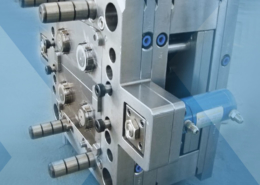
Exploring Extrusion and Injection Moulding: Revolutionizing Manufacturing
Author:gly Date: 2024-06-08
Introduction
Extrusion and injection moulding stand as two cornerstone processes in modern manufacturing, driving efficiency, precision, and versatility across various industries. As we delve into these methodologies, we embark on a journey through the intricate mechanisms that shape raw materials into finished products with unparalleled intricacy and accuracy.
Understanding Extrusion
Extrusion, a ubiquitous technique in manufacturing, involves the process of forcing molten material through a die to create a continuous profile. This method finds extensive applications in industries ranging from automotive to food packaging. The versatility of extrusion lies in its ability to process a wide array of materials, including plastics, metals, and ceramics.
The process begins with the raw material being fed into the extruder, where it is gradually heated to its melting point. Once molten, the material is forced through the die, taking on the desired shape. Extrusion offers precise control over dimensions and geometry, making it ideal for producing intricate profiles and long continuous lengths.
Moreover, advancements in extrusion technology, such as co-extrusion and micro-extrusion, have expanded its capabilities, enabling the manufacture of multi-layered products and micro-scale components.
The Art of Injection Moulding
Injection moulding, another pivotal manufacturing process, involves injecting molten material into a mould cavity at high pressure. This technique is renowned for its efficiency, repeatability, and scalability, making it the preferred choice for mass production of intricate components.
The process commences with the raw material being fed into the injection moulding machine, where it is heated to its melting point. Once molten, the material is injected into the mould cavity under pressure, where it solidifies, taking on the shape of the mould.
Injection moulding boasts remarkable precision, with tight tolerances achievable even for complex geometries. Furthermore, the ability to use a wide range of materials, including thermoplastics, thermosets, and elastomers, renders it indispensable across diverse industries, from medical devices to consumer electronics.
Advancements and Innovations
In recent years, both extrusion and injection moulding have witnessed significant advancements and innovations, propelling manufacturing capabilities to new heights.
In extrusion, developments such as 3D printing with extruded materials have revolutionized rapid prototyping and small-scale production. Additionally, the integration of artificial intelligence and machine learning algorithms has optimized extrusion processes, enhancing efficiency and minimizing material wastage.
Similarly, injection moulding has seen notable progress, with the advent of technologies like micro injection moulding enabling the fabrication of miniature components with unparalleled precision. Furthermore, the incorporation of sustainable materials and environmentally friendly processes reflects a growing emphasis on eco-conscious manufacturing practices.
Challenges and Future Directions
Despite their myriad benefits, extrusion and injection moulding face challenges in the form of material limitations, process complexities, and environmental concerns.
Addressing these challenges necessitates continued research and innovation. Future directions may include the development of novel materials tailored for extrusion and injection moulding processes, as well as the integration of IoT devices for real-time monitoring and optimization of manufacturing parameters.
Moreover, advancements in additive manufacturing techniques hold promise for complementing traditional extrusion and injection moulding processes, offering greater design freedom and customization options.
Conclusion
Extrusion and injection moulding stand as pillars of modern manufacturing, driving innovation, efficiency, and sustainability. From automotive components to medical devices, these processes underpin the production of diverse products that shape our daily lives.
As we navigate the ever-evolving landscape of manufacturing, it is imperative to embrace the opportunities presented by extrusion and injection moulding while addressing the challenges that lie ahead. Through continued research, innovation, and collaboration, we can unlock new possibilities and propel manufacturing into a future defined by precision, sustainability, and ingenuity.
GETTING A QUOTE WITH LK-MOULD IS FREE AND SIMPLE.
FIND MORE OF OUR SERVICES:
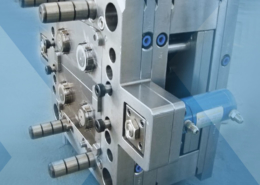
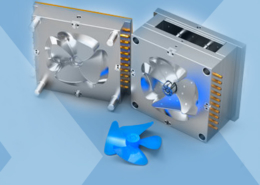
Plastic Molding

Rapid Prototyping
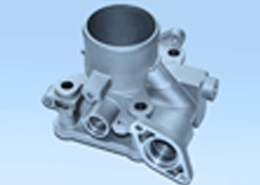
Pressure Die Casting
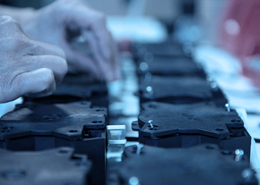
Parts Assembly
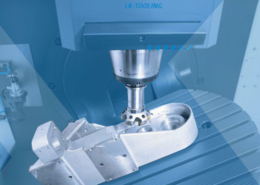