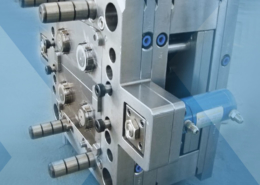
Exploring Back Injection Molding: Revolutionizing Plastic Component Manufacturin
Author:gly Date: 2024-06-08
Introduction
Back injection molding stands at the forefront of innovation in plastic component manufacturing, offering unparalleled versatility, efficiency, and design possibilities. This advanced technique involves injecting a thermoplastic material into a preformed cavity or substrate, enabling the creation of complex, multi-material, and highly functional parts. As industries continue to demand lighter, stronger, and more intricate components, back injection molding emerges as a transformative solution. In this article, we delve into the intricacies of back injection molding, exploring its mechanisms, applications, advantages, challenges, and future prospects.
Mechanisms of Back Injection Molding
Injection Process
The process of back injection molding begins with the preparation of the substrate or preformed cavity, which serves as the foundation for the final part. The thermoplastic material, typically in pellet form, is heated to a molten state within the injection molding machine. Once at optimal temperature and viscosity, the molten material is injected into the cavity, where it conforms to the desired shape and bonds with the substrate.
Material Compatibility
Back injection molding offers remarkable versatility in material selection, allowing manufacturers to combine different thermoplastics or incorporate additives to achieve specific properties. This compatibility with various materials enables the production of hybrid components with enhanced strength, flexibility, or aesthetic appeal. Common materials used in back injection molding include polypropylene (PP), thermoplastic elastomers (TPE), and acrylonitrile butadiene styrene (ABS).
Tooling Design
The design of molds and tooling plays a critical role in the success of back injection molding projects. Complex geometries, overmolding configurations, and precise part tolerances require meticulous attention during the tooling design phase. Advanced CAD/CAM software and additive manufacturing technologies facilitate the creation of intricate molds, optimizing part quality and production efficiency.
Applications of Back Injection Molding
Automotive Industry
In the automotive sector, back injection molding is widely employed for the production of interior and exterior components. From dashboard panels and door handles to grille inserts and taillight housings, back injection molding enables manufacturers to achieve lightweight, durable, and aesthetically pleasing parts. The ability to integrate functional features, such as clips, snaps, and gaskets, further enhances the performance and assembly of automotive components.
Consumer Electronics
The consumer electronics industry relies on back injection molding to create sleek and ergonomic product designs. Smartphone cases, remote control housings, and wearable device components benefit from the precision and customization offered by this manufacturing process. With the growing demand for wear-resistant and impact-absorbing materials, back injection molding enables manufacturers to meet the stringent requirements of modern electronic devices.
Medical Devices
Back injection molding plays a vital role in the production of medical devices and equipment, where biocompatibility, sterilizability, and precision are paramount. Surgical instruments, drug delivery devices, and diagnostic equipment leverage the versatility of this process to integrate features such as ergonomic grips, fluid channels, and patient-specific customization. By utilizing medical-grade materials and adhering to stringent quality standards, back injection molding ensures the reliability and safety of critical healthcare products.
Advantages and Challenges
Advantages
Design Freedom
: Back injection molding enables the creation of complex geometries and multi-material components, expanding design possibilities.
Cost Efficiency
: The ability to consolidate multiple manufacturing steps reduces production time and labor costs.
Improved Performance
: By integrating different materials, manufacturers can enhance part strength, flexibility, and functionality.
Challenges
Tooling Complexity
: Designing and fabricating molds for back injection molding can be time-consuming and costly, particularly for intricate geometries.
Material Compatibility
: Ensuring compatibility between substrate materials and injected thermoplastics is essential to avoid bonding issues or part defects.
Quality Control
: Maintaining consistent part quality and dimensional accuracy requires robust process monitoring and quality assurance protocols.
Conclusion
Back injection molding represents a paradigm shift in plastic component manufacturing, offering unprecedented flexibility, efficiency, and performance. From automotive and electronics to medical and consumer goods, this innovative process continues to drive advancements in product design, functionality, and sustainability. As industries evolve and demand for customized, high-performance components grows, back injection molding will remain at the forefront of technological innovation, shaping the future of manufacturing.
Through ongoing research, development, and collaboration across disciplines, the potential of back injection molding can be further unlocked, opening new avenues for material innovation, process optimization, and application diversification. Embracing this transformative technology and investing in its continued advancement will empower manufacturers to meet the evolving needs of global markets while pushing the boundaries of design creativity and functional excellence.
GETTING A QUOTE WITH LK-MOULD IS FREE AND SIMPLE.
FIND MORE OF OUR SERVICES:
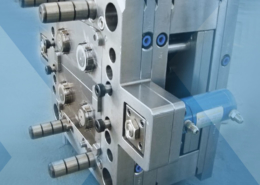
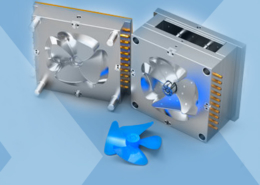
Plastic Molding

Rapid Prototyping
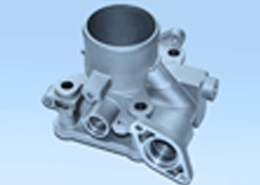
Pressure Die Casting
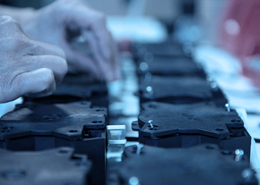
Parts Assembly
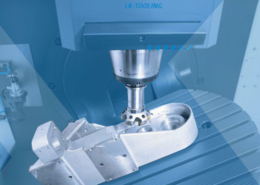