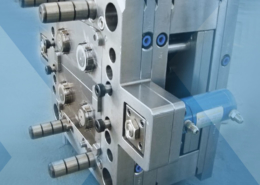
KCS Australia: Plastic Injection Moulding - plastic injection moulding manufactu
Author:gly Date: 2024-10-15
Ejector stroke H is usually equal to the product height L plus a safety margin (5~10mm). That is, H=L+(5~10mm). Here L is the distance from the highest point to the lowest point of the product in the mold opening direction.
2 shot plastic injection molding enables the use of dissimilar resins to be used in a multi-part assembly. In some instances, a 2 shot mold application may include different colors and also soft and hard materials assembled together in in a single part. Some of the benefits of 2 shot plastic injection molding include elimination of post-molding assembly, fewer injection molding machines to make a single part and reduced part handling by operators by utilizing a single molding operation.
According to the calculation of the stroke of the double-action flange ejector, the stroke distribution of the vertical flange and the side flange needs to be considered to ensure smooth ejection.
Midwest Mold specializes in the design and build of 2 shot plastic injection molds and has successfully manufactured pre-production and production tooling for structural, water management, crash impact and noise reduction applications.
With 2 shot molding, parts can include a clear window, integrated gaskets, movable segments, water shields, or sound or vibration reduction.
Your Name: Your Email: Resin: Estimated Life of Program: Estimated Annual Volume: Estimated Order Quantities (if Low Volume Molding Project): Target Price (Tooling/Piece Part): Message Attach a File ❌ ❌
The main function of the ejector stroke of the injection molding machine is to ensure smooth demolding of the product, protect the mold and the product, adapt to the needs of different products, improve production efficiency, and extend the service life of the mold.
Midwest Mold offers a cost-effective solution to challenges caused by parts that require the use of two different plastics. 2 Shot injection molding is a process that molds one part using two different plastic resins. This enabling technology allows you to use two colors of plastics or to integrate both hard and soft plastics into one part without any post-molding assembly.
This is the most common ejection method, which uses mechanical devices (such as ejector pins, ejector pins, etc.) to push the molded plastic parts out of the mold. The ejector rod is fixed on the frame and does not move. When the mold is opened, the movable template moves back. The ejector rod passes through the center hole of the movable template and acts on the top plate of the mold, pushing the top plate to eject the product out of the mold. The length of the ejector rod is determined by the thickness of the mold and can be adjusted by the thread.
If the ejection device stroke is insufficient, the plastic parts will not be able to completely detach from the mold, thus affecting production efficiency and product quality. By increasing the ejector stroke, it can be ensured that the plastic parts can be completely detached from the mold after the mold is opened, avoiding product defects or manual intervention caused by insufficient ejection.
2 shot injection molding reduces the number of machines and molds required to mold two materials together into one part, and it minimizes part handling, all of which can add up to lower costs. In addition to financial benefits, 2 shot molding can provide:
For inclined roof structures, the calculation of the ejection stroke H needs to take into account the angle of the inclined roof and the horizontal stroke.
For some plastic parts with complex structures, such as products with deep depressions in the middle, a longer ejector stroke may be required to achieve smooth demolding. By optimizing the ejection stroke, the mold design can be simplified, the product appearance can be protected, and the requirements for the injection molding machine stroke can be reduced.
When selecting an injection molding machine, the ejector stroke should be reasonably selected according to the appearance of the product and the design structure of the mold. Generally, the maximum ejector stroke of the machine is fixed, and the user can adjust it according to the specific product when using it. When ordering a machine, the ejector stroke should be large so as to be suitable for the molding of more products. For example, the ejector stroke of the Haichen HCK110 injection molding machine is 110mm.
Extending the ejector stroke does not require changing the internal structure of the mold, which reduces the production cost, and the extended ejection stroke can be accurately controlled by setting a scale, thereby improving the demolding efficiency.
The ejector stroke is the maximum distance the ejector moves forward to eject the plastic part, usually from 110mm-450mm.
According to the calculation of the mold slider stroke, the undercut distance and safety distance need to be considered to ensure that the product will not interfere with the slider when ejected.
The ejection mechanism is pushed by the hydraulic system, which is suitable for situations where a large thrust is required.
For questions regarding our quote form, data transfers or our FTP site for large files, please contact our data coordinator midwestmold@midwestmold.com.
The application of the secondary ejection mechanism shows that by reasonably setting the ejection stroke, the overall structure of the mold can be simpler, safer, and more reliable to use, and meet the automation needs of mass production.
S is the horizontal stroke of the inclined top, S1 is the downward stroke of the inclined top, X is the angle of the inclined top, Y is the downward angle of the inclined top
In some cases, a short ejector stroke may cause the product to warp or deform during demolding. By adjusting the ejector stroke, the demolding speed and force of the product can be better controlled, thereby reducing the risk of product damage.
According to the mold, the ejection stroke is determined according to the ejection stroke required by the product. Usually, there is a certain safety margin more than the ejection stroke required by the product to ensure that the product can be removed smoothly.
It is to ensure that the molded product can be smoothly separated from the mold so that the next mold action can continue. Only effective ejection force and ejector stroke can make the molded product finally smoothly separate from the mold.
Compressed air is used as the power source to push the ejection mechanism to move. Pneumatic ejection is accomplished by compressed air, which blows the plastic product directly out through many tiny holes in the molding mold. This ejection method does not leave any ejection marks on the surface of the product but requires the addition of pneumatic auxiliary equipment.
In addition, the ejector stroke also has the function of limit protection, which is used to limit the distance of the ejector forward and backward to ensure smooth de-moulding of the product and accurate reset of the ejector. For some specially designed molds, such as molds with secondary ejection mechanisms, the total ejector stroke must be greater than the first ejector stroke to ensure that the inclined ejector is completely separated from the undercut part and the core pulling action is completed.
In addition, the ejector stroke is closely related to other technical parameters such as ejector force and ejector speed. The ejector force refers to the maximum thrust of the ejector device, while the ejector speed refers to the speed at which the ejector device moves. These parameters work together to ensure that the plastic part can be removed from the mold safely and effectively.
there is an ejector cylinder installed behind the movable template, which pushes the piston, that is, the ejector rod, to work. There are bolts on the piston to adjust the length of the ejector rod. When the mold is opened, the template moves backward and the ejector cylinder pushes the ejector rod to extend. The ejection force, speed, time, and stroke are adjusted by the hydraulic system, which can be reset automatically and can eject the product during or after the mold opening process, which is conducive to shortening the injection molding cycle.
Specifically, the ejector stroke determines whether the plastic part can be de-molded smoothly. For example, a long plastic part requires a longer ejector stroke, while a short plastic part can use a shorter ejector stroke. When purchasing an injection molding machine, it is usually recommended to choose a larger ejector stroke to accommodate a wider variety of products.
GETTING A QUOTE WITH LK-MOULD IS FREE AND SIMPLE.
FIND MORE OF OUR SERVICES:
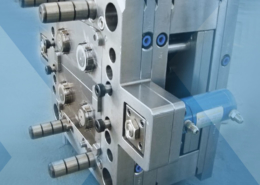
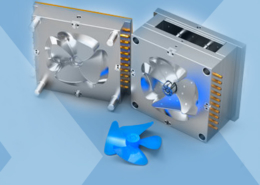
Plastic Molding

Rapid Prototyping
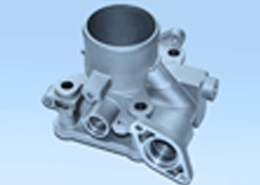
Pressure Die Casting
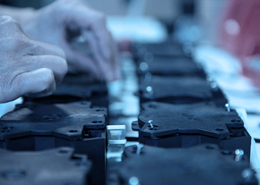
Parts Assembly
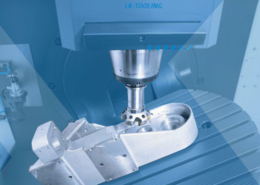