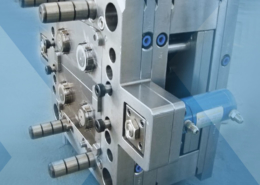
Industrial Injection Molding: Revolutionizing Manufacturing Processes
Author:gly Date: 2024-06-08
Industrial injection molding stands as a cornerstone of modern manufacturing, revolutionizing the production of various plastic components across industries. Its significance lies in its ability to efficiently and precisely manufacture large volumes of complex parts with high consistency and quality. This article delves into the intricacies of industrial injection molding, exploring its processes, applications, advancements, challenges, and future prospects.
The Essence of Industrial Injection Molding
Industrial injection molding encompasses the process of injecting molten material, typically thermoplastic or thermosetting polymers, into a mold cavity. Once the material cools and solidifies, the mold opens, releasing the formed part. This process is characterized by its speed, scalability, and versatility, making it indispensable in diverse sectors ranging from automotive and aerospace to electronics and consumer goods.
Historical Evolution
The roots of injection molding trace back to the late 19th century, but it wasn't until the mid-20th century that it gained widespread industrial application. With advancements in materials science, machinery, and automation, injection molding emerged as a dominant manufacturing technique, offering unparalleled efficiency and cost-effectiveness.
Process Overview
Industrial injection molding involves several key steps, including material preparation, mold setup, injection, cooling, ejection, and finishing. Each stage demands precision control of parameters such as temperature, pressure, and cooling rate to ensure optimal part quality and consistency.
Applications Across Industries
Automotive
In the automotive sector, industrial injection molding finds extensive use in producing interior and exterior components, ranging from dashboards and bumpers to door panels and lighting systems. Its ability to create lightweight, durable parts with complex geometries contributes to enhanced vehicle performance and aesthetics.
Electronics
In electronics manufacturing, injection molding facilitates the production of housings, connectors, and enclosures for various devices. The process ensures tight tolerances, insulation properties, and protection against environmental factors, crucial for the reliability and functionality of electronic products.
Medical Devices
The medical industry relies on industrial injection molding for manufacturing sterile and biocompatible components such as syringes, vials, and implants. Strict regulatory standards necessitate precision molding techniques to ensure product consistency, safety, and reliability in healthcare applications.
Advancements and Innovations
Industry 4.0 Integration
The integration of industrial injection molding with Industry 4.0 technologies, including IoT sensors, AI-driven analytics, and robotics, is transforming manufacturing operations. Real-time monitoring and predictive maintenance optimize production efficiency, minimize downtime, and enhance quality control.
Material Innovations
Ongoing research in polymer science continues to yield new materials tailored for specific applications, offering improved performance, sustainability, and cost-effectiveness. Biodegradable polymers, high-performance composites, and recycled materials expand the possibilities of industrial injection molding while addressing environmental concerns.
Additive Manufacturing Synergy
The synergy between industrial injection molding and additive manufacturing technologies, such as 3D printing, enables rapid prototyping, tooling fabrication, and on-demand production. Hybrid approaches combine the strengths of both processes, accelerating product development cycles and reducing time-to-market.
Challenges and Future Outlook
Sustainability Concerns
Despite its efficiency, industrial injection molding faces scrutiny regarding its environmental impact, particularly concerning plastic waste and energy consumption. Innovations in recycling technologies, circular economy initiatives, and bio-based materials offer avenues for mitigating these concerns and promoting sustainable manufacturing practices.
Supply Chain Disruptions
Global supply chain disruptions, exacerbated by events like the COVID-19 pandemic, underscore the need for resilience and agility in manufacturing operations. Strategies such as regionalization, digital supply networks, and inventory optimization mitigate risks and enhance the adaptability of industrial injection molding processes.
Customization and Personalization
Consumer preferences for customized products drive demand for flexible manufacturing solutions. Industrial injection molding must adapt to accommodate smaller production runs, faster changeovers, and personalized product configurations, necessitating advancements in automation, digital design, and flexible tooling technologies.
Conclusion and Future Directions
Industrial injection molding stands at the forefront of modern manufacturing, offering unparalleled efficiency, precision, and versatility. As technology continues to evolve, addressing sustainability concerns, enhancing material innovations, and embracing digitalization will shape the future landscape of injection molding. By leveraging advancements in Industry 4.0, materials science, and supply chain management, manufacturers can navigate challenges and unlock new opportunities for innovation and growth in the realm of industrial injection molding.
GETTING A QUOTE WITH LK-MOULD IS FREE AND SIMPLE.
FIND MORE OF OUR SERVICES:
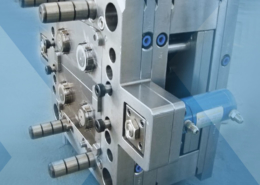
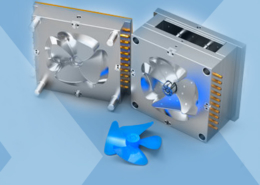
Plastic Molding

Rapid Prototyping
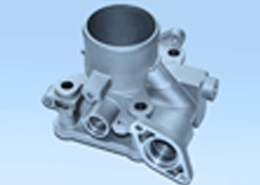
Pressure Die Casting
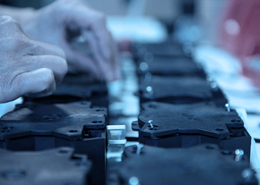
Parts Assembly
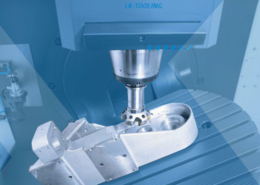