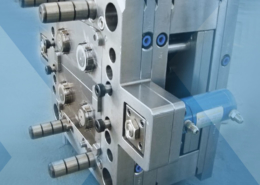
Machining High-Density Polyethylene (HDPE) in 2024 - machining polyethylene
Author:gly Date: 2024-10-15
3.Injection: The melt is transferred to an injector (which can be screw-driven, piston-driven, manual, or hydraulic) and then forcefully injected into the closed mold cavity.
Clients send us project information(stp file, parts material, parts color, and manufacturing volume) upon signing up NDA via email, Skype, or phone. We provide free quotation and project evaluation within 24 hours.
All of critical dimensions must be measured every 30 minutes with AQL lot standard, and we also provide SPC data to clients for any mass production.
Our project manager outlines all of critical checkpoints that used for process QC inspection. This process inspection is avoid defective parts to be produced.
We set up work instruction for whatever in-housing manufacturing process or outsourcing to ensure our are always the right foot to customer's specification.
Our engineering team reviews and evaluates each project deeply with profound experience and knowledge. A comprehensive DFM report will be provided to customer for review.
Our production team plans, performs, and monitors customer order that takes over from marketing team. Ensuring each order would be completed on-schedule, high quality, and within budget.
Golden sample with customer's signature will set aside of work station, so that our QC, technician, or operator can have standard reference.
Plastic injection molding is the most common manufacturing process to obtain plastic products with large scale of volume. Inno manufacturing engaged in plastic injection molding contract manufacturing service since 2001. Over 20 years of experience, we accumulated skillful engineers, technicians, and operators that enabled us to provide customer high precision, consistent quality, and professional services. Here below are our capabilities:
These classifications highlight the versatility of extrusion processes, allowing manufacturers to choose the most suitable method based on the material properties, desired product characteristics, and production requirements.
For metal parts in particular, extrusion is significantly more cost-effective than CNC machining when producing at scale. This makes it an attractive option for industries requiring large quantities of parts with consistent cross-sections.
Our sophisticated team brings a vast experience for a variety of industries including medical & beauty, home appliance, consumer electronics, sports & outdoor, automotive, etc.
Our QC team work throughout each project from start to shipping. IPQC inspects and monitor when production starts to run. and FQC double-check the finished products based on AQL standard.
Our experienced logistics team schedules and arranges each shipment to be delivered to customer punctually, cost effectively, and safely.
We assembled parts with whole unit to simulate product function that verify if our part structure or property function accordingly.
Our state-of-the-art plastic injection molding shop located in Shenzhen China provides cost-effective mold tooling and plastic injection molding services.
The availability of these different methods allows manufacturers to choose the most appropriate process based on the material properties, desired product characteristics, and production requirements.
The extrusion process involves several key steps to transform raw materials into a continuous product with a consistent cross-sectional profile. Here’s a detailed breakdown of the process:
With in-house mold making and injection molding shop, we work from mold tool making to plastic product contract manufacturing, available for parts weight from 0.5~2.0 KG with peace of mind at product quality, cost, and dead-time
This versatility allows manufacturers to choose the most suitable material for their specific application, whether it’s for structural components, consumer goods, or specialized industrial parts.
Based on quoted cost, timing, and other manufacturing terms, customers would confirm the order by issuing a PO and pre-payment. Normally we do 50%-50% of payment term for all of clients.
4.Cooling and Solidification: The molten plastic expands to fill the mold, then cools and solidifies, taking the shape of the cavity.
Extrusion is a manufacturing process that involves forcing molten or semi-molten material through a die with a specific cross-sectional profile to create a continuous length of product with a consistent shape. This process was invented by Thomas Hancock in 1820 and was fully established as an industrial manufacturing method by 1935.
Our on-line QC(IPQC) check out parts appearance comprehensively to avoid any flash, sink mark, short shot, deformation, scratch, dirty, marks, and so on.
To cater to customer's one-stop mold making and injection molding services, We combined mold making shop and plastic injection molding facility together, it enables us to make new mold and modify old mold tool conveniently and quickly. Inno manufacturing has over 20 years of mold making experience in making diverse kinds of mold tools. We make high precision, durable, and cost effective mold tools based on customers' requirement.
Starting from raw material sourcing, injection molding, until full assembled products, our on-site QC inspect and monitor the whole manufacturing process to ensure a high quality molded products to be made at us. We perform 100% of parts inspection with CMM, projector, and micrometer, our goal is to make zero defect rate for each orders.
2.Melting: The granules are compressed in the feed section, where frictional heat melts them into a thick liquid (melt).
Inno Manufacturing, a high quality contract manufacturer in Shenzhen China. We specialize in one-stop custom contract manufacturing services from parts to finished products.
Injection molding is a manufacturing process where molten material, typically plastic, is forced into a mold cavity under high pressure. The material then cools and solidifies, taking the shape of the mold to produce a wide variety of parts and products.
GETTING A QUOTE WITH LK-MOULD IS FREE AND SIMPLE.
FIND MORE OF OUR SERVICES:
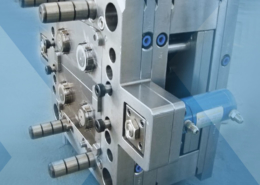
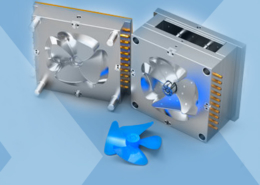
Plastic Molding

Rapid Prototyping
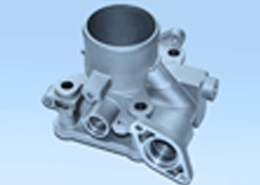
Pressure Die Casting
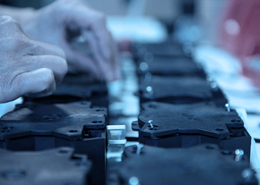
Parts Assembly
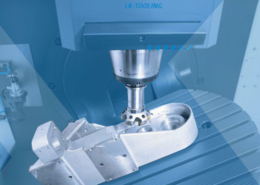