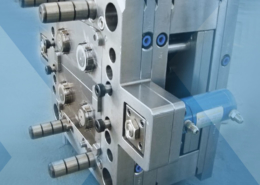
Injection Moulding - one off plastic moulding
Author:gly Date: 2024-10-15
With a metal printer, OECHSLER produces tools on demand - with complex cavities or conformal cooling shortening product innovation cycles.
High-precision polymer parts rely on the accuracy of the tools used in production. Thus, tool design is an integral part of our injection molding excellence. Our skilled in-house tool shop produces more than 100 tools per year. The process includes application engineering and tool design, digital simulation, Rapid Prototyping utilizing Additive Manufacturing and first sample testing, delivering high-precision tools for series production.
OECHSLER operates a fully automated polymer injection molding production at five sites in Europe, North America, and Asia-Pacific. In addition to customer benefits in terms of cost and flexibility, we minimize our product carbon footprint through local production. At the same time, the sites ensure the highest level of quality throughout the entire production network.
STRAUSS teamed up with OECHSLER to rethink existing workwear and manufacture knee pads fully driven by additive manufacturing technology.
Together with OECHSLER and Carbon, Jack Wolfskin revolutionized the backpack market and delivered a perfect back pad solution.
With a metal printer, OECHSLER produces tools on demand - with complex cavities or conformal cooling shortening product innovation cycles.
Bicycle saddles manufactured using Particle Foam. The combination of the injection-molding process and the subsequent "Patch Pro" process allows for maximum comfort. The product can be manufactured in Germany thanks to high automation.
We believe product excellence comes down to every detail. Thus, our development team of more than 120 engineers delivers innovative approaches to products and processes. Those are ideated in design-thinking workshops by our cross-functional teams, and then aligned with the ideas and specifications of our customers to ensure outstanding products.
As part of our development process, we use the digital product and process simulation to rethink the design and enhance the functionality of customer-specified products. Depending on your challenges, we also offer design-to-manufacturing, design-to-cost, and design-to-carbon-footprint services. Leveraging the technical benefits of Additive Manufacturing, we use Early and Rapid Prototyping to facilitate iteration loops with our customers.
Our customers benefit from a global production network with 400 injection molding machines and 40 corresponding assembly lines in Europe, North America, and Asia. Our quality management system (QMS) assures standardized machinery, equipment and material operation that meet all quality standards of the automotive and healthcare industry at all global sites.
We provide sophisticated solutions, based on 20 years of experience in actuator development, prototyping, and manufacturing.
TECHART and OECHSLER enable superior design and seating comfort for high-performance cars with additively manufactured upholstery.
PCS Company mold components are designed and manufactured to exceed demanding customer expectations for quality, reliability, and performance. With an extensive product selection supported with superior customer service, you can count on PCS to meet your needs.
OECHSLER operates a diverse material portfolio to exceed the wide-ranging quality standards of our customers. That includes proven polymer solutions for cost-efficient mass production and the most durable, high-performance polymers that add up to more than 10,000 tons of granules per year. Due to our profound testing approach, we can ensure the best durability and resistance characteristics.
Highly complex system component consisting of various components (polymer/metal) combined in an injection molding process manufactured in compliance with automotive specifications.
OECHSLER created data-driven transparency on its Product Carbon Footprint and identified the biggest source of emission.
As a turnkey partner, OECHSLER provides profound manufacturing expertise and, therefore, can offer a cross-manufacturing approach that is individually designed depending on product properties and customer needs. That may include a combination of materials or production technologies, for example:
We provide sophisticated solutions, based on 20 years of experience in actuator development, prototyping, and manufacturing.
Ceramic Injection Molding combines functionality and design for high-quality parts with excellent material characteristics and haptics.
With more than 70 years of experience in high-volume production, OECHSLER is firm in setting up the ideal manufacturing infrastructure for our customers. That includes in-house toolmaking to ensure the highest product quality and accuracy. Depending on customer needs, we also offer failure path detection (FMEA), risk analysis, and Advanced Product Quality Planning (APQP) services. Utilizing a comprehensive toolkit, we provide fully automated manufacturing and assembly.
Inhaler for medical applications produced in clean room conditions ISO - class 7 under consideration of highest quality requirements.
As a full-service provider with more than 70 years of experience, we at OECHSLER understand that our customers only require the perfect polymer solutions. Thus, we design and engineer forward-driven, high-precision, and top-notch products customized for your industry. Those can be realized in high-volume series production with the machinery of up to 7000 kN of clamp force. Throughout our global production network, we set the highest standards regarding product quality and operational excellence. This is validated by profound product and material testing and 100% end-of-line testing.
Specialized, Carbon & OECHSLER rethink bike saddles by using latest scientific results and innovative production technologies.
Polymer-based and injection-molded face shield for firefighting operations at high temperatures. The face shield is gold plated in a finishing process to increase resilience.
OECHSLER enables the 3D placement of patches, to individualize or add design elements to a 3D component or to stiffen a 3D component.
GETTING A QUOTE WITH LK-MOULD IS FREE AND SIMPLE.
FIND MORE OF OUR SERVICES:
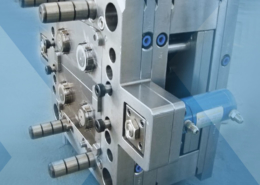
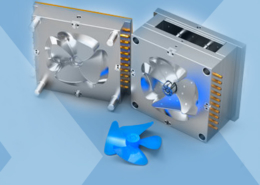
Plastic Molding

Rapid Prototyping
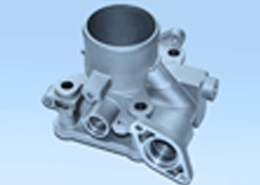
Pressure Die Casting
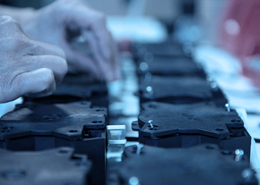
Parts Assembly
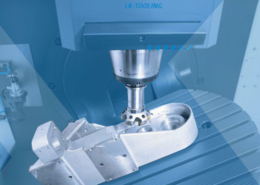