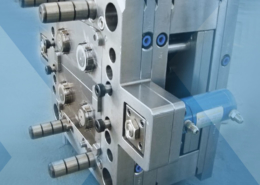
Injection Molding Services for Custom Parts - plastic injection molding part
Author:gly Date: 2024-10-15
At EnviroTech Custom Injection Molders, we assist our customers with anything from the most diminutive part to the largest injection molded components. But, when working on substantial components – heavy, thick-walled or especially large – we have capabilities that you may not find elsewhere in the industry.
Our strict and exacting quality control processes allow us to provide consistently high-quality results without sacrificing time or economy. With our ability to customize injection molding solutions for our customers, you get the results you demand, time after time.
The author gratefully acknowledges the permission of John Wiley & Sons, Inc., New York, to use material from his book Injection Molding, Theory and Practice (1973). Mr. Rubin is president of Robinson Plastics Corp.
When you need the best heavy, large or thick wall molding services, call on the experts at EnviroTech for all your bulk and custom injection molding needs.
EnviroTech’s unique proprietary bulk injection molding process allows EnviroTech to manufacture and produce large thick-walled polymer components that are simply impossible for other injection molders.
Our company is known around the world as the industry leader in thick-walled injection molding. We have one of the largest shot capacities in the industry, allowing us to produce exceptional quality thick wall molding components that are void-free. We also design, engineer and manufacture large shot and thick-walled molds.
Heavy injection molding uses a variety of space-age materials and additives to achieve the weight you need. Our processes ensure timely production and exacting standards of quality as well as the affordability you enjoy with standard injection molded products.
As the leading large part injection molder in the United States, EnviroTech designs, engineers and produces large injection-molded polymer resin components. Our streamlined processes and in-house production facility allow us to complete massive production runs quickly and affordably.
Injection molding is a major processing technique for converting thermoplastic materials, accounting for almost 20% of U.S. resin production.
We assist customers across virtually every sector and industry, including defense, mining, energy, oil and gas, agriculture, automotive, and deep-sea drilling rigs. We specialize in mold design, polymer resin engineering, mold optimization and troubleshooting, and custom injection molding of all types.
We have assembled a substantial collection of state-of-the-art equipment at our in-house design and production facility. Using cutting-edge technology and a half-century of experience, we have the ability to produce extremely large, heavy and thick-walled injection molded components.
Our technology and sophisticated automation capabilities allow us to complete even the most massive thick wall molding production runs quickly without compromising quality output. Even complex components are no match for our experience and capability.
Using thermoplastics and polymer resins, EnviroTech has the ability to manufacture substantial components that have all the benefits of polymer injection molded parts – reduced cost, quick turnaround, minimal environmental impact – as well as the desired weight.
Rubin, I.I. (1991). Injection Molding of Thermoplastics. In: Berins, M.L. (eds) SPI Plastics Engineering Handbook of the Society of the Plastics Industry, Inc.. Springer, Boston, MA. https://doi.org/10.1007/978-1-4615-7604-4_5
The basic concept of injection molding is the ability of a thermoplastic material to be softened by heating, formed under pressure, and hardened by cooling. In a reciprocating screw injection molding machine (Fig 5–1), granular material (the plastic resin) is fed from the hopper (a feeding device) into one end of the cylinder (the melting device). It is heated and melted (plasticized or plasticated), and it is forced out the other end of the cylinder (while still melted) through a nozzle (injection) into a relatively cool mold (cooling), held closed by the clamping mechanism. The melt cools and hardens (cures) until it is fully set up. Then the mold opens, ejecting the molded part (ejection).
The process was patented by John and Isaiah Hyatt in 1872 to mold camphor-plasticized cellulose nitrate (celluloid). The first multicavity mold was introduced by John Hyatt in 1878. Modern technology began to develop in the late 1930s and was accelerated by the demands of World War II. A similar surge in the technology of materials and equipment took place in the late sixties and early seventies.
We offer a wide variety of polymer and engineering resin materials for you to choose from. We can recommend the best materials for your needs or, if necessary, we can work with our engineering resin manufacturing partners to design a material formulation just for you.
EnviroTech has over 50 years of experience and expertise in the injection molding space, optimizing part design for mold-ability and polymer resin engineering. With presses ranging from 850 – 2500 tons, and our experienced process control techniques that give us the ability to mold virtually any thermoplastic polymer resin and additive composition (see Polymer Resin Section), that opens the door to products for metal replacement and a wide range of industrial applications that were never before believed possible.
Our expansive facility operates around the clock to meet our customers’ needs. And, although we consistently meet the needs of our clients, we always strive to exceed their expectations.
GETTING A QUOTE WITH LK-MOULD IS FREE AND SIMPLE.
FIND MORE OF OUR SERVICES:
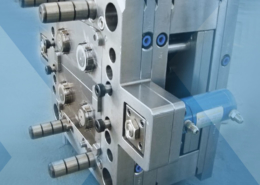
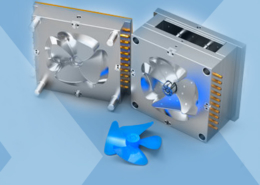
Plastic Molding

Rapid Prototyping
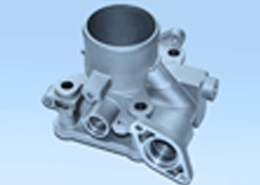
Pressure Die Casting
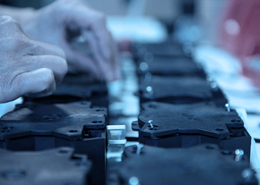
Parts Assembly
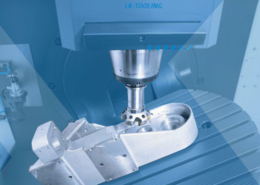