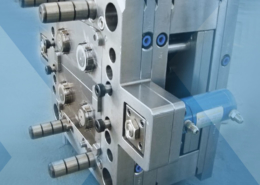
Jasa cetak plastik injection moulding - pembuatan moulding plastik
Author:gly Date: 2024-10-15
This goes to show that they can easily be recycled and reused for a different application. The ability to heat this plastic to its melting point, cool it, and reheat it again without degradation is an important aspect to most manufacturers and users. In most cases, when working with other types of plastic polymers you’ll find that when exposed to heat they tend to burn. However, when it comes to ABS plastics, all they do is change their state by liquefying which makes them an ideal option for injection molding.
The abs plastics have a high resistance to heat and chemical substances which makes them a great polymer option. They feature a low melting temperature which makes them ideal for manufacturing processes such as injection molding or 3D printing on an FDM machine.
When working with a drill and other power tools used in construction, you’ll find the use of plastic used to cover the inner mechanics. The plastic featured on these power tools is designed to be housing for them. This plastic is made to be strong to protect the power tools from any outside interference that could hinder performance. The plastic housing usually features the use of ABS plastic polymers in their construction.
In the manufacturing process, you’ll find that most will feature the addition of different products to help boost the performance of the plastic polymer being used. In the case of ABS plastics, mist manufacturers tend to work by adding fibers, especially fiberglass as their additive. This addition helps increase the strength of the product dramatically. Also, other additives may be introduced to increase heat resistance to as high as 80 ℃.
Dimensional Stability: HDPE 5000S exhibits low shrinkage (1.5%) and maintains its shape during cooling, contributing to the accurate and consistent production of precision parts.
Moderate Tensile Elongation: HDPE 7000F's tensile elongation of 500% balances flexibility and strength, making it suitable for products requiring a blend of both attributes. This property is advantageous for producing hoses, tubing, and flexible containers.
As a business, one of the most important aspects to cater to is the manufacturing of the products you’ll be using. This means you need to research and have a clear understanding of the processes that will be involved. One of the most used processes in the manufacture of different products is injection molding. It is an efficient option that ensures all your desired requirements are met. In injection molding, you’ll find ABS plastic molding as one of the most relied upon production processes. It is a process that is used by many injection molding manufacturers to ensure that the products being made are of the right standard. Learning more about ABS plastic molding will give you a great idea of what to expect when you approach your desired manufacturer. In this article, we’ll expound on ABS plastics, some of their properties, and also the process itself.
The ABS plastic polymer that is used in most plastic product manufacturing processes, undergoes a process of its own to make it a suitable option to use. ABS is commonly polymerized using a process mostly known as an emulsion. This process is used to refer to a situation where a mixture of multiple products is combined to make a single product. The uniqueness of this process is that the mixture involved features products that would typically not mix. The creation of ABS may also feature the use of the continuous mass polymerization process.
Balanced Strength and Flexibility: HDPE 5000S combines a commendable tensile strength of 30 MPa with a high elongation of 600%, rendering it suitable for manufacturing durable yet flexible products.
The ABS plastic polymers are used in the manufacture of specific plastic products used in different applications. Given the strength and endurance exhibited by this polymer, you’ll find them used in products that need such properties. For instance, some of the products where the use of ABS plastic polymers is featured include:
In the injection molding process, different types of plastics may be featured to achieve a certain plastic product. ABS plastics is one of the few choices that is preferred by different manufacturers who are focused on providing quality to all their customers. The ABS plastic is a short abbreviation of the name acrylonitrile butadiene styrene. This plastic is an opaque thermoplastic and amorphous polymer greatly used in the plastic manufacturing industry. The ABS plastics come in handy seeing they are thermoplastic and are responsive to the effects of heat. This means that at a certain degree of the heat applied, the ABS plastic will melt and can easily be manipulated and shaped into a different product.
Elevated Heat Deflection: HDPE 6000F's heat deflection temperature of 90°C makes it suitable for applications that face moderate thermal challenges. It is employed in crafting items like automotive interior parts, kitchen utensils, and electrical components that withstand elevated temperatures without deformation.
Given the properties we have just discussed, it is clear that working with ABS plastic polymers is the best way to go especially for injection molding. However, the properties featured by these plastics are not the only reason why they are preferred by most manufacturers. The other reason is the fact that these plastic polymers are relatively inexpensive making them quite pocket-friendly to both customers and manufacturers. Given that the ABS plastic polymers are made by recycling products made of the same, you find that the prices are much lower. This makes the ABS plastics a better and more quality option to use for the price invested in the plastic polymer.
When ABS plastics are molded at high temperatures, they produce higher gloss and heat resistance. However, on the other hand, when molded at lower temperatures they tend to improve their resistance and load strength resulting in better-finished products.
Enhanced Stiffness: Boasting a flexural modulus of 1300 MPa, HDPE 7000F excels in applications that demand stiffness and structural integrity. It is ideal for creating items like furniture, automotive components, and machinery parts where robustness is essential.
If you have ever had the chance to play with the LEGO toys and build a tower with them, you’ll have realized the properties they feature. LEGO toys are plastic and feature a great deal of strength which makes them hard to destroy. They additionally are durable and last a long time. They are also made in different colors to make the game more exciting. The plastic polymer used in the manufacture of the LEGO toys is ABS.
Superior Impact Strength: With an Izod impact strength of 50 J/m, HDPE 8000F ensures exceptional resilience against impacts and shocks. It finds relevance in creating challenging and durable items like tool cases, industrial bins, and protective equipment.
Optimized Heat Deflection: With a heat deflection temperature of 85°C, HDPE 5000S is apt for applications with elevated temperatures. It produces kitchenware, automotive components, and products exposed to moderate heat sources.
High-Density Polyethylene (HDPE) is a thermoplastic polymer known for its high strength-to-density ratio. It's produced from petroleum and exhibits excellent resistance to chemicals, impact, and moisture, making it suitable for various applications, including packaging, pipes, and injection-molded products.
Low Shrinkage and Dimensional Accuracy: HDPE 8000F's low shrinkage rate of 0.8% enhances its ability to maintain precise dimensions during cooling.
When it comes to choosing a plastic polymer that is perfect for machining especially with a process such as injection molding, this is the best for you. ABS plastics feature a great deal of versatility that allows them to easily take shape when in the manufacturing process.
High Molecular Weight: With an elevated molecular weight, HDPE 7000F offers improved mechanical properties and durability. It finds application in crafting industrial components, tanks, and agricultural equipment that require enduring performance under demanding conditions.
The keys featured on the computer keyboards are most commonly made of ABS plastic polymers. They are made to feature strength and stay durable while still offering quality service to their users.
Most wall sockets used to switch on and off the supply of electricity will usually feature the use of a plastic faceguard. This plastic housing just like that on the power tools is used to ensure that the mechanics of the socket are not interfered with. The plastic face guard also acts as a great finishing piece for aesthetics. The plastic used in these plastics is the ABS plastic polymer.
However, unlike the emulsion process, this particular option is not commonly used seeing as it is a patented process. One thing to note here is that during the emulsion process, you’ll have to use products that feature abs properties. Given that ABS is a thermoplastic, the products used should also feature the same qualities. It’s mostly like recycling products made of ABS plastic to make more ABS polymers.
Diverse Industrial Applications: HDPE 7000F's combination of properties makes it versatile for various industrial applications. It is used to craft large storage containers, material handling equipment, and industrial machinery components that withstand heavy loads and harsh environments.
Balanced Impact Resistance: An Izod impact strength of 35 J/m ensures robust resistance to impacts and shocks. This property is ideal for crafting items like safety equipment, consumer goods, and housings for power tools.
Elevated Heat Deflection: Featuring a heat deflection temperature of 100°C, HDPE 8000F is ideal for applications subjected to higher temperatures. It produces parts for automotive engine compartments, outdoor fixtures, and products with moderate heat exposure.
Enhanced Flow: HDPE 6000F's improved melt flow characteristics make it a prime choice for manufacturing intricate components with complex geometries. Its versatility applies to applications like thin-walled parts, including intricate automotive components and electronic enclosures.
ABS plastics feature a few properties that make them the go-to plastic polymer of choice for most manufacturers. These properties come in handy in ensuring that all the products made are of the highest quality and that they meet the customer’s needs. Some of the properties to consider include:
Mechanical Strength: With a tensile strength of 27 MPa and a flexural strength of 45 MPa, HDPE 6000F offers solid mechanical performance. It's an excellent fit for creating industrial components, agricultural equipment, and structural parts that demand a blend of strength and reliability.
High-Performance Polymer: HDPE 8000F stands out as a high-performance grade, primarily due to its excellent stress crack resistance. This property makes it an optimal choice for manufacturing chemical containers, outdoor equipment, and products exposed to challenging environments.
Excellent Impact Resistance: This grade's Izod impact strength of 30 J/m ensures resilience against impacts and shocks. It finds relevance in creating toys, household items, and industrial components that require impact resistance to withstand rough handling or accidental drops.
ABS plastic molding is a process where ABS plastic polymers are used in the injection molding process. These polymers are used to manufacture different plastic products like power tool housings and lego toys among others. They feature amazing properties that make them the go-to plastic of choice for most injection molding manufacturers. As a business, if you want to have your plastic products made using the injection process, ABS plastic polymers will come in handy for you.
GETTING A QUOTE WITH LK-MOULD IS FREE AND SIMPLE.
FIND MORE OF OUR SERVICES:
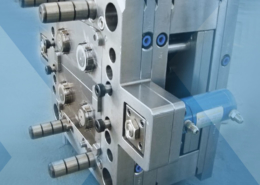
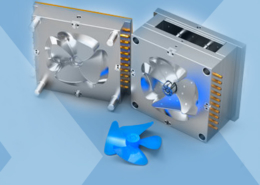
Plastic Molding

Rapid Prototyping
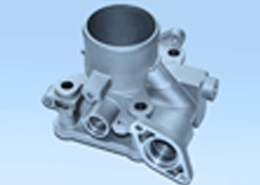
Pressure Die Casting
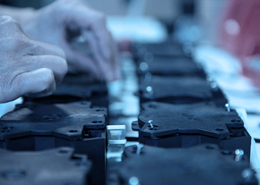
Parts Assembly
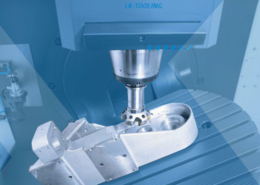