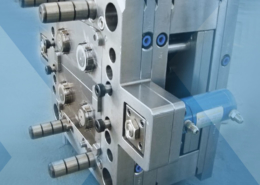
Low Density Polyethylene (LDPE) Injection Molding - ldpe injection molding
Author:gly Date: 2024-10-15
Change of oil temperature of injection molding machine leads to fluctuation of injection pressure. It is necessary to use a cooling device for hydraulic oil to stabilize oil temperature at 50 to 55℃.
Taking PC as an example, ordinary machine has a injection pressure of 177 Mpa, which can form a product with a thickness of 0.8 mm, and a precision machine with a injection pressure of 392 MPa can form a product with a thickness of 0.45 mm or more. Ultra high pressure injection molding machines can obtain products with a larger flow length ratio.
2. Clamping system has sufficient rigidity and clamping precision. So-called clamping precision refers to uniformity, adjustable, stable and repeatable of clamping force, position accuracy of opening and closing mold is high;
“It is a pleasure to work with your company; your team is most helpful in attending to our requirements and delivery schedules. We love your service that goes the extra mile!”
“I was extremely impressed with Allmould Plastics assistance and service with my latest custom moulding project. Their professionalism and service was second to none – their technical advice and help with drawings and prototyping is what helped us get ahead of the market, I would highly recommend their service.”
For variable pump injection molding machine, since pressure and flow output of oil pump are adjusted by swashplate angle of oil pump, it has high responsiveness and high responsiveness, repeatability of oil pump can reach 0.2% or less.
Turn Concept Into Reality From your initial concept, we provide product development, drafting and prototyping, all the way through to manufacture.
As an Australian Manufacturer for over 25 years, Allmould Plastics Group have the expertise and the facilities to take your project from initial idea right through to finished product
Ideal state of injection molding machine for product control is to directly control size, quality, apparent quality and mechanical properties of product to feedback control feedback signal. However, for the moment, direct measurement and conversion of these non-electrical quantities into electrical signals has not been solved, so it can only be solved by controlling controllable variables of injection molding machine that affect quality of above products, mainly including:
Ordinary injection molding machine: 147 ~ 177Mpa; precision injection molding machine: 216 ~ 243 Mpa; ultra high pressure injection molding machine: 243MPa or more, usually between 243 ~ 392 MPa.
(4) Injection system pressure, installed on injection cylinder with a strain sensor, detecting periodic signals, measuring injection pressure, holding pressure and back pressure signal;
Mold temperature has a considerable influence on later heat shrinkage of part, affects apparent quality and crystallinity of part, and also affects mechanical properties of part. If cooling time is same, thickness of product having a low mold cavity temperature is greater than thickness of product having a higher temperature.
2. In direct compression type clamping mechanism, mold section oil passage and injection section oil passage are separated.
3. Pressure, flow, temperature, metering can be controlled to precise accuracy. Multi-stage injection can be used to ensure reproducibility of molding process and repeatability of product.
4. Hydraulic system of precision injection molding machine should fully embody machine-electric-liquid-integration project.
Allmould Plastics Group is extremely passionate in relation to Medical component development, not only for the human side of this industry but also Veterinary
“Allmould Plastics is our preferred supplier for all our plastic injection moulding needs. Their exceptional quality and customer service never fail to impress.”
As already mentioned, injection molded products have been applied to various fields and are widely used to replace high-precision metal parts, thereby placing strict requirements on dimensional accuracy, quality accuracy, apparent quality and mechanical properties of injection molded parts. At the same time, higher requirements have been placed on process factors affecting quality of injection molded products.
Usually precision injection molding machines have two indicators: one is repeated size deviation of product; the other is repeated weight deviation of product. The former is difficult to compare due to size and thickness of product; the latter represents comprehensive level of injection molding machine.
Precision injection molding machines refer to molding machinery suitable for forming precision plastic products. How to measure or judge a precision injection molding machine?
Established in 1995, Allmould Plastics is a privately owned, family run business specializing in injection moulding. We place strong importance on customer satisfaction, constant high quality and value for money. Allmould Plastics has grown and developed over the last 20 years into a strong Customer Service orientated company. With our new built premises, fully designed to suit our customers’ needs and requirements, we are continually improving.
Hydraulic system of injection molding machine needs to use proportional pressure valve, proportional flow valve to achieve different working pressure and flow of system. Whether it is fixed pump hydraulic system or variable pump hydraulic system, there are proportional valves to control working pressure and working flow of oil pump output, achieve proportional linear adjustment.
1. Oil system requires use of proportional pressure valves, proportional flow valves or closed-loop variable pump systems.
Injection pressure has the most obvious effect on mold shrinkage of product. When injection pressure reaches 392 MPa, mold shrinkage rate of product is almost zero. At this time, accuracy of product is only affected by mold control or environment. Experiment proves that injection pressure is from 98 to 392 MPa, and mechanical strength of workpiece can be increased by 3 to 33%.
(2) It is required to protect low-pressure mold and control accuracy of clamping force. Because size of clamping force affects degree of mold deformation, it will ultimately affect dimensional tolerance of part.
Plastic Fabrication & Sheeting Products to serve a wide range of industries including point of sale display, building, manufacturing, retail, engineering and transport.
At present, injection molding machine generally adopts full computer control, and functions are gradually improved. It has intelligent functions such as “human-machine dialogue”, fault self-diagnosis, molding status monitoring, and SPC quality monitoring. Hydraulic system of injection molding machine is power component of each action of injection molding machine. Controller is hydraulic system control center, and all kinds of instruments are auxiliary monitoring part of running state of machine. Injection molding machine is actually an intelligent combination of machine, electricity, liquid and instrument.
(8) Injection speed is at least 4 levels of setting curve and feedback signal detection, displacement variable is converted to speed feedback, and feedback control is performed.
When temperature control system is heated, overshoot amount is small, temperature fluctuation is small. Precision injection molding uses PID proportional, integral, and differential temperature control to achieve a temperature accuracy of ±1℃. Temperature control accuracy of ultra-precision injection molding machine is ±0.1℃, and temperature deviation can be stably controlled between ±0.2℃.
Most of precision injection molding is done under high injection pressure and high rate of injection (connector or mobile phone button). Filling time is very short, generally only a few tenths of a second. This requires system to have high response performance, otherwise response will be delayed, eventually leading to a large deviation between output signal of system and input signal. Molding process is difficult to debug, which will directly affect size or weight stability of workpiece during production.
Precision injection molding machines require high injection speeds. Injection speed of precision hydraulic injection molding machines is required to reach 200mm/s or more, and injection speed of all-electric injection molding machines can reach 300mm/above.
Providing high end closures and packaging solutions to a various range of markets including food, dry goods, telecommunications, chemicals, beverages and more
(1) Due to high injection pressure of precision injection molding machines. This requires a high stiffness of clamping system. Parallelism of moving and fixed templates is controlled in the range of 0.08 to 0.10 mm.
(3) Pre-plastic displacement of screw, and periodic signal is detected by displacement electronic ruler, thereby extracting speed signal;
(1) Temperature of each section of screw melting cylinder, non-periodic signal, generally at least 4 sections of heating;
Accuracy of displacement sensor is required to be at least 0.1 mm, so that metering stroke, injection stroke and thickness of residual mat (injection monitoring point) can be strictly controlled to ensure accuracy of each injection and improve molding accuracy of product.
In order to achieve rated injection rate, there are two ways: one is to increase maximum injection pressure of system; the other is to modify parameters of injection device or injection system, including screw parameters;
High responsiveness of injection molding machine depends on scan time of controller, response time of oil pump and oil valve. For hydraulic systems with servo valves, there are considerable advantages in terms of response and repeatability.
Small Enough To Care With our new purpose built facilities, Allmould Plastics are large enough to get the job done right, but still small enough to care.
1. Requirements for repeatability (reproducibility) of injection molding parameters are high, and multi-stage injection feedback control should be adopted.
AMP Circular is not a typical business but rather a platform that sits under the Allmould Plastics Group to manage circular and recycling programs through the public and private sectors in Australia
This requirement is for a direct pressure injection molding machine because direct pressure injection molding machine starts to inject melt and fill mold cavity immediately after high pressure is applied. At the same time, oil must be filled with clamping cylinder to form a high clamping pressure. Otherwise, middle plate will retreat due to filling pressure and mold expansion force, which is not allowed. This requires that mold clamping oil line and injection oil circuit are separated. Otherwise, oil pump overload problem occurs due to oil filling clamping cylinder and injection cylinder at the same time, injection speed and system stability are affected.
Generally, weight error of ordinary injection molding machines is about 1%, and better machine can reach 0.8%. Below 0.5% is a precision machine, less than 0.3% is an ultra-precision machine. As mentioned above, precision injection molding machines require product dimensional accuracy to be generally within 0.01 to 0.001 mm.
(4) Plasticized parts: screw, screw head, check ring, barrel should be designed into a structural form with strong plasticizing ability, good degree of homogenization and high injection efficiency; screw drive torque is large and can be continuously variable.
Allmould Plastics Group is heavily involved in the development of plastic construction parts within the Construction Industry across Australia and beyond
GETTING A QUOTE WITH LK-MOULD IS FREE AND SIMPLE.
FIND MORE OF OUR SERVICES:
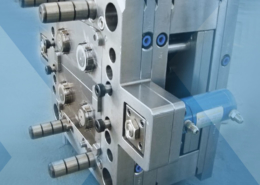
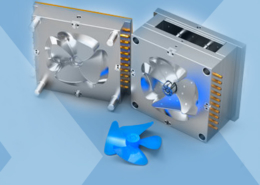
Plastic Molding

Rapid Prototyping
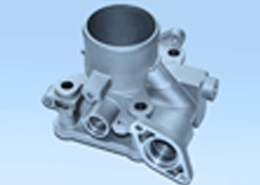
Pressure Die Casting
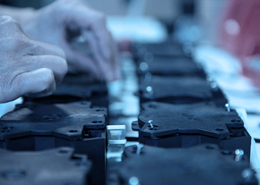
Parts Assembly
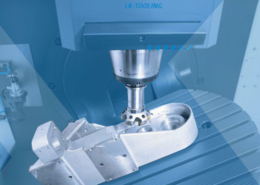