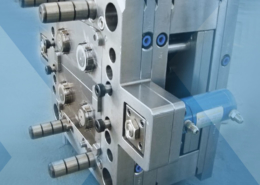
Injection Molding Services for Electrical Manufacturing - electrical plastic mol
Author:gly Date: 2024-10-15
Acrylonitrile butadiene styrene (ABS) is a rigid, lightweight plastic that is both durable and impact resistant. ABS is made up of the three monomers – acrylonitrile, butadiene, and styrene – hence the abbreviation ABS. Each of the monomers plays an important role in the composition of the final plastic. The acrylonitrile gives the final product heat and chemical resistance. The butadiene is used for impact resistance. The styrene provides extra strength and a glossy finish. ABS is used to make appliances, toys, medical supplies, musical instruments, computer parts, and more. One of the most recognizable examples of ABS injection molding is the little plastic LEGO® brick. LEGO® bricks exhibit all the qualities that makes ABS an ideal material for a wide array of projects. LEGO® bricks are tough, scratch resistant, impact resistant, and have a smooth, glossy finish.
A cleanroom is a controlled environment where technicians use equipment and gear to minimize and eliminate pollutants such as dust, microbes, and other airborne particles.
ICOMold by Fathom has the expertise to help meet your ABS injection molding needs. We offer fast and dependable service, low prices, quick quotes, and an online project management system. ICOMold by Fathom can handle projects of any size – from small part or prototype runs to extended part runs in the thousands or even millions.
Medical injection molding is typically conducted in an ISO Class 8 cleanroom. An ISO 8 cleanroom provides air quality levels with an allowable maximum of 100,000 particles (≥0.5 um) per cubic foot of interior air with a minimum of 20 air exchanges per hour.
Spectrum designed the cleanroom to manage the unique challenges of cleanroom molding and workflow. Real-time data capture, process quality monitoring, and in-cavity pressure monitoring are components of this cleanroom’s ultra-modern digital technology framework.
ABS plastic is recyclable. Using a combination of virgin ABS plastic mixed with recycled ABS can help customers reduce overall costs. The ABS is shredded and then purified to remove any undesirable metals or plastics during the recycling process. The leftover product is then analyzed and combined with virgin ABS to produce a new product that is ready for injection molding.
Additionally, standards significantly drive the cleanroom technology and processes needed in medical device manufacturing. Most medical device manufacturing must be conducted in a cleanroom between Class 100,000 (ISO 8) and Class 100 (ISO 5).
ABS plastic begins as a pellet. The pellet is then melted into a moldable state and injected into the cavity of a two-part mold. The plastic will solidify almost as soon as the mold has been filled. The part then cools to the shape of the mold. The mold opens once the plastic has fully cooled and the part is ejected. The mold is closed and the process starts over.
The work area and personnel within the Minneapolis cleanroom conform to environmental control standards through the use of:
Cleanroom molding is vital for industries where precision, cleanliness, and contamination control are paramount. It helps companies meet regulatory standards, produce high-quality, reliable products, and maintain the integrity of sensitive materials. This specialized manufacturing process plays a crucial role in ensuring the safety, functionality, and quality of products in various high-stakes industries.
ICOMold by Fathom is an expert at ABS injection molding and can provide customers of all sizes with a seamless manufacturing process from prototype to production.
ABS injection molding done at a high temperature produces resistance to heat and a smooth, gloss finish. ABS injection molding done at a lower temperature will result in better strength and impact resistance. The final properties and strength of any ABS injection molding product will be influenced by the condition parameters used during the manufacturing process. The experts at ICOMold can help customers select the correct parameters for their next ABS injection molding project.
ABS injection molding offers numerous benefits over other plastic materials. ABS plastic is easy to mold and has good machinability. It has high impact and tensile strength, dimensional stability, stiffness, and excellent stability under load. ABS can maintain its characteristics and performance in extreme temperatures but also has a low melting temperature — making it easy to use when injection molding. ABS can be alloyed with other polymers to achieve desired characteristics. ABS can also be colored for custom pieces and is easy to paint and glue, making it a good candidate for secondary processing.
Keeping the cleanroom environment free from contaminants requires precise control of the area's airflow, temperature, and humidity and strict cleaning procedures for the people, equipment, and materials that pass in and out of the cleanroom.
ABS is a thermoplastic polymer widely used for injection molding. ABS is durable, budget -friendly, and is easy to machine. ABS can be used in conjunction with a metal coating since many metals will adhere strongly to the surface of ABS plastic. ABS plastic has good resistance to extreme temperature and humidity. ABS is perfect for projects that demand strength, stiffness, and impact resistance. ABS is an ideal candidate for secondary processing as it can easily be painted or glued. ABS is also very easy to recycle.
Not all parts require cleanroom injection molding. We also offer injection molding services for lower-risk applications that require a controlled environment but no certification. Do you have any questions about our cleanroom and injection molding services? Contact us for more information.
Our cleanroom facilities are ideal for testing, developing, and assembling highly sensitive parts and products. These parts are made from materials engineered to deliver very specific physical and chemical characteristics.
Our injection-molded solutions include premium, high-quality components and fully assembled medical devices. We have years of experience with complex molding projects working with highly engineered performance medical plastics.
Take a virtual tour at Spectrum Minneapolis. Imagine your next complex, tight-tolerance injection molding, and assembly project becoming a reality with the help of our expert engineers and manufacturing teams.
ICOMold’s fast-turn, low-cost, high-value injection molding enhanced by joining Fathom’s manufacturing platform. Learn More
Many medical devices come into contact with or are inserted into the human body. Therefore, manufacturers must utilize the highest standards of precision and cleanliness when producing medical device products to ensure the safety of patients.
Cleanrooms are classified into different levels, depending on the “allowable” amount of particles (contaminants) in the space. This is conveyed as the number of particles per cubic meter.
Our external audits have always confirmed our high-quality standards. An external certified professional verifies our airflow, filter flow, and bioburdens. We are ISO 14644 certified, and our cleanrooms are suited for manufacturing various types of medical devices.
ABS plastic should not be used under direct sunlight or near an open flame. Fire-retardant and heat-resistant grades of ABS are available. Some ABS components can emit toxic fumes after heating.
GETTING A QUOTE WITH LK-MOULD IS FREE AND SIMPLE.
FIND MORE OF OUR SERVICES:
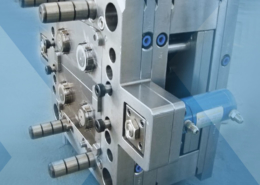
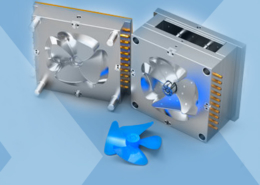
Plastic Molding

Rapid Prototyping
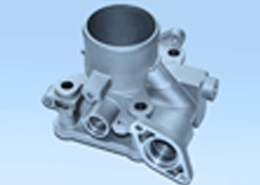
Pressure Die Casting
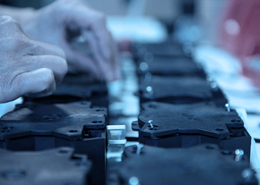
Parts Assembly
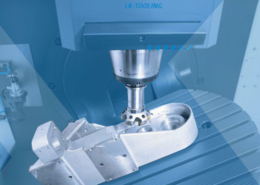