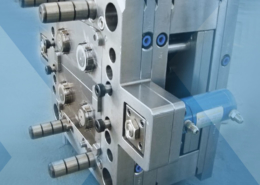
Injection Moulding Businesses for Sale - plastic injection molding business for
Author:gly Date: 2024-10-15
As with any plastic material, there are some common issues that could potentially arise in the PMMA thermoplastic molding process. Some of the problems that could occur include:
Poly(methyl methacrylate), also known as acrylic, is a clear thermoplastic homopolymer often used as a more resistant alternative to glass. Acrylic is the most common type of clear, moldable plastic available to the general public, and it can be used for anything from windows and picture frames to fake nails and paint.
Myriad considerations go into the final decision. It requires input from an experienced injection molding partner such as Kaysun, and guidance like that which you'll find in our white paper, Processing High-Temperature and Engineered-Grade Resins. Click the button below to download your copy of this valuable resource now.
The chemical properties of acrylic allow it to be completely transparent while remaining hard and highly resistant to scratches and impact. Acrylic can be easily molded into different shapes and sizes, meaning it can be an economic substitute for other types of hard plastic. The professional molding experts at Retlaw Industries can use acrylic material for your specific molded plastic part.
When you need professionally-manufactured plastic idler pulleys, sprockets, rebar chairs, or custom-made parts made for your business, Retlaw Industries can help. Our certified plastic part manufacturers build OEM parts to your exact specifications. Whether you want acrylic or any other type of composite plastic for your custom part, Retlaw has the capabilities to ensure you succeed.
From OEM parts to custom projects, Retlaw Industries has the capability and resources to deliver impressive results. We work with companies across the nation including within these great states: Colorado, Illinois, Indiana, Michigan, Minnesota, New York, Ohio, Pennsylvania, Washington, Wisconsin, and others!
Mention “high-temperature thermoplastic” and chances are that polyether ether ketone (PEEK) comes to mind. Its high heat tolerance, mechanical strength, and chemical resistance make PEEK resin ideal for many demanding applications including those in the automotive, electronics, aerospace, medical, and other markets. But is it the only choice?
In short, Tg correlates to the temperature at which a solid, glassy polymer transitions to a viscous, pliable state. Tm refers to the temperature at which the structured molecules of crystalline polymers become random chains of molecules (or, amorphous) — essentially, the thermoplastic begins to melt.
PEEK material falls within the family of semicrystalline thermoplastics known as Polyaryletherketones (PAEK). Polymers within the PAEK plastics classification all have high-temperature stability and excellent mechanical strength. Key differences appear in the temperatures at which the polymers’ textures change — the glass transition temperature (Tg) and melt temperature (Tm).
The Tg and Tm temperatures of PAEK plastics don’t vary greatly, yet even the seemingly minor differences can impact critical properties of an injection-molded part, including:
Typically, high-temperature resins can be run on conventional injection molding equipment — with one important caveat. The tooling used with PAEK materials must be able to achieve and withstand high temperatures (at least 165℃) in order to process unreinforced and reinforced PEEK, PEK, PEEKK, and other PAEK materials at processing melt temperatures generally ranging from 370℃ to 410℃.
While not directly related to tool design, it’s important to note injection molding at elevated temperatures is particularly susceptible to moisture. Materials must be completely dry prior to processing or failure could occur even when the most accurate tools are used.
For complex applications, there are rarely any easy solutions — and that includes identifying a high-temperature thermoplastic and maximizing its use during injection molding.
To ensure consistent, defect-free part production using high-heat resins, tooling design must address several key factors:
Acrylic is one of the most affordable plastics available to the general public. Its impact-resistant structure makes it one of the most useful plastics for a wide variety of applications, including where clear, impact-resistant material is needed. If you want your specific molded plastic part to be manufactured with acrylic resin, contact us for a quote. We'll always make sure your chosen plastic is the best material for the job.
GETTING A QUOTE WITH LK-MOULD IS FREE AND SIMPLE.
FIND MORE OF OUR SERVICES:
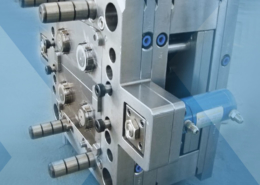
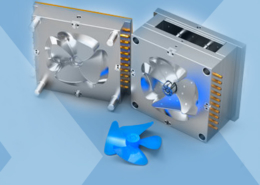
Plastic Molding

Rapid Prototyping
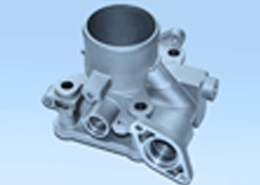
Pressure Die Casting
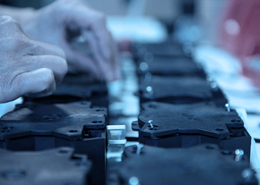
Parts Assembly
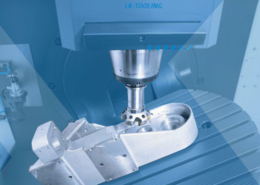