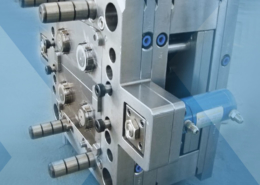
Injection Moulding Design Guide - plastic injection part
Author:gly Date: 2024-10-15
We offer specialized medical molding services to produce high-precision, sterile components for the healthcare industry. Our Class 8 Clean Room ensures that all medical parts are manufactured in a controlled, contamination-free environment. This guarantees the highest standards of cleanliness and compliance with medical regulations.
We view our clients as partners and are dedicated to supporting your success from concept to completion. Our experienced team is available to assist with design, prototyping, production, and post-production services. This end-to-end support ensures a smooth and successful project execution, allowing you to focus on your core business objectives.
Knowing about the injection molding cost can help in optimizing the manufacturing process. This is achievable by understanding different factors and elements, and this article discussed everything you need to know about costs in injection molding and how to use it. Looking for a quality-focused injection molding service provider? At RapidDirect, we offer the best at a competitive price.
While high-performance plastics may offer specific advantages, they often come with a higher price tag. Analyzing the functional requirements of the part and selecting a cost-effective material that meets those needs can lead to substantial cost savings without compromising quality.
We understand the importance of speed in bringing new products to market. Our quick-turn tooling services enable us to deliver parts within a month after placing an order. This rapid turnaround time allows you to accelerate your product development cycles and respond swiftly to market demands, giving you a competitive edge.
Optimize gate locations to ensure uniform filling and minimize defects. For example, placing the gate at the thickest section of a part helps ensure proper material flow and reduces the risk of sink marks.
Yes, we have the capability to manage both small quantity prototypes and large-scale production runs. Our flexible manufacturing processes ensure high-quality production regardless of the order size.
The choice of mold material influences both the upfront investment and the overall efficiency of the manufacturing process. Mold materials vary in cost and durability, with aluminum and 3D-printed molds offering lower upfront expenses suitable for low-volume production.
Insert molding involves placing pre-formed components or inserts into the mold before injection. This technique allows for the integration of multiple parts into a single molding process, reducing the need for additional assembly steps. Naturally, a single-step process would mean a lower machine run-time and a lower number of repetitions and cycles. Furthermore, you won’t be assembling separately designed parts together as well and that again would save time. By consolidating manufacturing steps, insert molding can lead to time and cost savings.
Despite this, the overall manufacturing cost decreases as production scales up. Hence, plastic injection molding is widely considered a cost-effective solution for mass-producing plastic parts, with the price per part decreasing as quantities increase.
We adhere to strict quality control processes, including comprehensive testing and inspection at various stages of production. Our commitment to quality ensures that each part meets your exact specifications and industry standards.
There are several best practices to minimize injection molding costs without compromising quality. By strategically implementing these practices, businesses can achieve cost-effective production and enhance overall efficiency.
Recognizing the fluctuating nature of pricing and the vital role injection molding cost estimates play in projects, we have crafted an illustrative example to help better understand the cost estimation process.
This category necessitates a straightforward mold, often crafted from cost-effective materials like aluminum or 3D-printed materials. Additionally, it requires minimal raw materials and less advanced machinery, resulting in an overall low injection molding cost. However, the cost per unit part tends to be higher in low-volume production scenarios.
Maintain uniform wall thickness to prevent defects such as warping and sink marks. For example, designing a plastic enclosure with consistent wall thickness ensures even cooling and material flow.
Design for Manufacturing (DFM) for injection molding involves optimizing the design of parts to improve manufacturability, reduce costs, and enhance quality. By integrating DFM principles, we ensure your designs are ready for efficient and effective injection molding production.
The equipment used in the molding process is unique. The cost of a machine depends on the size and its level of sophistication (often measured in terms of automation), and it ranges from $10000 (small) or less suitable for low-volume injection molding to $200,000 (large) suitable for high-volume injection molding. Medium molding machines ($50,000 or more) can also be tailored for medium-level molding. Also, you need to consider the following types of injection molding machines and how they affect the cost:
At Aprios, we specialize in precision plastics for mission-critical parts, focusing on creating components where lives may be on the line, such as medical devices and safety equipment. We understand the gravity of plastic manufacturing for applications where failure is not an option, ensuring our plastic molding products meet the standards of accuracy, reliability, and performance. Our quality control processes and plastic molding techniques ensure that every part we produce is flawless, making us the ideal choice for high-stakes plastic manufacturing that requires dependability, rather than commodities like plastic spoons.
The overmolding process enhances the functionality and aesthetics of a product by combining different materials, such as a rigid plastic with a soft-touch surface. Insert molding integrates metal or plastic inserts into the molded parts, increasing strength and functionality, and is ideal for creating complex assemblies.
Conduct mold flow analysis to predict and address potential issues such as air traps, weld lines, or hotspots. For example, simulating the injection process for a complex part can help optimize gate locations and cooling channels.
We can work with a wide range of thermoplastic materials, including ABS, polycarbonate, polyethylene, polypropylene, and more. We select materials based on your specific application requirements, such as strength, flexibility, and temperature resistance. We do not work with PVC or Teflon.
By incorporating these considerations into your design, we ensure a more efficient injection molding process, leading to high-quality, cost-effective parts.
In contrast, simpler mold designs with fewer complex features result in lower tooling costs, making them a more cost-effective choice, especially for applications where intricate features are not essential. Striking a balance between design requirements and cost considerations is essential in optimizing injection molding expenses.
If you want to produce high-quality machined parts with a sleek appearance, it’s essential to consider some critical factors related to CNC machining.
Beyond molding, we provide comprehensive post-processing and assembly services. Our secondary operations include machining, bonding, and finishing, ensuring that your parts are ready for immediate use. We can also offer assembly and packaging in our Class 8 Clean Room, maintaining the highest standards of cleanliness and quality.
Quality injection molded parts and a cost-effective process are achievable by trusting the right injection molding services. At RapidDirect, we offer custom plastic injection molding services to help you make different plastic prototypes or real parts based on your requirements.
Streamlined tool designs contribute to shorter cycle times in the molding process, enhancing production efficiency and reducing manufacturing costs. They also minimize material waste by lowering rejection rates and decreasing scrap material. Additionally, simpler molds are easier to maintain, which prolongs their lifespan and lessens the frequency and costs of repairs and replacements.
The tooling cost incurred during injection molding depends on the machining process used in making the mold, the material used, mold complexity, and mold cavity size.
Injection molding costs are a focal point for plastic product manufacturers utilizing this process. This article delves into the intricacies of injection molding costs, shedding light on various factors that contribute to the overall expense. By unraveling these elements, you can gain valuable insights into optimizing costs for your specific project.
This approach simplifies the mold design, leading to lower manufacturing costs as complex molds are more expensive to produce. Furthermore, reducing part complexity translates to decreased material usage, offering direct savings. Additionally, simpler designs can shorten the molding cycle, boosting productivity and cutting down on labor and energy expenses. This also results in molds that are less demanding in terms of maintenance. Importantly, such streamlined designs often yield parts with improved structural integrity and consistent quality, reducing the likelihood of defects.
This will require a strong injection mold made from steel due to its long life expectancy, many materials, and, if possible, a sophisticated machine. This should increase the injection molding cost. However, the high cost will be distributed among the parts, reducing the cost per part manufactured. It is important to note that there is a higher cost distribution per part in high-volume production than in medium-volume production. As a result, they have a lower cost per part manufactured.
Please navigate to our online quotation platform and upload an injection molding CAD file to get a quick quotation. Our quotation process is comprehensive from start to finish and involves configuring different materials, finishes, quantities, etc. Furthermore, we will confirm the DFM analysis of the mold so that you get the most accurate part possible.
A well-designed part can reduce material usage, simplify mold design, and shorten cycle times, all of which lower manufacturing expenses. Optimizing wall thickness, incorporating uniformity, and minimizing undercuts can lead to more efficient production processes and less material waste. Conversely, complex geometries and poor DFM can lead to increased tooling adjustments, higher defect rates, and prolonged production cycles.
Minimize or eliminate undercuts to simplify mold design and reduce tooling costs. For instance, redesigning a part to avoid internal undercuts can eliminate the need for side actions in the mold.
Complex designs often require intricate molds with finer details, increasing initial tooling expenses. They may also necessitate advanced machinery and tighter tolerances, leading to higher operational costs and longer production times. Complex plastic molded parts often result in increased cycle times due to additional cooling and setting requirements, reducing overall manufacturing efficiency. Furthermore, the potential for defects rises with complexity, leading to higher rates of waste and rework.
We adhere to stringent quality assurance protocols and comply with industry standards to ensure the reliability of every part we produce. Our comprehensive testing and inspection processes guarantee that each component meets your exact specifications. For more information, please visit our Quality page. This commitment to quality reduces the risk of defects and enhances the overall performance of your products.
Larger parts require more material, leading to higher raw material expenses. They also necessitate bigger, more energy-consuming machines with longer cycle times, reducing production efficiency. As part size increases, maintaining precision becomes more challenging, possibly requiring advanced, costlier processes. Additionally, larger parts can produce more waste, especially in the runner system where excess material is generated, further elevating costs.
Part packaging costs depend on whether the packaging is consumer-facing (i.e., recognizable and short-span) or more costly shipping packaging. Consumer-facing packaging is suitable for products that are ready to use. However, larger manufacturers can use automatic packaging, which reduces damage and incurs fewer errors.
Surface finishing includes processes such as annealing, sandblasting, powder coating, etc., in which the part is subjected to increase its aesthetic appeal or functionality. They are separate from the injection molding process itself. However, many service providers will give a discount to clients using them for both injection molding and surface finishing. Also, there are secondary services which can be manufacturing processes(e.g., machining and drilling), assembly services (e.g., sonic welding), and decorating (e.g., pad printing), which can increase the injection molding cost.
Our injection molding services cater to a wide range of needs, from small quantity prototypes to full-scale production. Whether you need a few test pieces or millions of units, we have the capability to meet your demands efficiently. Our flexible production processes ensure that you receive high-quality parts on time, every time.
Incorporate appropriate draft angles (typically 1-2 degrees) on vertical surfaces to facilitate easy ejection from the mold. For instance, adding a slight taper to the sides of a plastic cup makes it easier to remove from the mold.
Maximizing the lifespan of molds is a cost-effective approach in injection molding. Reusing molds for multiple production runs helps distribute tooling costs across a larger production volume, reducing the per-part cost. Regular maintenance and careful handling of molds can extend their life, providing long-term cost benefits for manufacturers.
In some applications, the cosmetic appearance of a part may not be critical to its functionality. Choosing to forego intricate cosmetic details can result in faster production cycles and reduced tooling complexity, ultimately contributing to lower costs. This practice is particularly relevant for parts where aesthetics are secondary to functionality.
We can handle parts with surface areas up to 156 square inches in the direction of the mold clamp. Specific dimensions like 10x15 or 12x13, and shot weights up to 61 ounces (3.8 pounds), are within our capacity.
Insert molding integrates metal or plastic inserts into the molded parts during the injection process. This technique enhances the strength and functionality of components, making it perfect for complex assemblies. Our expertise in insert molding allows us to produce parts with embedded reinforcements, electrical components, or threaded inserts with precision.
Micro injection molding is a technique for producing tiny and precise components using minimal resin volumes in the injection procedure. Our expertise in micro injection molding allows us to create intricate parts with high accuracy, perfect for industries such as medical devices, electronics, and automotive components.
On the other hand, smaller mold cavities are generally more cost-effective due to reduced material usage and simpler mold construction. The choice of mold cavity size should align with production requirements, as optimizing for the right balance between cavity size and part dimensions can result in cost savings in both material consumption and tooling expenses.
Choose materials that are suitable for injection molding and meet your product's performance requirements. For instance, selecting a high-impact resin for a component that will experience significant wear and tear.
Determining whether injection molding is expensive isn’t a straightforward answer. While the process proves cost-effective for mass production of plastic parts, the initial setup costs can be substantial due to high machine prices.
More complex molds, characterized by intricate features, undercuts, or intricate geometries, generally involve higher tooling costs due to increased manufacturing complexity. These molds require specialized machining and longer production times, contributing to elevated upfront expenses.
Larger mold cavities, capable of accommodating higher material volumes and producing more significant parts in each cycle, typically necessitate more substantial and, consequently, costlier molds.
To effectively reduce unnecessary features, a thorough design review is essential, focusing on optimizing part geometry for both functionality and manufacturability. This might involve reevaluating the necessity of certain aesthetic elements, consolidating multiple components into a single, more efficient design, or modifying part dimensions to eliminate redundant or non-critical aspects. The goal is to achieve an optimal balance between the part’s functional requirements and the cost-effectiveness of its production.
Use ribs and gussets to add strength without increasing wall thickness. For example, adding ribs to a plastic panel increases rigidity while keeping the part lightweight.
We have several plastic materials chosen using a stringent and streamlined selection process and an engineering team that can provide professional design suggestions and material selection. Our highly sophisticated manufacturing capabilities and network allow us to ensure high-quality molds and plastic parts. Upload your design today and get instant quotes and free DfM analysis at a competitive price.
Selecting specific materials, such as high-performance plastics, often results in increased expenses. However, optimizing designs and manufacturing processes to reduce material wastage can significantly lower overall costs. While incorporating recyclable materials might lead to a modest increase in initial expenses, it paves the way for more sustainable practices and could prove economically beneficial over time.
In contrast, high-volume production often demands molds made from robust materials like steel, incurring a higher initial cost but providing extended tool life and minimizing the cost per unit produced. The selection of mold material, therefore, becomes a strategic decision balancing short-term expenditure with long-term efficiency and cost-effectiveness in injection molding operations.
Our Design for Manufacturing (DFM) services help you optimize your designs for efficient and cost-effective production. By collaborating early in the design process, we identify potential issues and suggest improvements to enhance manufacturability. This proactive approach reduces time-to-market, lowers production costs, and ensures that your products are designed with manufacturing efficiency in mind.
The production volume affects the amount of raw injection molding material required, the sophistication of the injection molding machine, and the injection mold’s strength/durability/other mechanical properties. The volume of production is divided into three major categories:
The extremely high level of precision needed within the aerospace industry makes CNC machining a suitable manufacturing process for the sector.
Part inspection costs can be specialized or standard. On the one hand, standard inspection is an internal process that requires trained personnel to check for part defects (cosmetic or critical) and a quality verification team to identify the probable cause. On the other hand, specialized inspection involves inviting specialized engineers to inspect the product. Thus, specialized certification costs more, and sometimes injection service providers offer the certification at a cost.
We have a defined project management and quality assurance process for intaking tools from other manufacturers. Our team can repair and modify existing tools to get your production back on track quickly. With our expertise, we ensure a smooth transition and minimal disruption to your manufacturing process.
To simplify mold designs, it’s crucial to eliminate unnecessary features, optimize part geometry, and consider using standardized components. Utilizing CAD and CAM tools can help in identifying and removing superfluous elements, ensuring efficient mold design without compromising product quality.
Note: not all parts will require surface finishing or other secondary services. As a result, you should ensure you need such services to increase overall production efficiency and less material wastage.
Several factors directly impact your costs, and understanding these key elements is crucial for optimizing your project’s financial aspect.
Our overmolding process allows us to combine multiple materials into a single component, enhancing functionality and performance. This process is ideal for creating ergonomic designs and improving the durability of parts. We use cutting-edge technology to ensure a seamless bond between materials, resulting in superior end products.
Instead of buying a machine, businesses outsource their project to injection molding service providers. So they no longer incur the heavy cost of purchasing the machine but are subject to the service provider’s service cost.
GETTING A QUOTE WITH LK-MOULD IS FREE AND SIMPLE.
FIND MORE OF OUR SERVICES:
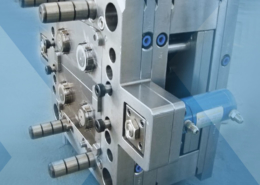
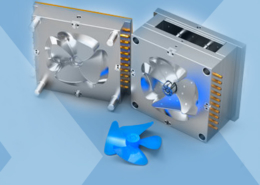
Plastic Molding

Rapid Prototyping
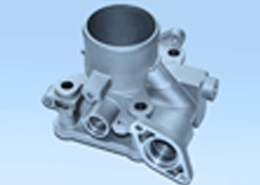
Pressure Die Casting
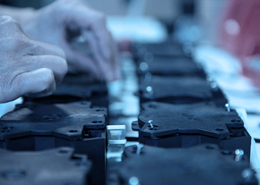
Parts Assembly
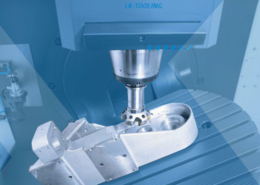