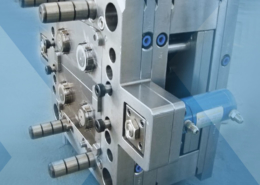
Low Density Polyethylene (LDPE) Injection Molding - ldpe injection molding
Author:gly Date: 2024-10-15
Editor's Note: A version of this post was originally published in June 3, 2020. It has been updated to include current trends and statistics.
This emphasis on the domestic market and local suppliers could indicate a potential for expansion on new markets for plastic mold manufacturers.
Most thermoplastics can benefit from the use of gas assisted moulding including Polypropylene (PP), ABS, HIPS, Polycarbonate (PC), PPC and Nylon (including glass filled grades).
• 8% of plastic mold manufacturers import raw materials, which is slightly lower than the 11% average across all manufacturers.• 76% of plastic mold makers focus on domestic distribution. This is slightly higher than the 70% of all manufacturers that sell their products on the domestic market.
American Tool & Mold, Inc. produces plastic molds used by other manufacturers. This Clearwater, Florida, company has 180 employees and can create customized molds for a wide range of applications, including multi-cavity molds and precision molds.
Developments over the past years in Gas Assisted Moulding or (Gas Assisted Molding to use the US spelling or Gas Injection Moulding being a common reference term) have resulted in advances in the way in which injection moulded components are manufactured. Enhanced quality, reduced cycle times and component weight reductions can be achieved by the process.
Most plastic injection moulded components can benefit from the use of gas assisted moulding. Applications from consumer goods to automotive parts benefit from the process. External Gas Assisted Moulding Applications:
Techniques have been developed whereby inert gas nitrogen is injected into the still molten plastic in the mould cavity. Acting from within the component shape, the gas inflates the component and counteracts the effects of the material shrinkage. The effect is to keep an internal pressure on the material until it solidifies and skins at the mould cavity surface. This is independent of any gate freezing.
Meanwhile, the global market for injection molded plastics is expected to reach a value of $473.4 billion by the year 2027. Currently, the industry is valued at $339.3 billion.
Are you looking for sales leads in the the plastic injecton molding industry or the manufacturing world at large? Access comprehensive profiles of 500,000 industrial businesses and one million executives with IndustrySelect. Try a free demo of IndustrySelect and reach new prospects in the industrial world!
Located in Boyne City, Michigan, LexaMar Corp. employs 400 people. This manufacturer uses rubber and plastic to produce exterior parts for the automotive industry.
To mould thermoplastic materials, they have to be heated to their melt temperature and injected into a closed metal mould. Cooling channels built into the mould act to cool the mould and in turn extract heat from the material.
Alwin offers design and product development services to create customized solutions. This Clintonville, Wisconsin, manufacturer has 150 employees and also produces commercial towel and napkin dispensers.
Hi-Tech Mold & Engineering, Inc. is located in Rochester Hills, Michigan. Its 200 employees work on components for vehicles, appliances, medical devices, and solutions for the aerospace and defense industries.
This Louisville, Kentucky, manufacturer has 300 employees. Jones Plastic & Engineering Co., LLC uses injection molding techniques to produce automotive parts, packaging, electronic components and products for the medical industry.
IndustrySelect provides clients with touch-point data for potential leads, including direct executive contact information and other actionable data among 500,000 companies in the manufacturing and energy sector.
Seaway Plastics Engineering, LLC has 151 employees and is located in Port Richey, Florida. This company specializes in engineering and low-volume runs. It creates products for the packaging, defense, medical, transportation and electronics sectors among others.
The Cinpres Gas Injection Company have developed a range of gas generation and control equipment to cover any manufacturing need. Some patented process variants are offered under licence.
According to MNI, the century-old data compiler that powers IndustrySelect's industrial database subscription, the plastic injection mold industry is a fairly small and specialized sector with 555 US-based companies. Half of these manufacturers are located in the Midwest.
When cooling, the material shrinks away from the mould cavity surface. To counteract this, more plastic material is injected (packing) into the cavity to try to maintain the surface contact.
Today we're taking a quick look at some additional facts on the plastic injection molding industry and exploring the top ten plastic injection companies in the United States.
CompanyCityState Number of EmployeesPlastek Industries, Inc.EriePA850LexaMar Corp.Boyne CityMI400Jones Plastic & Engineering Co., LLCLouisvilleKY300Hi-Tech Mold & Engineering, Inc.Rochester HillsMI200MMI Engineered SolutionsSalineMI192American Tool & Mold, Inc.ClearwaterFL180Ironwood Plastics, Inc.IronwoodMI155Seaway Plastics Engineering, LLCPort RicheyFL151AlwinClintonvilleWI150Decatur Mold, Tool & Engineering, Inc.North VernonIN150
Located in North Vernon, Indiana, Decatur Mold, Tool & Engineering, Inc. employs 150 people to produce military aircraft parts, car seats and automotive components.
Creating a more efficent mould process During the 'normal' injection moulding process of packing a mould cavity with plastic material, stresses are introduced into the component. Often these are along the line of flow of the packing material. In service these will result in the moulding warping and changing its dimensions. By using the gas medium, transmission of pressure throughout the moulding is more efficient and therefore less pressure is required. By injecting a gas into the material the cavity pressures are lower and being derived from within the component will considerably minimise the risk of warping In addition, with the material being pressed against the mould surface by the gas until it solidifies, the moulding will have better surface definition and will be more likely to be dimensionally correct. Enhanced Surface Definition External gas injection provides an enhanced surface definition of the component. Weight and Cost Reduction The combined benefits of not packing a moulding are less material is used. By not having to pack the material, and in thicker components the resultant hollow core, can save as much as up to 30% on the material used. Another major benefit is the reduction in machine cycle times that can be achieved. With no molten core to solidify, the material in the mould cavity solidifies quicker thus enabling the component to be ejected sooner. Quality Better dimensional control, and increased surface quality are major benefits of using gas injection. Sink marks caused by local thick/thin deviations in wall section can be eliminated.
Plastek Industries, Inc. has locations in four countries. Its Erie, Pennsylvania, headquarters is the largest plastic mold manufacturing facility in the US with 850 employees. They manufacture products like packaging for the beauty and cosmetics industry, food and beverage products, stock packaging options, and pharmaceutical packaging.
As U.S. manufacturers continue to contend with disruptions to the global supply chain, manufacturers are looking to source more supplies at home. One study found that 62% of manufacturers plan to source more supplies domestically in 2021.
Located in Saline, Michigan, MMI Engineered Solutions employs 192 people. This manufacturer has an in-house design team and uses injection and blow mold techniques to produce powertrain, exterior and interior parts for the automotive industry.
At a point in the moulding cycle, the material at the gate feed point solidifies (freezes) precluding any further packing. In thick components the shrinkage of the material from the mould surface is more pronounced.
This Ironwood, Michigan, manufacturer creates molds for products with precise requirements. Ironwood Plastics, Inc. and its 155 employees use advanced techniques like pressure monitoring, laser scanning and mold flow analysis to create specialized molds.
The industrial marketplace IndustryNet continues to see heightened domestic sourcing activity, including greater demand for plastic injection molding services, which reported thousands of searches from industrial buyers interested in plastic injection molding in 2020. Year-over-year category searches on the industrial marketplace IndustryNet were up 27% in 2020, while requests-for-quotes rose 102.1% and catalog downloads increased 21%. This trend reflects the growing number of manufacturers looking for domestic supplies, including plastic injection molding companies.
GETTING A QUOTE WITH LK-MOULD IS FREE AND SIMPLE.
FIND MORE OF OUR SERVICES:
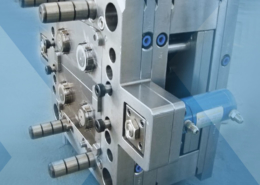
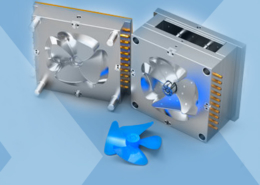
Plastic Molding

Rapid Prototyping
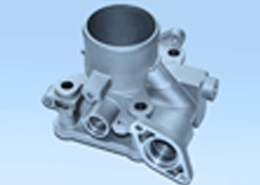
Pressure Die Casting
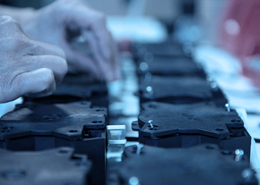
Parts Assembly
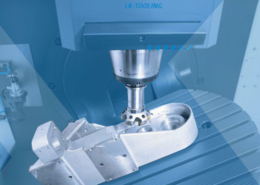