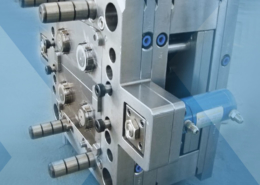
Injection moulding - molds for plastic
Author:gly Date: 2024-10-15
One of the key drawbacks of aluminum molds is their inability to be polished to the same degree as steel molds. This limitation can affect the surface quality and dimensional accuracy of the molded parts, making them less suitable for applications where a pristine finish is essential.
When working with aluminum, a common challenge arises: aluminum tends to adhere to the tool, resulting in the formation of built-up burrs. This adhesion issue can significantly impact the machined surface’s smoothness and dimensional accuracy due to alterations in the tool’s size and shape. Consequently, the quality and dimensions of plastic products are compromised as a result.
One of the standout features of aluminum is its exceptional cutting speed. The fast machining capabilities of aluminum significantly reduce processing time. This, in turn, translates to cost savings and shorter production cycles. In fact, aluminum molds can be processed in approximately one-third to one-half the time required for steel molds.
Given these challenges, those seeking aluminum molds are often advised to collaborate with specialized manufacturers who have expertise in creating and working with aluminum molds. Despite their advantages, aluminum molds have not gained widespread popularity over the years, emphasizing the importance of finding skilled professionals when choosing this mold type.
Moxietec is equipped with an innovative, world-class research team, one of the largest 5-axis CNC mills on the east coast, and the capacity to design and machine molds in-house.
Greater Care and Precision Required: Using aluminum molds demands a higher degree of care and precision from production staff. They need to be vigilant and proactive to avoid potential problems. Any accidents or mistakes can result in monetary losses for the company.
Aluminum is relatively affordable when compared to other mold materials. While the price per unit weight may not be the lowest, the cost per unit volume is notably lower than many mold steels. This affordability makes it an attractive choice for manufacturers on a budget.
Our robust, patented foamingtechnology can accommodate high levels of recycled content to produce highly repeatable parts.
Within our 50,000 sq. ft. facility, we are well equipped with state-of-the-art equipment including injection molding machines and CNC machines. In addition, our lab can provide numerous testing services. By housing everything under one roof, we can efficiently provide total package solutions.
Aluminum injection molds do not signify the complete mold is constructed from aluminum; rather, it means that the mold’s core and cavity are crafted from aluminum, while the mold base remains constructed from steel. This approach offers a valuable advantage in maintaining mold rigidity. The steel mold base provides essential support to the mold core, ensuring structural stability. Simultaneously, the mold core often features intricate shapes, making its fabrication more complex. In contrast, the mold base’s manufacturing process is relatively straightforward, allowing for the retention of necessary mold rigidity while minimizing processing time.
When it comes to selecting aluminum for injection molds, it’s important to acknowledge that aluminum’s mechanical properties, including strength, hardness, and rigidity, typically don’t measure up to those of materials like 1045 steel or pricier alloy steels.
The last step to providing a Turnkey solution is optimizing the Moxietec process for each specific mold. Our skilled engineers will prototype the product to ensure a great quality part is produced every cycle. Process optimization starts with a good foundation which is why Moxietec’s vertical integration across all aspects of the process was brought in-house. We understand that a robust process starts with a good part design, a precise mold, and a compatible material formulation. Through years of research and development, we have created a process that is widely accepting of many polymers and demonstrated that large amounts of recycled content can be processed with repeatability. We are committed to continuously improving our technology in order to deliver the new standard of foam injection molding capabilities for many years to come.
Considering the approximately 30% cost savings offered by aluminum molds, it becomes essential to weigh the pros and cons. While aluminum molds provide significant cost advantages, it’s important to remember that steel molds have a significantly longer lifespan, often lasting hundreds of times longer than their aluminum counterparts. The choice ultimately depends on the specific needs and budget of the project at hand.
If you were to ask a random plastic molder, you’d often find a reluctance to opt for aluminum injection molds. Several factors contribute to this hesitation:
However, mold longevity is also influenced by the acceptance of flash, which refers to the presence of excess material at the parting line of the molded product. If strict requirements for flash-free production are in place, it can shorten the mold’s lifespan.
In the world of injection molding, choosing between aluminum and steel molds requires a careful evaluation of cost savings and production challenges. While aluminum molds offer affordability and quicker processing, they demand a more cautious approach and have shorter lifespans compared to steel molds. The decision ultimately depends on the specific project requirements, budget considerations, and the willingness to navigate the intricacies of aluminum molds for optimal results.
Aluminum’s poor welding performance and difficulty in polishing make it challenging to repair molds once flaws occur. This can result in increased maintenance costs and downtime.
Challenges During Mold Trial and Production: Aluminum injection molds can pose challenges during mold trials and production runs. Issues like plastic products sticking to the mold or plastic remnants clinging to the sprue’s tail can arise. These problems can lead to mold damage, flash formation, or other production hiccups. Repairing these issues in aluminum molds can be more complex than with steel molds.
Aluminum injection molds have long been considered an attractive option for various manufacturing processes, primarily driven by cost considerations and the need for shorter turnaround time.
Our company showcases top-of-the-line tool cutting machinery, including one of the largest 5-axis CNC mills on the East Coast. Designs can be seamlessly transferred from our mold designers to machinists for faster lead times. Constant communication between departments helps ensure fewer mistakes and less rework on the molds. Molds are then inspected utilizing high precision verification systems before being released to pilot production. Moxietec can also bring in previously fabricated molds and use 3D scanning to reverse engineer damaged or unoptimized molds and restore them to be compatible with the Moxietec process. We prioritize root cause analysis over fast, band-aid fixes.
When considering aluminum injection molds, cost savings can be substantial. While the material itself is less expensive, the primary source of savings lies in reduced processing time. In general, aluminum molds tend to be 20-40% cheaper than their steel counterparts.
Unfamiliarity with Aluminum Molds: Many mold workers are not well-versed in the intricacies of aluminum molds. They may lack experience and familiarity with the material, which makes them hesitant to use it.
The key to a short cycle time and excellent part quality is understanding the fundamentals of mold design. Our mold designers understand the science behind crafting an optimal mold to fit the needs of our proprietary process. As our technology evolves, our mold designers are available for short feedback loops to implement the latest and greatest technology into the next generation of our foam injection molds. All mold designs are passed through a rigorous review process where each component of the mold is carefully analyzed. This helps ensure faster and better product launches.
One or more Moxietec products may be covered by one or more of the following U.S. patents or related foreign patents; or U.S. patents pending or related foreign patents pending:
Choosing the right material for a product is quintessential for success. Every polymer is unique and Moxietec is invested in understanding how our proprietary process affects the polymers’ foaming behavior. With the ability to create and characterize custom compounds in-house, the perfect material for your project can be created. Already have a material in mind? Not a problem! Each material that comes through the door is verified through a series of thermal analysis procedures to determine its foamability and compatibility with our proprietary process. Our scientists use this data to make any necessary tweaks to the material recipe for further formulation optimization.
Moxietec is an American plastic injection molding company that manufactures innovative recycled foamed parts in a wide range of thermoplastic materials.
Compared to steel, aluminum has inferior mechanical properties and is less capable of withstanding high-injection speed and high-pressure conditions. This limitation can lead to flashings, even in new molds. Therefore, aluminum molds are best suited for applications involving simple product designs, materials with high fluidity, and lower temperature and pressure requirements. Materials like ABS and PP are well-suited, while materials like PC and glass fiber-reinforced plastics are less compatible due to their higher temperature and pressure demands.
Aluminum boasts impressive thermal conductivity, facilitating efficient heat dissipation. This characteristic helps maintain the optimal mold temperature, preventing issues like slow mold ejection, excessive product shrinkage, and warping due to inconsistent cooling. As a result, aluminum molds are well-suited for applications where precise temperature control is crucial.
While aluminum molds are not a new concept and have been used in the past, they haven’t gained widespread popularity in recent years. In this article, we will explore the advantages and disadvantages of aluminum molds to understand why their usage has fluctuated over time.
Therefore, the preference often leans toward aluminum variants with greater hardness. While aviation-grade aluminum 7075 is a viable option, 6061-T6 is frequently favored due to its considerably more affordable price point.
The lifespan of an aluminum injection mold varies depending on factors such as the material being molded and the complexity of the product. For instance, for a product made from PA6+GF30 with a straightforward design, an aluminum mold can typically produce around 2000-3000 shots. When working with materials like PP or ABS, the number of shots can increase to 5000-10000, assuming no unexpected issues arise during production.
Furthermore, in manufacturing facilities frequently utilizing aluminum molds, the aluminum mold cores may experience shorter lifespans and may need replacement. In such cases, the mold base can be efficiently reused in molds of similar sizes, offering a practical and cost-effective solution.
GETTING A QUOTE WITH LK-MOULD IS FREE AND SIMPLE.
FIND MORE OF OUR SERVICES:
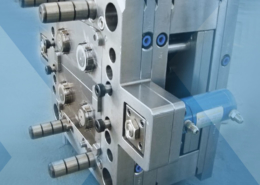
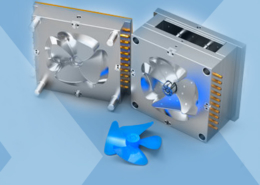
Plastic Molding

Rapid Prototyping
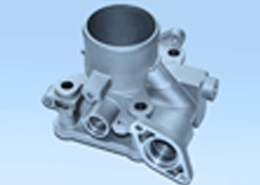
Pressure Die Casting
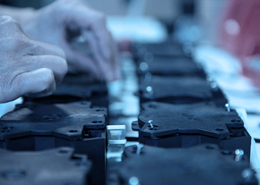
Parts Assembly
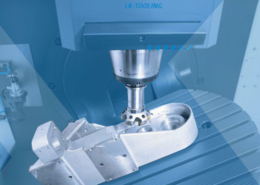