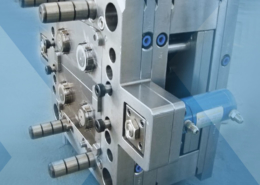
Unlocking the Potential of Complex Injection Molding
Author:gly Date: 2024-06-08
The Essence of Complexity
Complex injection molding represents a pinnacle of engineering ingenuity, merging advanced materials science with intricate tooling techniques to produce components of unparalleled sophistication. Unlike conventional injection molding, which primarily deals with simple geometries, complex injection molding ventures into the realm of intricate designs, undercuts, and challenging geometries. This process enables the fabrication of parts with multifaceted shapes and functionalities, revolutionizing industries ranging from automotive to medical devices.
Complex injection molding capitalizes on cutting-edge technologies, such as multi-cavity molds, micro-injection molding, and overmolding, to push the boundaries of what is achievable. It requires meticulous attention to detail, from the design phase through production, to ensure the integrity and precision of the final product. The allure of complex injection molding lies in its ability to transform abstract concepts into tangible realities, fostering innovation and driving progress across diverse sectors.
Material Selection and Compatibility
One of the foundational aspects of complex injection molding revolves around material selection and compatibility. The choice of materials profoundly influences the manufacturability, performance, and longevity of the final product. Engineers must carefully evaluate a plethora of factors, including mechanical properties, thermal stability, chemical resistance, and biocompatibility, to determine the most suitable material for the intended application.
Furthermore, achieving optimal material compatibility is paramount, especially in multi-material or overmolding processes. The seamless integration of different materials necessitates a comprehensive understanding of their respective properties and behaviors during the injection molding process. Advanced techniques, such as material testing, rheological analysis, and computational modeling, aid in predicting and mitigating potential issues, ensuring the successful execution of complex injection molding projects.
Precision Tooling and Mold Design
At the heart of complex injection molding lies precision tooling and mold design, which serve as the cornerstone for achieving intricate geometries and tight tolerances. The design and fabrication of molds require a synergistic blend of artistry and engineering prowess, as each intricacy must be meticulously crafted to exacting specifications.
State-of-the-art technologies, such as computer-aided design (CAD), computer-aided manufacturing (CAM), and additive manufacturing, empower engineers to push the boundaries of mold complexity and sophistication. Advanced features, including side actions, collapsible cores, and unscrewing mechanisms, enable the realization of complex geometries and undercuts previously deemed unattainable.
Process Optimization and Control
Process optimization and control play a pivotal role in ensuring the reproducibility, efficiency, and quality of complex injection molding operations. From machine settings to injection parameters, every facet of the manufacturing process must be meticulously fine-tuned to achieve desired outcomes consistently.
Statistical process control (SPC), real-time monitoring systems, and automation technologies facilitate data-driven decision-making, enabling engineers to identify and address potential issues proactively. Additionally, advanced molding techniques, such as gas-assisted injection molding and in-mold labeling, offer enhanced capabilities for producing complex parts with superior surface finish and structural integrity.
Conclusion: Pioneering the Future of Manufacturing
In conclusion, complex injection molding represents a paradigm shift in the field of manufacturing, unlocking new realms of possibility and driving innovation across industries. By harnessing the synergistic interplay of materials science, precision engineering, and process optimization, complex injection molding transcends traditional boundaries, enabling the realization of previously unimaginable designs and functionalities.
As we look to the future, continued advancements in materials science, digital manufacturing technologies, and sustainability initiatives will further propel the evolution of complex injection molding. By embracing collaboration, creativity, and continuous improvement, we can leverage the transformative power of complex injection molding to address emerging challenges, propel economic growth, and enhance the quality of life for generations to come.
GETTING A QUOTE WITH LK-MOULD IS FREE AND SIMPLE.
FIND MORE OF OUR SERVICES:
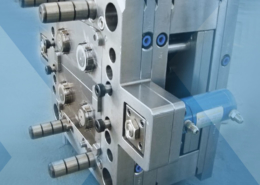
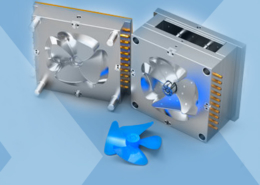
Plastic Molding

Rapid Prototyping
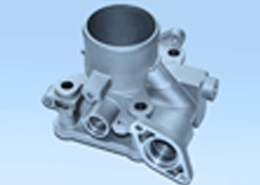
Pressure Die Casting
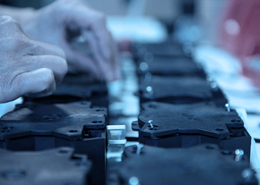
Parts Assembly
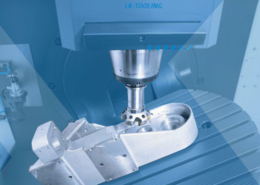