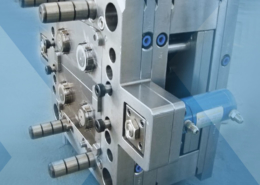
Contract Injection Molding: Streamlining Production Processes
Author:gly Date: 2024-06-08
Introduction
Contract injection molding, a cornerstone of modern manufacturing, serves as a vital link in the production chain for countless industries. This article delves into the intricacies of contract injection molding, elucidating its significance, processes, advantages, and future prospects.
Definition and Background
Contract injection molding entails outsourcing the manufacturing of plastic parts to specialized firms equipped with injection molding machines. These firms, known as contract manufacturers, offer their expertise and facilities to produce components according to the specifications provided by the client. The technique gained prominence in the mid-20th century and has since become indispensable in various sectors, including automotive, aerospace, medical, and consumer goods.
Evolution of Injection Molding
Injection molding, introduced in the 1930s, revolutionized the production of plastic components. Initially used for simple items, such as buttons and combs, its capabilities expanded with technological advancements. Today, it enables the cost-effective and rapid fabrication of intricate parts with high precision.
Market Dynamics
The contract injection molding market has witnessed significant growth due to several factors, including globalization, specialization, and the quest for operational efficiency. Companies increasingly opt for outsourcing to focus on core competencies while leveraging the expertise and resources of contract manufacturers.
Technological Innovations
Advancements in materials science, automation, and digitalization have propelled the evolution of contract injection molding. From the adoption of biodegradable polymers to the integration of real-time monitoring systems, innovations continue to enhance efficiency, quality, and sustainability in the manufacturing process.
Process Overview
Tooling and Design
The process commences with tooling design, where engineers collaborate with clients to create molds tailored to the desired specifications. Computer-aided design (CAD) software facilitates the precise modeling of components, optimizing functionality and manufacturability.
Material Selection
Selecting the appropriate material is paramount to the success of injection molding projects. Factors such as mechanical properties, thermal stability, and cost-effectiveness are meticulously evaluated to ensure optimal performance and durability of the final product.
Injection Molding
During the molding phase, molten thermoplastic material is injected into the cavity of the mold under high pressure. The material solidifies upon cooling, assuming the shape of the mold cavity. Advanced machinery and automated systems ensure consistency and repeatability in production.
Advantages and Challenges
Advantages
Contract injection molding offers myriad benefits, including:
Cost Efficiency
: By outsourcing production, companies can mitigate capital expenditure on equipment and facilities, optimizing cost structures.
Scalability
: Contract manufacturers accommodate varying production volumes, enabling clients to scale operations without significant investments.
Expertise and Specialization
: Leveraging the proficiency of specialized firms ensures high-quality output and access to advanced technologies.
Time-to-Market
: Streamlined processes and rapid prototyping capabilities expedite product development cycles, facilitating timely market entry.
Challenges
Despite its advantages, contract injection molding presents challenges such as:
Quality Control
: Maintaining consistent quality across batches necessitates stringent quality control measures and close collaboration between stakeholders.
Intellectual Property Protection
: Protecting proprietary designs and processes poses challenges in an outsourced manufacturing environment, requiring robust contractual agreements and security protocols.
Supply Chain Risks
: Dependency on external suppliers entails inherent risks, including supply chain disruptions, geopolitical factors, and fluctuations in material costs.
Future Perspectives
Contract injection molding is poised for continued growth and innovation:
Sustainability
: Embracing eco-friendly materials and energy-efficient processes aligns with evolving regulatory frameworks and consumer preferences.
Additive Manufacturing Integration
: Hybrid approaches combining injection molding with additive manufacturing techniques promise enhanced design flexibility and customization.
Digital Transformation
: The integration of data analytics, artificial intelligence, and IoT technologies optimizes process efficiency, predictive maintenance, and supply chain management.
Conclusion
Contract injection molding epitomizes the convergence of expertise, technology, and collaboration in modern manufacturing. Its role in facilitating cost-effective, scalable, and agile production processes is indispensable across diverse industries. Embracing technological innovations and addressing inherent challenges are imperative for harnessing the full potential of contract injection molding in the dynamic landscape of global manufacturing.
This article has provided a comprehensive overview of contract injection molding, highlighting its definition, processes, advantages, challenges, and future prospects. As industries continue to evolve, embracing collaborative partnerships and leveraging advanced manufacturing technologies will be key to driving innovation and competitiveness in the era of Industry 4.0.
GETTING A QUOTE WITH LK-MOULD IS FREE AND SIMPLE.
FIND MORE OF OUR SERVICES:
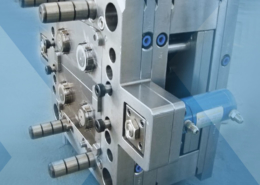
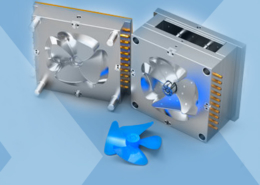
Plastic Molding

Rapid Prototyping
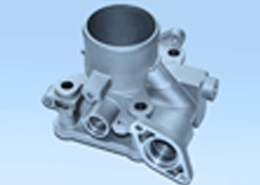
Pressure Die Casting
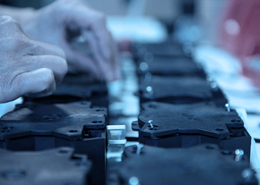
Parts Assembly
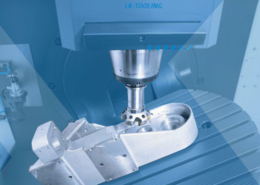