: injecting molten plastic material into a mold cavity, where it cools and solidifies to form the desired shape. The process begins with the melting of plastic pellets in a heated barrel, followed by the injection of the molten material into a mold under high pressure. Once the material cools and solidifies, the mold opens, and the finished product is ejected, ready for further processing or distribution.
Injection molding boasts several advantages over traditional manufacturing methods, including high production efficiency, intricate design capabilities, and minimal material wastage. Its versatility and scalability make it the preferred choice for a wide range of industries, from automotive and aerospace to consumer electronics and medical devices.
Key Components of Injection Molding
Several components play a crucial role in the injection molding process, each contributing to its efficiency and precision. The injection unit, consisting of the barrel, screw, and nozzle, is responsible for melting and injecting the plastic material into the mold. The clamping unit holds the mold in place and applies the necessary pressure to keep it closed during injection. The mold, typically made of steel or aluminum, defines the shape and features of the final product, while the cooling system ensures proper solidification and dimensional stability.
Materials and Additives
The choice of material is paramount in injection molding, as it determines the properties and characteristics of the final product. Common materials used in injection molding include thermoplastics, thermosets, and elastomers, each offering unique advantages in terms of strength, flexibility, and durability. Additives such as fillers, reinforcements, and colorants can further enhance the properties of the material, providing additional strength, heat resistance, or aesthetic appeal.
Design Considerations and Optimization
Design plays a critical role in the success of an injection molding project, influencing everything from part quality and performance to production cost and cycle time. Design considerations such as wall thickness, draft angles, and parting lines can significantly impact the manufacturability and functionality of the final product. By leveraging advanced design tools and simulation software, engineers can optimize the design for injection molding, minimizing defects and maximizing efficiency.
Conclusion: Exploring the Boundless Possibilities of Injection Molding
In conclusion, Injection Molding 101 offers a glimpse into the intricate world of plastic manufacturing, highlighting its principles, processes, and applications. Whether it's producing intricate components for the automotive industry or mass-producing consumer goods, injection molding continues to revolutionize the way we manufacture plastic products. As we delve deeper into the realm of injection molding, the possibilities are endless, promising innovation, efficiency, and sustainability for generations to come.
GETTING A QUOTE WITH LK-MOULD IS FREE AND SIMPLE.
FIND MORE OF OUR SERVICES:
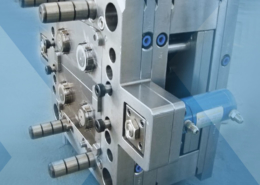
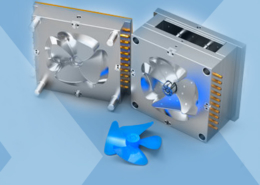
Plastic Molding

Rapid Prototyping
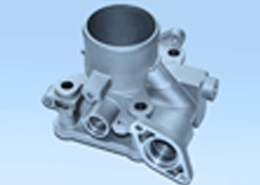
Pressure Die Casting
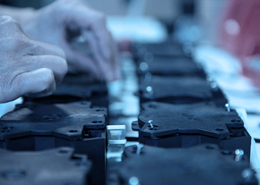
Parts Assembly
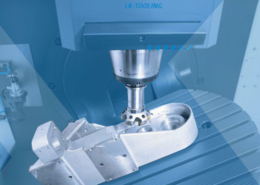