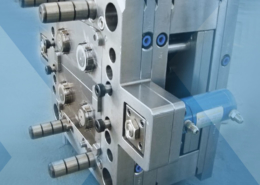
Exploring the Potential of Gas Injection Molding
Author:gly Date: 2024-06-08
Gas injection molding (GIM) stands as a cutting-edge manufacturing technique that offers unparalleled advantages in producing complex, lightweight, and high-performance plastic components. With its ability to enhance part quality, reduce cycle times, and optimize material usage, gas injection molding has garnered significant interest across industries. In this comprehensive exploration, we delve into the intricacies of gas injection molding, examining its techniques, applications, benefits, and future prospects.
Unveiling the Essence of Gas Injection Molding
Gas injection molding is an advanced variation of conventional injection molding, wherein a gas (typically nitrogen) is injected into the polymer melt within the mold cavity to displace material and form hollow sections or create a gas barrier. This process enables the production of lightweight, thick-walled parts with improved surface finish, reduced sink marks, and enhanced mechanical properties.
Technological Innovations
The evolution of gas injection molding technology has been driven by advancements in equipment, process control, and simulation software. From improved gas injection systems and pressure regulators to sophisticated mold designs and predictive modeling tools, manufacturers have access to a wide array of resources to optimize the gas injection molding process and achieve desired outcomes.
Gas Injection Systems
Modern gas injection systems feature precise control over gas pressure, flow rate, and distribution, allowing for fine-tuning of the gas-assisted molding process to meet specific part requirements. Integrated sensors and feedback mechanisms enable real-time monitoring and adjustment, ensuring consistent part quality and production efficiency.
Mold Design and Simulation
The use of advanced mold design software and simulation tools has revolutionized the way engineers conceptualize, analyze, and optimize gas injection molding processes. Virtual prototyping and mold flow analysis enable predictive modeling of gas flow behavior, part filling patterns, and gas penetration depth, facilitating design iterations and process optimization prior to actual production.
Applications Across Industries
Gas injection molding finds diverse applications across industries where lightweighting, structural integrity, and cost efficiency are paramount. From automotive and aerospace to consumer electronics and medical devices, the versatility and performance of gas-assisted molding make it a preferred choice for producing a wide range of components with complex geometries and functional requirements.
Automotive Industry
In the automotive sector, gas injection molding is utilized to produce structural components such as instrument panels, door panels, and seat frames, as well as aesthetic elements such as grilles, spoilers, and trim pieces. By incorporating gas-assisted molding techniques, manufacturers can achieve significant weight reduction, material savings, and design flexibility while maintaining structural integrity and crashworthiness.
Consumer Electronics
Gas injection molding plays a crucial role in the production of consumer electronics, where lightweight, durable, and aesthetically pleasing designs are essential. From laptop casings and smartphone housings to appliance components and wearable devices, gas-assisted molding enables manufacturers to achieve thin-walled structures, intricate features, and superior surface finish, enhancing product performance and user experience.
Medical Devices
In the medical device industry, gas injection molding is employed to manufacture components such as surgical instruments, drug delivery devices, and diagnostic equipment. The ability to produce complex, hollow parts with controlled wall thickness and smooth surfaces is particularly advantageous for applications requiring sterilizability, biocompatibility, and ergonomic design.
Advantages of Gas Injection Molding
Gas injection molding offers several advantages over conventional injection molding techniques, making it an attractive option for manufacturers seeking to optimize part quality, production efficiency, and cost-effectiveness.
Enhanced Part Quality
Gas-assisted molding allows for the production of parts with uniform wall thickness, reduced warpage, and improved dimensional stability. By controlling the distribution and penetration of the gas within the mold cavity, manufacturers can minimize sink marks, voids, and surface defects, resulting in higher-quality finished products with tighter tolerances and superior aesthetics.
Reduced Cycle Times
Gas injection molding can significantly reduce cycle times by accelerating the cooling and solidification of the polymer melt. By strategically introducing gas into the mold cavity during the injection phase, manufacturers can promote rapid material solidification, shorten cycle times, and increase production throughput without compromising part quality or integrity.
Material Savings
Gas-assisted molding enables material savings by reducing the overall volume of plastic resin required to fill the mold cavity. By displacing material with gas and creating hollow sections or gas barriers within the part, manufacturers can achieve substantial weight reduction while maintaining structural integrity and performance. This results in lower material costs, reduced environmental impact, and enhanced sustainability.
Challenges and Future Directions
Despite its numerous advantages, gas injection molding is not without its challenges and opportunities for improvement. Issues such as process complexity, equipment costs, and material compatibility continue to pose obstacles to widespread adoption. However, ongoing research and development efforts are focused on addressing these challenges and advancing the capabilities of gas-assisted molding technology.
Process Optimization
Further research is needed to optimize gas injection molding processes and parameters for specific applications, materials, and part geometries. By refining gas injection strategies, mold designs, and processing conditions, manufacturers can maximize part quality, production efficiency, and cost-effectiveness, unlocking new opportunities for innovation and market growth.
Material Innovation
Advancements in materials science and polymer chemistry are driving the development of novel resins and additives tailored for gas injection molding applications. By formulating materials with enhanced flow properties, thermal stability, and gas permeability, researchers aim to expand the range of materials suitable for gas-assisted molding, enabling new possibilities for lightweighting, design optimization, and functional integration.
Conclusion
In conclusion, gas injection molding represents a paradigm shift in the field of plastic molding, offering unparalleled opportunities for innovation, efficiency, and sustainability. By harnessing the power of gas to optimize part quality, reduce cycle times, and minimize material usage, manufacturers can achieve significant cost savings, environmental benefits, and competitive advantages in the global marketplace. As we continue to push the boundaries of technology and explore new frontiers in materials science, the future of gas injection molding holds immense promise and potential for revolutionizing the way we design, manufacture, and consume plastic products.
GETTING A QUOTE WITH LK-MOULD IS FREE AND SIMPLE.
FIND MORE OF OUR SERVICES:
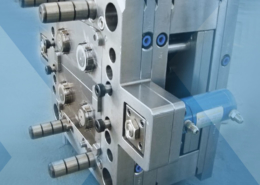
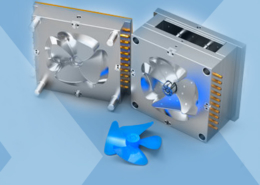
Plastic Molding

Rapid Prototyping
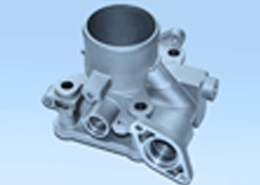
Pressure Die Casting
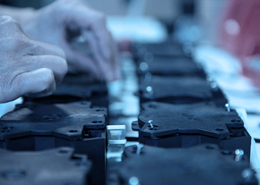
Parts Assembly
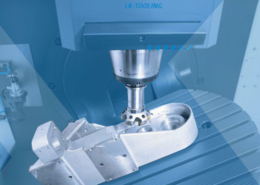