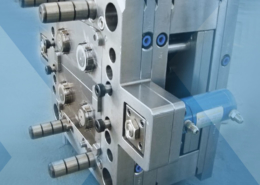
Limited Growth Among Top 100 Injection Molders - top 100 injection molding compa
Author:gly Date: 2024-10-15
The injection molding process is reasonably quick and produces a detailed plastic piece that often does not require additional assembly or processing. Because of this quality, injection molding carries a higher cost than plastic extrusion. The injection molding process is often used to make the following plastic items:
In rapid prototyping, the use of a prototype mold for plastic injection, therefore, makes it possible to obtain small series using the right material at a lower cost and in reduced time. It is a very good solution for testing your concept quickly and cheaply. There is no need to sacrifice the quality of the final part. You, therefore, obtain reliable information (mechanical, geometric, assembly and industrialization) on the final parts as well as the subsequent production of a series injection mold.
Thank you for your comment. Best format would be : STP / IGS / XT. I you could provide one of these please we could quote your project.
Thank you for your comment. We would only need the CAD design of the toothbrush, CAD design of mold would be done by us. On of our project manager will reach to you by email to have more information about you injection molding project.
The injection molding method begins by feeding plastic pellets into a hopper. The granules are then compressed, and the frictional heat melts the plastic. Next, the meld goes into the injector, which directs the liquid into die cavities. From here, the molten material fills the mold, taking the shape of the mold. Once the material is cooled and solidified, the die is opened, and the specific object is obtained.
Deciding between plastic extrusion vs. injection molding can be a challenging choice for product designers. It’s up to the manufacturer to understand the intricacies of each process to help their clients make informed decisions. It’s important to note that both methods have their advantages and are valuable in the world of plastic manufacturing.
This process consists of injecting a molten polymer (thermoplastic material) into the prototype tooling under high pressure. The plastic material is then cooled and solidifies, taking on the shape of your part. This prototyping technique allows the use of a very large range of ‘right material’ resins. The overmolding of metal inserts and the production of parts incorporating two materials is possible.
Thank you for you comment. We would need you specifications to advice and quote you : CAD files, volume required, material etc.
The extrusion process is ideal for end products that need a smooth finish, like industrial piping. It can also be used to create complex cross-sections such as tubing found in many medical devices and food processing applications. Products commonly formed using the plastic extrusion method include:
Unlike plastic extrusion, injection molding can be used to form three-dimensional shapes. With this method, manufacturers inject plastic resin into a mold where it settles and cools into the desired shape.
The design of our injection rapid tooling is based on a standard ‘mold base’ frame and interchangeable aluminum core and cavity inserts. This reduces the investment costs and production times inherent in plastic injection. This is our rapid production technique which is the most expensive. However, it makes it possible to obtain functional parts made from the ‘right material’. They can be marketed or used in transition production.
If you’re looking for equipment to support your plastic extrusion or injection molding processes, you can rely on Plastrac for high-quality material blenders and loader systems. We have everything from gravimetric mixers to injection molding accessories to keep your manufacturing company running smoothly. Get in touch with us today for a quote!
First, plastic granules are placed into the feeder, where they are melted into a thick liquid. From the feeder, the meld will be pushed through the die opening and extruded from the end. Once it is cooled, the product will be in the desired shape. From here, manufacturers can cut the plastic piece into different lengths.
The ‘prototype mold’, or ‘rapid plastic injection tooling’ is based on the same principle as series plastic injection molds, but has a simplified and accelerated design. It is also not intended for long-term use. The use of a common mold base and aluminum for the molding parts makes it possible to reduce investment costs and machining time. Production of the prototyping mold takes between 2 and 4 weeks and is 40 to 60% less expensive than a traditional mold. The cost and design time of the mold depends on the shape complexity of the part to be molded. After a complete analysis of your plastic parts, our design office creates the tooling plan of your mold. We then start its production according to your specifications.
Injection molding is based on the molten die casting method, which means a thick liquid called melt is injected into a mold to form the desired object.
Hello, I have 3D drawings for a project. I would like a quote for injection molding or your prototype mold system. Thank you
Cases, cowlings and hulls are examples of parts that we produce very regularly. In a field that requires many tests and certificates, such as the medical sector, the plastic injection can satisfy the regulatory requirements and constraints. (Find out more on our page about standards.)
Our rapid plastic injection molding solutions are specially adapted to the production of prototypes and small series of plastic parts (from 100 to 1000+ parts). Inspired by traditional molding techniques, we inject your plastic parts using an aluminum prototype mold (or rapid tooling). The results achieved with this technique are equivalent to series molds. The robustness, mechanical properties and industrialization information are identical.
Within the realm of plastic processing, there are several methods of manufacturing. Two of the most popular processes include extrusion and injection molding. While they produce similar results, they use different equipment and techniques. Whether you are forming plastic pieces for commercial, industrial, or medical use, the manufacturing method you use will vary. Here are the important differences between plastic extrusion and injection molding.
Both extrusion and injection molding are methods of plastic molding. However, they differ in execution. With extrusion, melted plastic is pushed through a die to create a specific shape. The extrusion method is used for two-dimensional objects.
Now that we’ve clarified the key difference between extrusion and injection molding, we can take a more in-depth look at the extrusion process.
This technique allows the production of small series that are close to reality. The applications of plastic injection molding are very varied. They are particularly useful in the automotive, packaging, medical, and electronics sectors.
GETTING A QUOTE WITH LK-MOULD IS FREE AND SIMPLE.
FIND MORE OF OUR SERVICES:
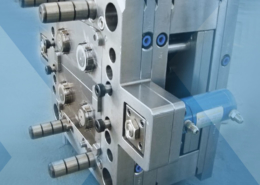
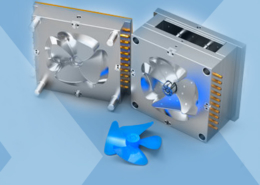
Plastic Molding

Rapid Prototyping
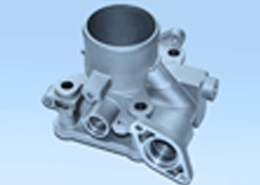
Pressure Die Casting
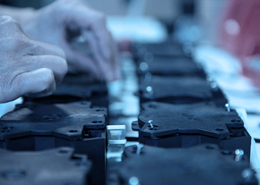
Parts Assembly
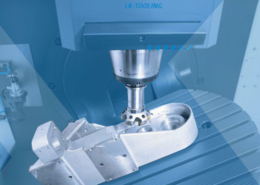