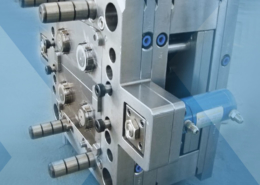
KCS Australia: Plastic Injection Moulding - large injection moulding
Author:gly Date: 2024-10-15
It is a very popular method to manufacture large, hollow molded plastic parts. It enjoys numerous advantages such as remarkable surface finish and geometric accuracy.
Our injection molding process is guided by an unwavering commitment to precision and consistency. Customer satisfaction is our primary goal, and we ensure that the tools and processes we use serve that goal. We utilize hydraulic and hybrid hydraulic electric machines that offer exceptional precision, as opposed to an injection molding machine focused solely on speed. By leveraging our expertise in process control and material behavior, we can achieve precise and consistent results.
In the event of a defective plastic part, we implement reactive Quality Control (QC) measures. We employ a corrective action process, starting with a corrective action report to contain the issue and prevent further defective parts from being released. Through root cause analysis, we identify the underlying cause of the defect and implement the necessary corrective solutions, such as process adjustments or molding machine operator training. This information is then fed back into our Quality Assurance system to further refine our precision plastic injection molding process and maintain the highest level of dimensional accuracy in each plastic component we manufacture.
Ultraviolet (UV) bonding is another permanent bonding process. The ultraviolet bonding process carries the advantage of bonding plastics to other materials such as glass, ceramic, and metal. Bonding using ultraviolet light is a highly intense concentration of ultraviolet lighting that instantly dries or cures the adhesive. Moreover, UV bonding works in seconds to bond plastic components with other materials. A solid bond forming in moments lessens production time and often reduces rates.
Heat staking is another permanent bonding technique. This bonding concept takes advantage of the base material being malleable plastic. The base material is heated up and the plastic reformed using a combination of heat and pressure to model the plastic around the second piece forming a hardware-free bond. One advantage is that we can use it to combine two alike or dissimilar materials. Also, it is a reasonably easy bonding process that does not require any additional parts or materials.
To facilitate our customers, we have developed an efficient online quotation platform that provides rapid quotes based on the design files you upload. Augmenting these quotes is a detailed design feasibility analysis and DFM feedback, which is just one example of the personalized attention you will get here at RapidDirect. Contact us to get in touch with our team for your custom plastic manufacturing needs.
The automotive industry is controlling fuel efficiency by switching to lightweight plastics. Using plastics for many auto parts reduces the vehicle’s overall weight and increases fuel efficiency. With the need for better fuel economy solutions, the automotive business has turned to plastics manufacturing for many automotive components. Additionally, government regulations recently are pressing the automotive industry to move from iron and steel to plastics. This push from the government is shifting the automotive industry towards higher-grade plastics in place of metals. The recent drive for a plastic manufacturing process in the automotive segment allows us to anticipate that injection molded plastics will increase rapidly under these new regulations.
Our commitment to precision extends to our production processes. We employ proactive Quality Assurance (QA) techniques to prevent defects and rejections. By identifying potential risks and areas of improvement, we ensure consistent and high-quality production. Our operators perform regular inspections throughout the production run, and we conduct maintenance on molds and injection machines to ensure longevity and precision.
In order to maintain the highest standards of quality, IMS utilizes the concept of Acceptable Quality Limits (AQL) based on Mil standard 105D. AQL is a heavily utilized sampling plan across our manufacturing processes. It enables us to conduct Out of Box Audits (OAB’s) and statistically assess the quality of finished products. By referring to the AQL chart (see below), we determine the number of parts in a lot that need to be tested to ensure compliance with quality standards. This rigorous sampling plan allows us to identify any potential deviations and take corrective actions promptly, ensuring that our products consistently meet the desired level of precision. By employing AQL, IMS further strengthens our commitment to making parts right the first time and upholding our reputation for delivering precise, high-quality plastic components.
Towards the end of the primary gas penetration phase, the resin starts to cool down and contract. Due to the gap created by this thermal contraction, the gas pressure slightly decreases. This can cause part deformations and induce geometric errors, which are never desirable.
The gas assist injection molding process takes place in three stages (refer to the injection molding diagram below). Each stage constitutes an important step of the process and requires design sense and practical skill from the manufacturing team.
Gas assisted molded parts to have various applications. Generally, it is for injection molding hollow parts with ribbed/boss features and smooth surface finish requirements.
This process is well-suited to manufacture hollow, lightweight geometries. Additionally, the gas exerts constant pressure on the resin, which helps to minimize shrinkage and distortion/warpage. These factors are usually the main reason for the deteriorating dimensional accuracy of thin walls. Thus, thin-walled parts are another special application of this process.
Hence, there is a secondary gas penetration phase where more gas flows into the mold to fill up these gaps. This maintains uniform pressure and guarantees a neat fill.
Plastic manufacturing is a versatile field that is continually developing. When it comes to complex geometries and top-of-the-class manufacturing capabilities, gas-assisted injection molding is one of the number one options.
Precision begins with the design phase. Our engineering team thoroughly reviews part drawings, evaluating them for molding and tooling issues. We examine features that may pose challenges for molded plastic, such as undercuts, texture requirements, draft angles, and thickness. By addressing these concerns early on, we ensure that the final design will meet the required form, fit, and function while optimizing the manufacturability of the part.
In this article, we dive deep into this manufacturing process and discuss what it is and its types, applications, and materials.
Gas assisted injection molding is a plastic molding process that combines principles of conventional injection molding with the application of pressurized inert gas. It uses mold cavities in the form of the product’s shape. The mold is partially filled with ~70%-80% molten plastic raw material. Injecting Nitrogen gas fills the remaining volume to pack the plastic material against the mold’s walls.
To simplify the tooling process, IMS engineers utilize the principles of Design for Manufacturing (DFM). By employing intelligent mold design strategies, we can achieve complex geometries using simple precision tooling methods. Our goal is to engineer cost-effective tooling solutions while maintaining the highest levels of precision and delivering on customer requirements. By collaborating closely with toolmakers, we guarantee that the tooling is precisely crafted to meet the specific requirements of each project. We also perform routine maintenance and upkeep on each precision mold to ensure mold longevity.
At first, the mold clamps shut, and raw resin is fed into the hopper of the injection molding equipment. Just as in a regular injection molding process, the machine melts and pressurizes the resin in its screw-feed section.
The pressure and growing volume of the gas bubble push the molten resin to the boundaries of the mold. The pressure of the gas remains constant during this process, ensuring that the resin reaches all corners of the mold, filling it up.
At Integrated Molding Solutions, precision is at the core of everything we do. From the initial design phase to the production process and quality control, we strive for consistency and accuracy in delivering high quality plastic parts. By employing cutting-edge technologies, adhering to rigorous quality control standards, and leveraging our expertise in material behavior and process control, we ensure that every part meets the required specifications. Partner with IMS for precision injection molding services that meet your needs, and experience the difference that true precision can make in your molded parts and products. Contact us today for additional information.
Insert molding is a systematic process of modeling thermoplastic material around an additional component. Most pliable thermoplastic resins are suitable for the insert molding process. The added piece is often a metal part. The main advantage of mold-in inserts is that generic threaded inserts are readily available in standard sizes. Generic inserts help keep costs down and avoid further customization costs. Metal inserts provide properties that plastic alone wears down over time, such as threading.
If you want to produce high-quality machined parts with a sleek appearance, it’s essential to consider some critical factors related to CNC machining.
Plastics are a growing industry that is becoming prominent in the healthcare sector. The medical industry is establishing a foothold in plastic 3D printing as a modern solution. Plastic molds help doctors to see a CT scan in 3D physically. The dental occupation often uses 3D plastic molds to custom fit parts before surgery. Research suggests that Medical grade polymers used in healthcare will positively impact growth in the medical field over the next decade.
After the required amount of resin enters the mold, the process of primary gas penetration begins. A pressurized gas source releases nitrogen into the spruce network, which forms a bubble inside the resin material.
These two forms of painting apply color to the part. The painting application is ideal after molding. Painting can be any color or even metallic finishes painted over plastic. This application also helps with particular requirements such as non-static parts. In comparison, pad printing permanently places an image onto the components. Pad printing is similar in nature to a rubber stamp. An inverted image is coated with paint and laid against the part to transfer the image to the part’s surface.
At Integrated Molding Solutions, we deliver precision plastic injection molded parts to your door. IMS provides innovative plastic solutions offering guidance and help for small and large businesses alike.
Our state-of-the-art equipment and years of experience guarantee that you will get high-quality plastic parts that will help you beat the competition.
Internal gas assisted molding is more widely used than the external process, so we shall discuss it first. Initially, molten plastic resin enters the mold through spruce channels. Then, the gas enters through a nozzle and forms a bubble inside the molten resin. The pressure of the growing gas bubble forces the resin against the walls of the mold, giving the parts their shape.
The gas assisted injection molding process has two main types, external and internal. It also follows a specific workflow with three steps. In the following sections, we distinguish between the two types and explain the step-by-step procedure.
During the FAI process, we utilize the Cp/Cpk (Process Capability Analysis) method to assess the precision and consistency of the parts. By running our own sample lot and checking the primary dimensions of each sample injection molded part, we can determine the mold’s capability to produce parts that meet the desired specifications. Our target Cp/Cpk value is greater than 1.33, and we are proud that our regular results exceed this threshold, ranging from Cpk 2.5 to 3. This level of consistency assures our customers that each plastic part will be consistently produced with the utmost precision.
The manufacturing sector is one of the most innovative in today’s fast-paced world, setting new standards with each stride. Gas assisted injection molding is one such novel plastic manufacturing technique that offers great product quality.
Integrated Molding Solutions understands that precision and consistency require skilled operators who are well-versed in the intricacies of the molding process. To ensure that our team meets the highest standards of expertise, we provide comprehensive training programs for our employees. Through these programs, our operators receive in-depth knowledge about injection molding principles, machine operation, mold maintenance, and quality control procedures. We also offer opportunities for our employees to become certified operators, equipping them with the necessary skills and knowledge to handle complex molding projects with precision and efficiency. By investing in training, certification, and continuing education, we empower our team of industry veterans to deliver exceptional results and uphold the utmost precision in every aspect of our operations.
This process is well-known for its fine surface finish quality. Since the gas pressure acts uniformly on the non-aesthetic side, the opposite end tightly packs into the mold extremities, taking its exact shape. The resultant surface is so precise that it also includes fine textures and patterns of the mold. Consequently, external gas assisted molding is preferable if the part has surface patterns and imprints.
For your plastic parts, RapidDirect can help you become more competitive in your market through our specialized injection molding services!
Gas assist has several pros that make it the go-to technique for many manufacturers. Summarized below are all of its main advantages and disadvantages.
Tapping and threading make for easy disassembly. Both processes produce threads on a part. “Threads” means a small threadlike ridge or groove. Tapping and threading both create threaded surfaces. The threading process makes threads on the outside surface. Like a bolt or screw, for example. Similarly, tapping creates threads inside a hole, such as a nut. Threading is performed with a die tool, while tapping uses a tapping tool. When opposite features come together, the threads interlock.
External gas assisted injection molding is fundamentally different from the internal process. The gas does not penetrate the material to create hollow sections. Rather, it enters into the mold through microchannels from one side only. It packs the molten resin against the mold’s walls by applying pressure from the backside/non-aesthetic side of the part.
The extremely high level of precision needed within the aerospace industry makes CNC machining a suitable manufacturing process for the sector.
Mechanical fasteners have the distinct advantage of offering disassembly and reassembly. Components include screws, nuts, bolts, rivets, pins, and inserts are examples of mechanical fasteners. Tapping is a process used to place threading inside a plastic injection molded hole. Advantages mechanical fasteners provide are a stronger, longer-lasting bond, durability, and disassembly. When you need to ensure the strength of the hold, mechanical fasteners are likely the correct choice.
In addition to good surface quality, this technique also allows for thicker sections due to better packing and shrinkage-countering ability. Especially, for ribbed/boss features the rib/wall ratio can be up to 1, which is much better than some other methods. This lends strength and stability to the molded part.
Moreover, parts with large surfaces and curved profiles are tackled quite efficiently. The gas channels are in line with the entire surface, allowing the gas to apply pressure all over the wide surface area. As a result, manufacturing large surfaces is not a considerable issue.
Electronics are still a leading sector in the use of plastic resin parts. Plastics do not conduct electricity. Electronics often need plastics to insulate the electricity running through them. Consequently, a plastic part can make the perfect insulator for electronics and electrical devices. Plastics also have a lower conductivity for heat. Meaning, that plastics do not transfer heat well due to their insulating properties. This particular property works to the advantage of the plastics industry when it wishes to shield heat from other more delicate parts or the user. You may also treat plastics with special flame retardant finishing applications to further support their fire-resistant properties.
Electroplating or electro-deposition is a process whereby a metal material coats the surface of a part. In the electroplating process, a permanent bond connects the metal to the surface of another piece. The process involves an electrolyte or plating bath charged with electricity. The electricity-charged bath deposits small particles of the metal over the part’s surface. Therefore, this process effectively coats the plastic piece in a completely shiny, smooth metal finish.
Before proceeding to production, IMS experts conduct thorough tool verification and First Article Inspection (FAI). The toolmaker runs samples and ships them to IMS for evaluation. We measure the tolerances of these samples to ensure that the injection mold can consistently produce precision plastic parts within the given requirements. Once the customer approves the samples, the mold is shipped to our facility for FAI.
Now that you know about the ins and outs of gas assisted injection molding, it is time to know who does it best. RapidDirect is your best choice in injection molding services. Our ever-growing establishment boasts a talented team of professional engineers and technicians, supported by powerful manufacturing capabilities. For our esteemed clientele, we offer plastic manufacturing services in a wide variety of plastic materials.
A major advantage of this manufacturing technique is that it can handle a wide range of plastic materials. We will discuss below the main plastic materials compatible with this process.
This molten resin then enters the mold cavity. However, the resin injection mechanism does not fill up the mold since the product has hollow sections. The amount of injected resin material depends upon the volume of the part. It typically depends on geometrical factors like wall thickness, ribbed features, holes, etc. Usually, around ~70%-80% of the mold fills up with plastic material.
The resin melts due to external heating and friction while the constantly decreasing pitch of the screw compresses it to pressurize it. For gas assist molding, pressure is lower than conventional injection molding as there is less material to pack into the mold due to hollow sections. Also, since the pressure comes from gas rather than a thick, viscous liquid, there are lower viscosity-based frictional losses inside the pressurized media itself.
Cycle times are also significantly lower for internal gas assisted molding. Due to the geometries having hollow portions and thin cross-sections, they cool down quickly in comparison to solid parts.
From the very beginning of a project, IMS engineers identify the key parameters required to establish and maintain consistency throughout the manufacturing process. We adjust injection mold temperature, material temperature, injection speed, and injection pressure to optimize the mold cavity filling and ensure the parts come out exactly as intended and avoid pitfalls like sink or shrinkage. Our mastery of process control and material behavior allows us to minimize unnecessary post-processing requirements, such as trimming, and deliver high precision parts that meet the strictest tolerances. For necessary post-process treatments like assembly, painting, or fastening, IMS upholds our precision injection molding standards.
To provide customers with a clear understanding of the final product, IMS employs advanced 3D printing technology. Our precision 3D printers produce prototypes that closely resemble the actual model dimensions. This allows customers to visualize and test the part’s form, fit, and function before moving into production. In alignment with our goal of customer satisfaction, IMS utilizes the highest quality 3D printers to deliver prototypes with tight dimensional tolerance.
Precision is a crucial element in the world of manufacturing, and IMS engineers have the expertise to achieve precision consistently. When it comes to plastic injection molding, precision is often required for the form, fit, and function of a plastic product or part. At IMS, we specialize in precision injection molding, employing state-of-the-art technologies and our years of experience to deliver consistent, high-quality plastic parts. Our precision-focused approach includes design for manufacturing (DFM), tooling, production processes, and quality assurance and control.
GETTING A QUOTE WITH LK-MOULD IS FREE AND SIMPLE.
FIND MORE OF OUR SERVICES:
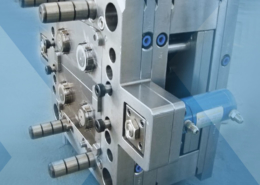
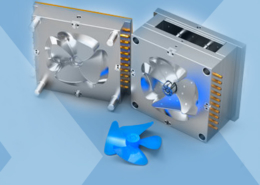
Plastic Molding

Rapid Prototyping
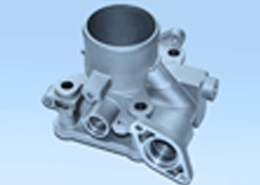
Pressure Die Casting
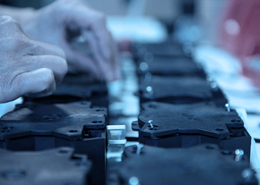
Parts Assembly
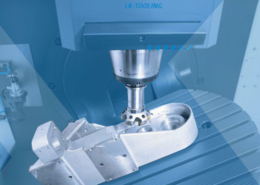