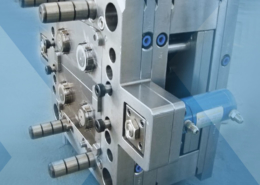
Machining High-Density Polyethylene (HDPE) in 2024 - machining polyethylene
Author:gly Date: 2024-10-15
Within these pages, you will acquire a comprehensive understanding of this specialized molding approach, a cornerstone for crafting optics, medical instruments, electronics, and other goods necessitating unparalleled precision.
The achievement of plastic parts characterized by astoundingly tight tolerances hinges on the meticulous control of these core factors:
This comprehensive guide delves into the depths of precise injection molding, providing a thorough exploration of its mechanics, pivotal advantages, employed equipment, design considerations, and more.
Mouldings can be joined by welding and adhesives. Decoration using printing, embossing or metallizing is possible. ABS is easily machined on conventional metalworking machinery although mouldings should be handled carefully as they can easily scratch.
This exceptional level of precision unlocks the ability to produce plastic components of extraordinary complexity, boasting precision-fit assemblies, optical-grade surfaces, and microscopically detailed features.
ABS is a tough material with most grades it is yellowish in colour with some degree of translucency but is close to opaque in nature although there are some transparent grades available. A wide range of properties are possible from medium impact through high and very high impact, as well as high heat, plating and flame retardant grades. Please Note: This page is for information purposes only. Rutland Plastics is an Injection Moulder and does not supply polymers.
Precise injection molding stands as a pivotal method in the realm of manufacturing, facilitating the creation of plastic components characterized by remarkably stringent tolerances, intricate geometries, and precise details.
This intricate procedure allows for the production of intricate components that would be otherwise unattainable through traditional injection molding techniques.
Precision plastic enclosures, connectors, insulators, and other elements tailored to meet the exacting tolerances of electronics materialize through this technique.
Mouldings can be produced in a wide variety of colours and are dimensionally stable with high gloss finishes possible. The surface is resistant to scuffing but has poor weathering properties. For outdoor use carbon black or UV stabilisers should be added.
Industries such as optics, medical devices, electronics, and automotive stand as fervent patrons of precise injection molding, leaning on its capability to yield plastic components of unparalleled accuracy.
Precise injection molding constitutes an advanced manufacturing technique, facilitating cost-effective mass production of remarkably intricate plastic components. This methodology finds its zenith in industries like optics, medical, and electronics, where the demand for plastic components boasting micron-level precision and accuracy is unwavering. With the appropriate expertise and equipment, the finesse of precise injection techniques can replicate nearly any plastic component design with unparalleled precision.
Dubbed both precise and precision injection molding, this specialized iteration of the conventional injection molding methodology establishes itself as an evolved form of its predecessor. Where conventional injection molding achieves tolerances of ±0.005 inches, precise injection molding surmounts this by attaining tolerances of ±0.001 inches, or even tighter margins.
Critical automotive plastic parts, ranging from headlamps and dashboards to exterior trims, are meticulously produced via precise injection techniques.
Precision optics encompassing lenses, prisms, mirrors, screens, light pipes, and other optical constituents owe their existence to this methodology.
ABS is widely used in the automotive industry due to its high impact strength, good heat distortion, high gloss appearance and suitability for electroplating. Typical uses are mirror housings, radiator grilles, wheel covers and instrument panels. Also used for office machines, pipes and pipe fittings, refrigeration, vacuum cleaners and other kitchen appliances. PC/ABS may be used where a higher heat resistance is required, for example in the manufacture of hair dryers, irons and coffee makers.
While it retains a fundamental kinship with traditional injection molding, the essence of precise injection molding lies in its specialized equipment designed to achieve unparalleled tolerances and consistency:
ABS has high impact strength, good scratch resistance and hardness with high gloss. It also has good mechanical strength and rigidity with good dimensional stability. Fillers can be incorporated to improve rigidity. ABS may be blended with other plastics, most commonly Polycarbonate (PC/ABS), in order to improve particular performance properties.
From inhalers to surgical implements, the flawless, dependable plastic components vital to medical devices find their genesis in precise injection molding.
Several compelling factors underscore manufacturers’ inclination towards adopting precise injection molding instead of the conventional approach:
GETTING A QUOTE WITH LK-MOULD IS FREE AND SIMPLE.
FIND MORE OF OUR SERVICES:
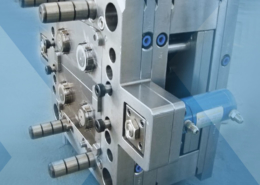
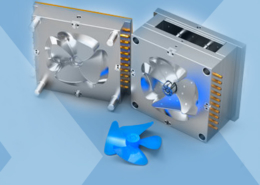
Plastic Molding

Rapid Prototyping
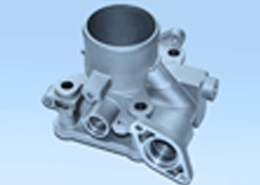
Pressure Die Casting
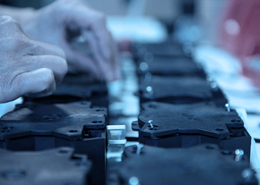
Parts Assembly
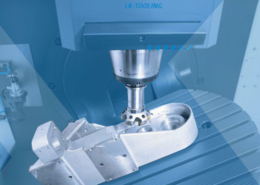