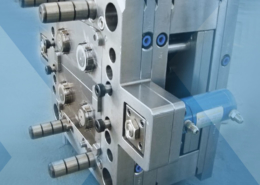
Exploring Benchtop Injection Molding: Revolutionizing Small-Scale Manufacturing
Author:gly Date: 2024-06-08
In recent years, benchtop injection molding has emerged as a disruptive technology, revolutionizing small-scale manufacturing processes. This compact yet powerful method offers unprecedented flexibility and efficiency, enabling businesses and hobbyists alike to produce high-quality plastic components with remarkable ease. Delving into the intricacies of benchtop injection molding unveils a world of innovation and potential, promising to reshape the landscape of production across various industries.
Understanding Benchtop Injection Molding
Benchtop injection molding refers to the process of injecting molten plastic material into a mold cavity, typically at a small-scale workstation or tabletop setup. Unlike traditional industrial injection molding, which requires substantial infrastructure and capital investment, benchtop molding systems are compact, affordable, and user-friendly. This democratization of the molding process has democratized access to manufacturing capabilities, empowering entrepreneurs, designers, and educators to bring their ideas to life with unprecedented speed and efficiency.
The Advantages of Benchtop Injection Molding
The allure of benchtop injection molding lies in its myriad advantages. Firstly, its compact size and affordability make it accessible to a wide range of users, from small businesses and startups to educational institutions and hobbyists. Additionally, its versatility enables rapid prototyping and iterative design, allowing for quick modifications and adjustments without the need for expensive tooling. Moreover, benchtop molding systems boast impressive precision and repeatability, ensuring consistent quality across batches. These advantages collectively contribute to its growing popularity and widespread adoption across diverse sectors.
Technology and Innovation in Benchtop Molding
Behind the scenes, benchtop injection molding systems incorporate advanced technology and innovative features to streamline the manufacturing process. From intuitive software interfaces for mold design and simulation to precision control systems for temperature and pressure regulation, these systems embody the latest advancements in engineering and materials science. Furthermore, ongoing research and development efforts continue to push the boundaries of benchtop molding capabilities, with improvements in material compatibility, mold complexity, and production efficiency driving further innovation in the field.
Applications of Benchtop Injection Molding
The versatility of benchtop injection molding extends to its wide-ranging applications across various industries and sectors. From rapid prototyping and small-scale production to educational demonstrations and artisanal crafting, its adaptability knows no bounds.
Industrial Prototyping and Production
In industrial settings, benchtop injection molding serves as a valuable tool for prototyping new products and components. Its ability to quickly produce high-quality plastic parts allows engineers and designers to iterate designs rapidly, accelerating the product development cycle and reducing time-to-market. Moreover, for small-batch production runs or niche markets, benchtop molding offers a cost-effective alternative to traditional manufacturing methods, enabling agile and responsive production processes.
Educational Training and Skill Development
In educational environments, benchtop injection molding plays a crucial role in teaching students about the principles of manufacturing and design. By providing hands-on experience with real-world production processes, educators can impart practical skills and knowledge that are highly sought after in the industry. Additionally, the accessibility and affordability of benchtop molding systems make them ideal for educational institutions with limited resources, ensuring that students from diverse backgrounds have the opportunity to engage with advanced manufacturing technologies.
Artisanal and Customized Production
Beyond industrial and educational applications, benchtop injection molding has found a niche in artisanal and customized production. Craftsmen and hobbyists leverage its capabilities to create bespoke plastic components for a wide range of applications, from jewelry and accessories to specialty tools and gadgets. The ability to produce small quantities of custom parts on demand empowers artisans to explore creative designs and cater to niche markets, fostering a culture of innovation and individuality in manufacturing.
Challenges and Future Directions
Despite its many benefits, benchtop injection molding is not without its challenges. From material selection and mold design to process optimization and quality control, users must navigate various complexities to achieve optimal results. Additionally, as demand for benchtop molding systems continues to grow, addressing issues such as sustainability, waste management, and environmental impact becomes increasingly important.
Looking ahead, ongoing research and development efforts aim to address these challenges and unlock new opportunities for benchtop injection molding. Advancements in materials science, automation technology, and digital manufacturing hold the potential to further enhance the capabilities and accessibility of benchtop molding systems. Moreover, collaborations between academia, industry, and government entities can facilitate knowledge sharing and technology transfer, driving innovation and sustainability in the field of small-scale manufacturing.
Conclusion
In conclusion, benchtop injection molding represents a transformative technology with far-reaching implications for small-scale manufacturing. Its accessibility, versatility, and efficiency have democratized the production process, empowering individuals and businesses to innovate and create with unprecedented freedom. By understanding the intricacies of benchtop molding and exploring its diverse applications, we can harness its full potential to shape the future of manufacturing in a sustainable and inclusive manner. As we embark on this journey of discovery and innovation, let us embrace the opportunities that benchtop injection molding presents and strive to realize its promise of a more agile, efficient, and creative manufacturing ecosystem.
GETTING A QUOTE WITH LK-MOULD IS FREE AND SIMPLE.
FIND MORE OF OUR SERVICES:
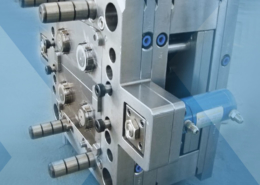
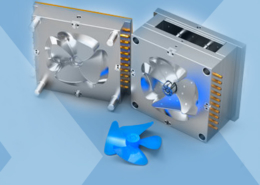
Plastic Molding

Rapid Prototyping
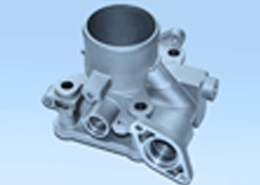
Pressure Die Casting
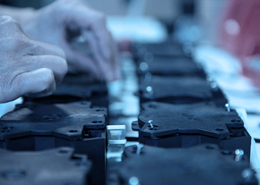
Parts Assembly
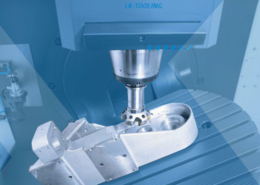